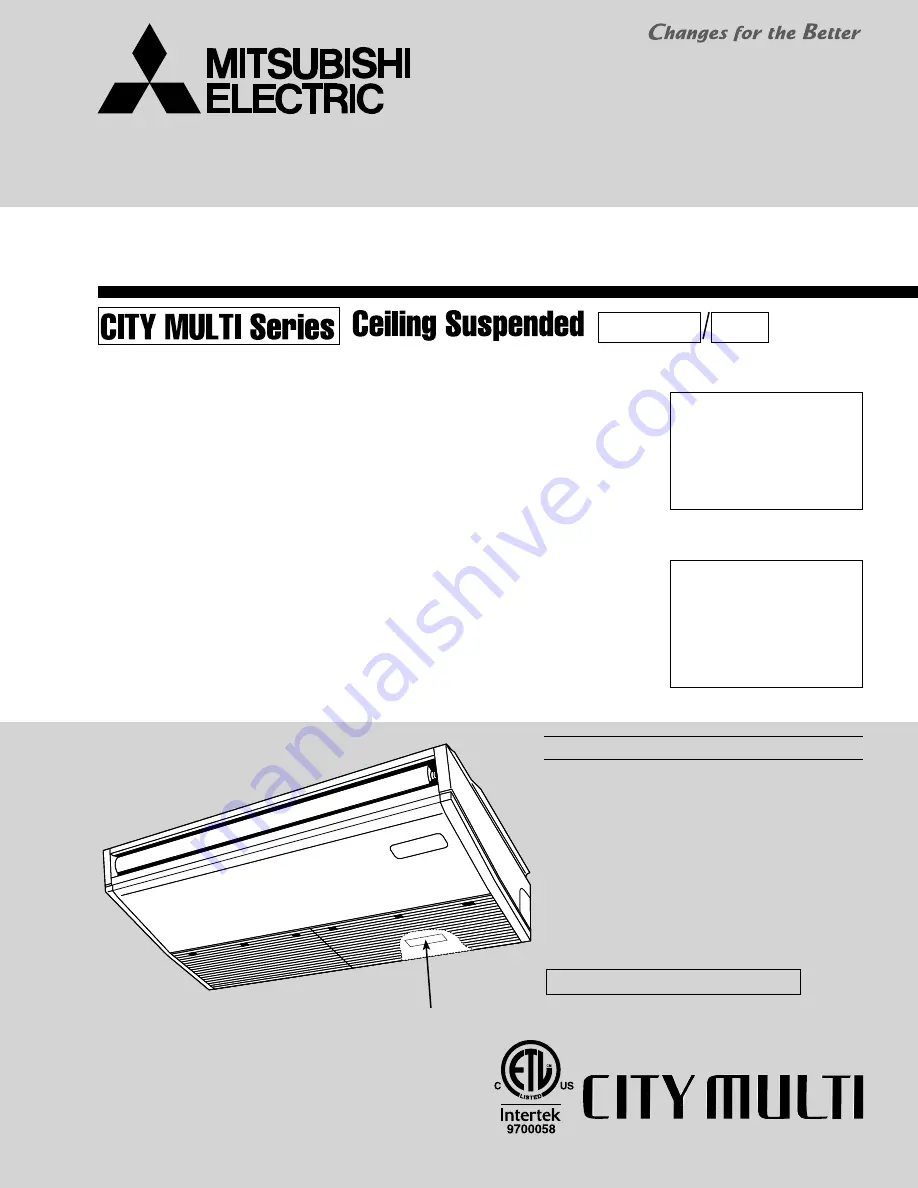
TECHNICAL & SERVICE MANUAL
CONTENTS
1. TECHNICAL CHANGES ......................... 2
2. PART NAMES AND FUNCTIONS .......... 2
3. SPECIFICATION ..................................... 4
4. OUTLINES AND DIMENSIONS .............. 8
5. WIRING DIAGRAM ............................... 11
6. REFRIGERANT SYSTEM DIAGRAM ........13
7. MICROPROCESSOR CONTROL...............14
8. TROUBLESHOOTING .......................... 21
9. DISASSEMBLY PROCEDURE ............. 30
Indoor unit
[Model names]
[Service Ref.]
No. OCH500
REVISED EDITION-A
INDOOR UNIT
R22
R410A
Note:
•
This manual describes only
service data of the indoor
units.
•
RoHS compliant products
have <G> mark on the spec
name plate.
April 2012
PARTS CATALOG (OCB500)
Model name
indication
SPLIT-TYPE, HEAT PUMP AIR CONDITIONERS
PCFY-P15NKMU-E
PCFY-P24NKMU-E
PCFY-P30NKMU-E
PCFY-P36NKMU-E
PCFY-P15NKMU-E.TH
PCFY-P15NKMU-ER1.TH
PCFY-P24NKMU-E.TH
PCFY-P24NKMU-ER1.TH
PCFY-P30NKMU-E.TH
PCFY-P30NKMU-ER1.TH
PCFY-P36NKMU-E.TH
PCFY-P36NKMU-ER1.TH
Revision:
• PCFY-P15/24/30/36NKMU-
ER1 have been added in
REVISED EDITION-A.
• Some descriptions have
been modified.
• Please void OCH500.