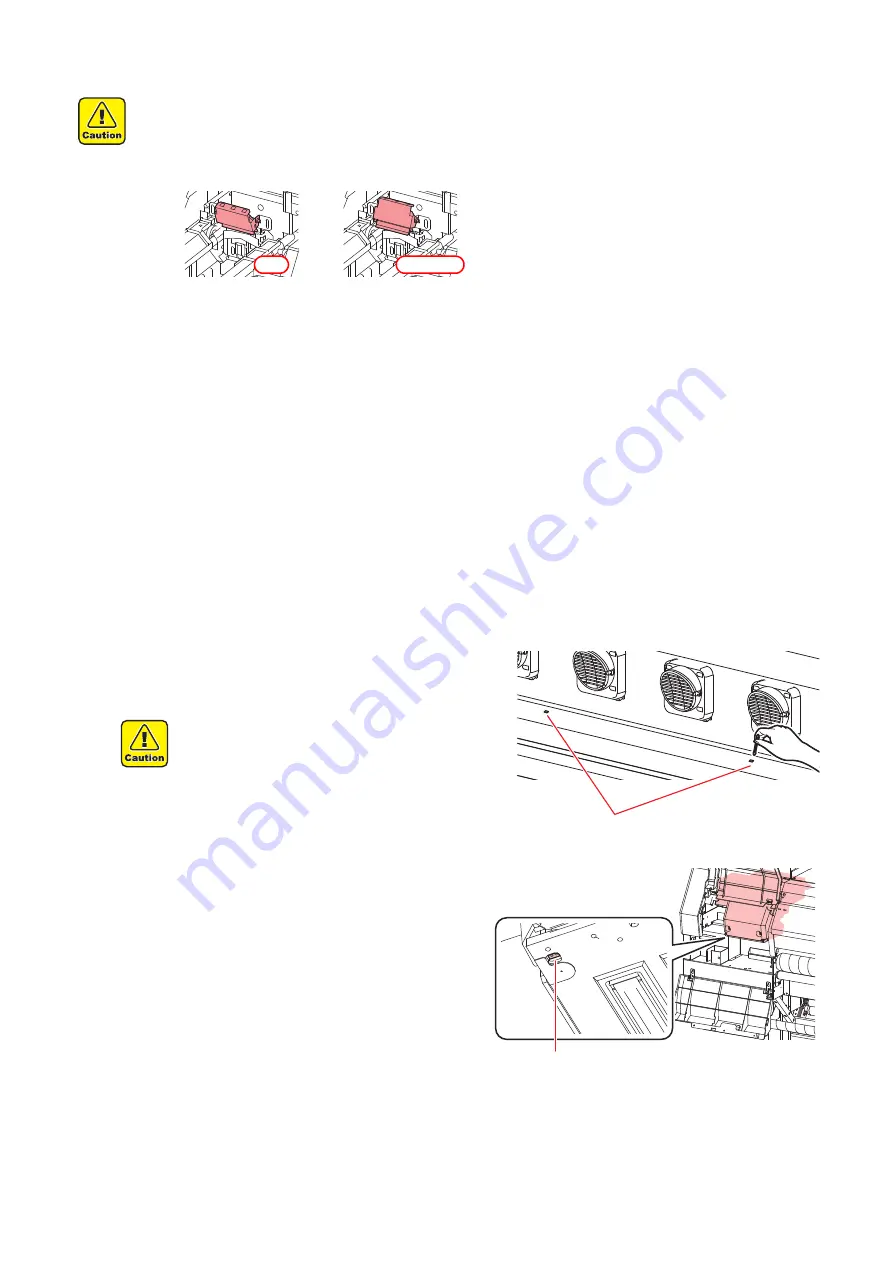
7
Further, in the cases as explained below, replace the wiper with the new one (SPA-0271) in accordance with
"Replacing the wiper" on Chapter 4 of the Operation Manual.
• When the wiper is deformed
• When the stuck ink can not be wiped off
• When the warning for wiper replacement is indicated
(4) Fabric retainer / Media press (“Cleaning the Fabric Retainer / Media press” Chapter 4
of the Operation Manual)
When the cut dust of the media and other dusts accumulate between the media holder and the platen, it could
cause the risks that the transfer of the media could not be performed properly or such dusts stick to the noz-
zles and this could interfere the proper printings. You are recommended to clean it frequently.
(5) Media sensor ("Cleaning the Media Sensor" Chapter 4 of the Operation Manual)
The media sensors are located on the platen in the
backside and the bottom surface of the head.
If the dusts and ink accumulate on the sensor, it could
cause false detection of the media or the register mark.
Wipe off the sensors with soft cloth or clean sticks.
• Do not remove the wiper cleaner from the bracket.
• Only clean the front surface on the wiper cleaner's
wiper. (You do not need to clean the rear surface.)
• After the wiper cleaner cleaning, make sure that the
cleaner is not facing up.
• For the cleaning of the media sensors,
never use the solvent.
• When the sensor is heavily stained, wipe
off with a cloth soaked in the waterdiluted
neutral detergent.
OK
Not Good
The backside of the machine
The lower surface of the head
Media sensor
Media sensor