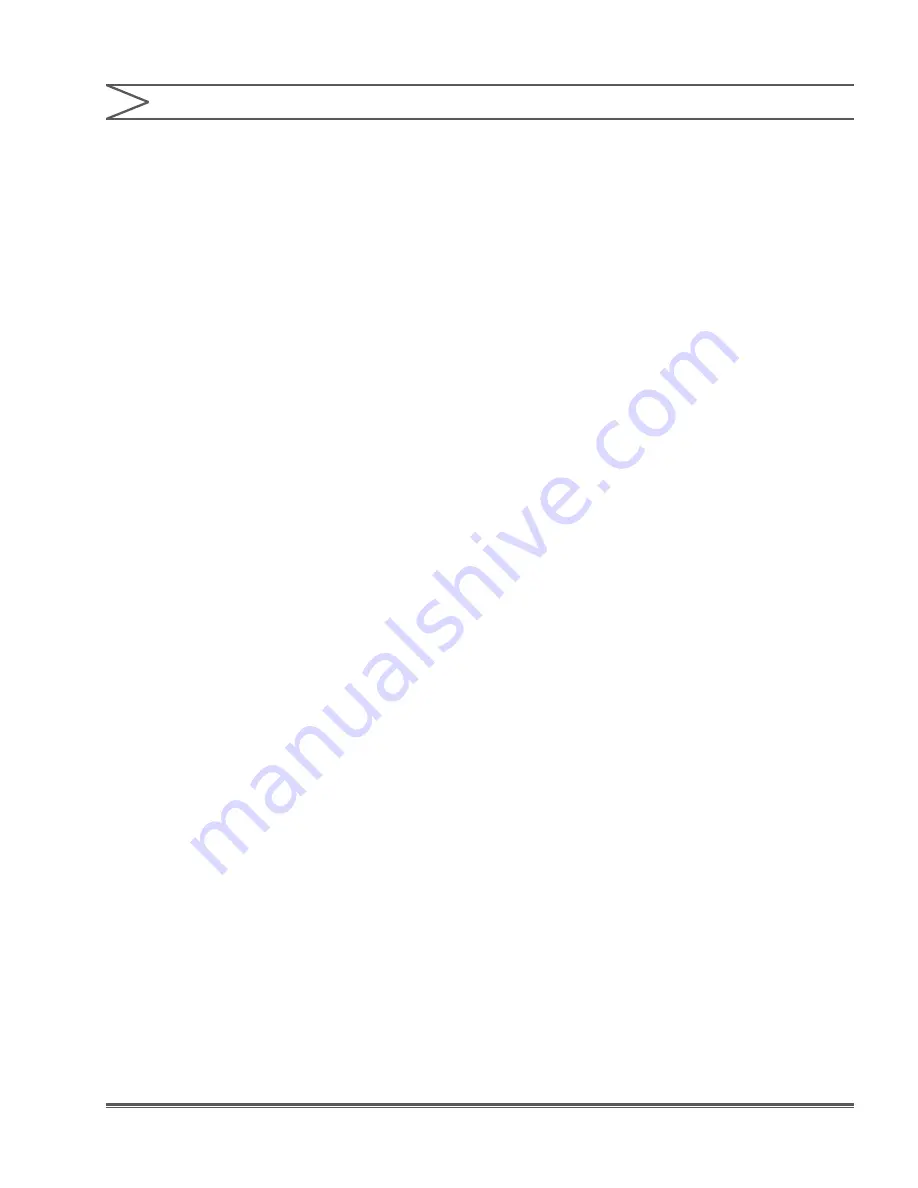
2
Instruction Manual
SECTION 1 - DESCRIPTION
In the Milroyal
®
pump, the pulsating plunger thrust
load is applied directly onto the capacity control,
through the adapter shaft (1320) which must be
capable of opposing this pulsating force without
moving. Air, which is compressible, cannot be used
directly to load the large area side of the Actuator
piston to oppose this pulsating load. Therefore,
the air pressure established by the Moore Valve
Positioner is changed to an equivalent hydraulic
pressure. To accomplish this, the oil in the reservoir
is pressurized by the air pressure from the Moore
Valve Positioner and the oil is routed internally from
the reservoir through the transfer shaft to the large
side of the Actuator Piston. To effectively prevent
movement of the stroke adjustment when the
plunger thrust load is applied, an oil check valve
is required to prevent flow back from the hydraulic
cylinder(1240) to the reservoir. This valve action
is obtained where the actuator shaft (1100) bears
against the Actuator Piston.
The Actuator Shaft retention in the Actuator Piston
allows for approximately 0.005 to 0.020 inch
(0.127 to 5.080 mm) lost motion and is spring
loaded for Actuator shaft-piston contact. On the
suction stroke the thrust reversal overcomes the
spring force and separated the surfaces to open the
oil passage between the reservoir and the hydraulic
piston-cylinder, thus permitting readjustment of
the piston position. Then at the end of the suction
stroke, these surfaces are brought into contact to
close this passage and create a closed hydraulic
cylinder with an incompressible fluid to hold the
Actuator Piston position on the next pressure
stroke.
When the oil pressure in the transfer shaft passage
is 5-10 psi (34.5-68.9 kPa) higher than the oil in the
hydraulic cylinder, the spring loaded check valve
in the adapter shaft will open to supply oil to the
hydraulic cylinder. This oil valve bypass is used
to increase the speed of response when reducing
stroke position and to provide for control movement
when the pump is not operating.
A small quantity of oil is continuously bled from the
top of the hydraulic cylinder and routed internally
to the bottom of the oil reservoir. This bleed flow
also tends to increase the speed of response when
increasing stroke position.
The Transfer Shaft (1220) is extended through
the reservoir into the transparent Plastic Cylinder
(1430) so that this shaft is also used to transmit
the position of the Actuator Piston to the Range
Spring (1430). The transparent cylinder provides
a direct visual indication of the actual position of
the actuator piston by comparing the position of the
ring groove in the Range Spring Piston (1380) with
the percent capacity scale on the outside diameter
of the cylinder.
The complete Pneumatic Capacity Control
assembly is mounted on the pump using an
adapter flange clamped on the boss of the housing.
The position of the adapter is adjusted at the factory
to establish the correct stroke calibration and the
control assembly can be removed for servicing in
the field without disturbing this.
1.3 MODEL PRODUCT CODING
Milroyal
®
B pumps can be ordered with or without
a pneumatic capacity control (PCC) unit already
attached. If the PCC is ordered with the pump, it
is indicated in the pump model code by a “PN” in
the 11th & 12th or 13th & 14th positions. The pump
model code can be found on the pump data plate,
mounted to the pump.