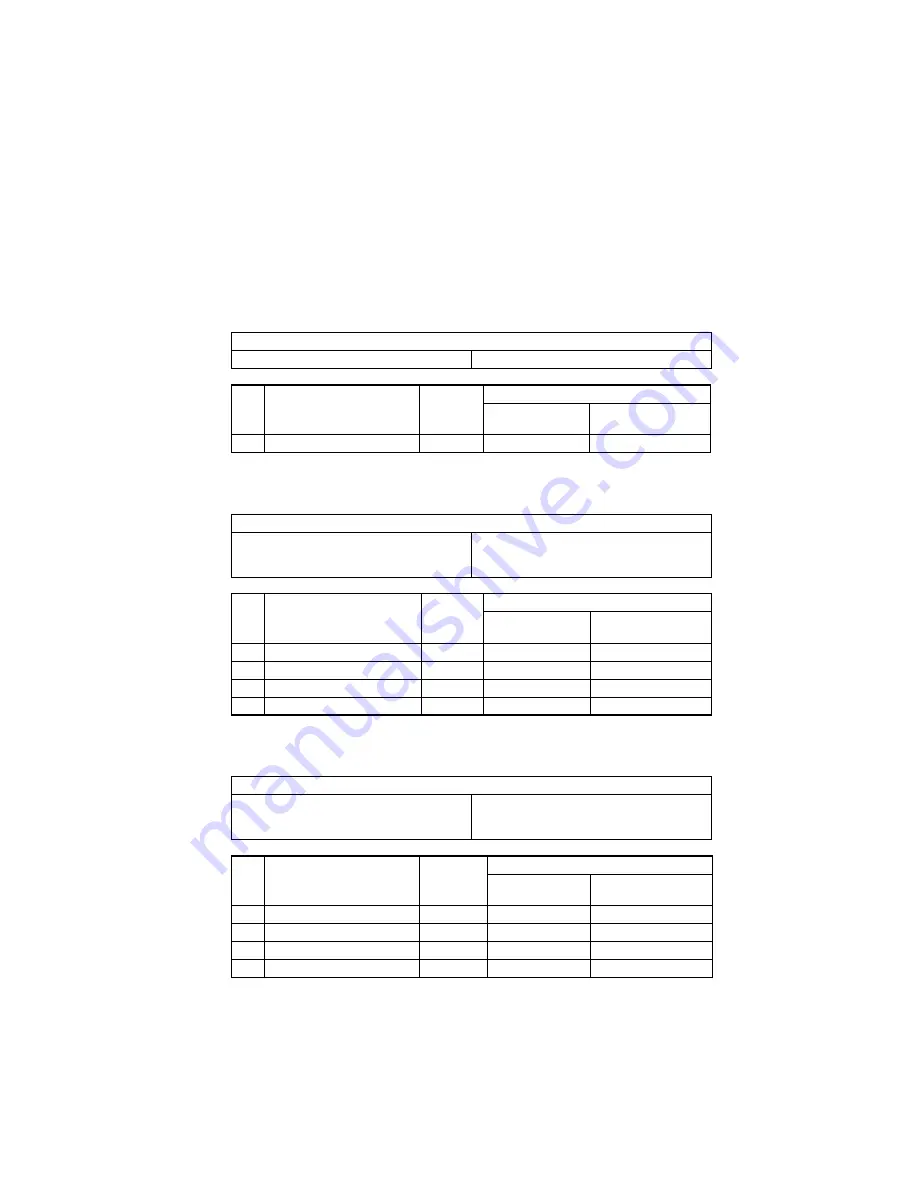
130
3-1.
Malfunction detection timing and remedies
• If the problem cannot be corrected by the user, a service code is displayed.
(1)
FATAL ERROR CODE 04H: Malfunction of the master board
<Remedy>
(2)
FATAL ERROR CODE 08H: Malfunction of the main motor
<Remedy>
(3)
FATAL ERROR CODE 0BH: Malfunction of the ventilation fan motor
<Remedy>
Components for display of the warning
Master board (PWB-A)
Step
Remedy
Reference
page
WARNING DIAGRAM
Control signal
Location(electrical com-
ponent)
1
Replace PWB-A.
-
-
-
Components for display of the warning
Main motor (M1)
Master board (PWB-A)
Power unit (PU)
Controller control board (PWB-P)
Step
Remedy
Reference
page
WARNING DIAGRAM
Control signal
Location(electrical com-
ponent)
1
Check M1 operation.
T-3
M1_REM
5-A
3
Replace PU.
-
-
-
4
Replace PWB-A.
-
-
-
5
Replace PWB-P.
-
-
-
Components for display of the warning
Ventilation fan motor (M6)
Master board (PWB-A)
Power unit (PU)
Controller control board (PWB-P)
Step
Remedy
Reference
page
WARNING DIAGRAM
Control signal
Location(electrical com-
ponent)
1
Check M6 operation.
T-3
M6_REM
3-E
2
Replace PU.
-
-
-
3
Replace PWB-A.
-
-
-
4
Replace PWB-P.
-
-
-
Summary of Contents for magicolor 2300 Series
Page 1: ...magicolor 2300 Series Service Manual 1750058 001A...
Page 6: ...6...
Page 7: ...7 SAFETY...
Page 8: ......
Page 23: ...23 GENERAL...
Page 24: ......
Page 32: ...32...
Page 33: ...33 MECHANICAL ELECTRICAL...
Page 34: ......
Page 75: ...75 DISASSEMBLY ASSEMBLY 19971...
Page 76: ......
Page 106: ...106...
Page 107: ...107 CONTROL PANEL SER VICE MODE DESCRIPTIONS...
Page 108: ......
Page 117: ...117 TROUBLESHOOT ING...
Page 118: ......
Page 128: ...128 3 Replace PWB A...
Page 139: ...139 INDEX...
Page 140: ......