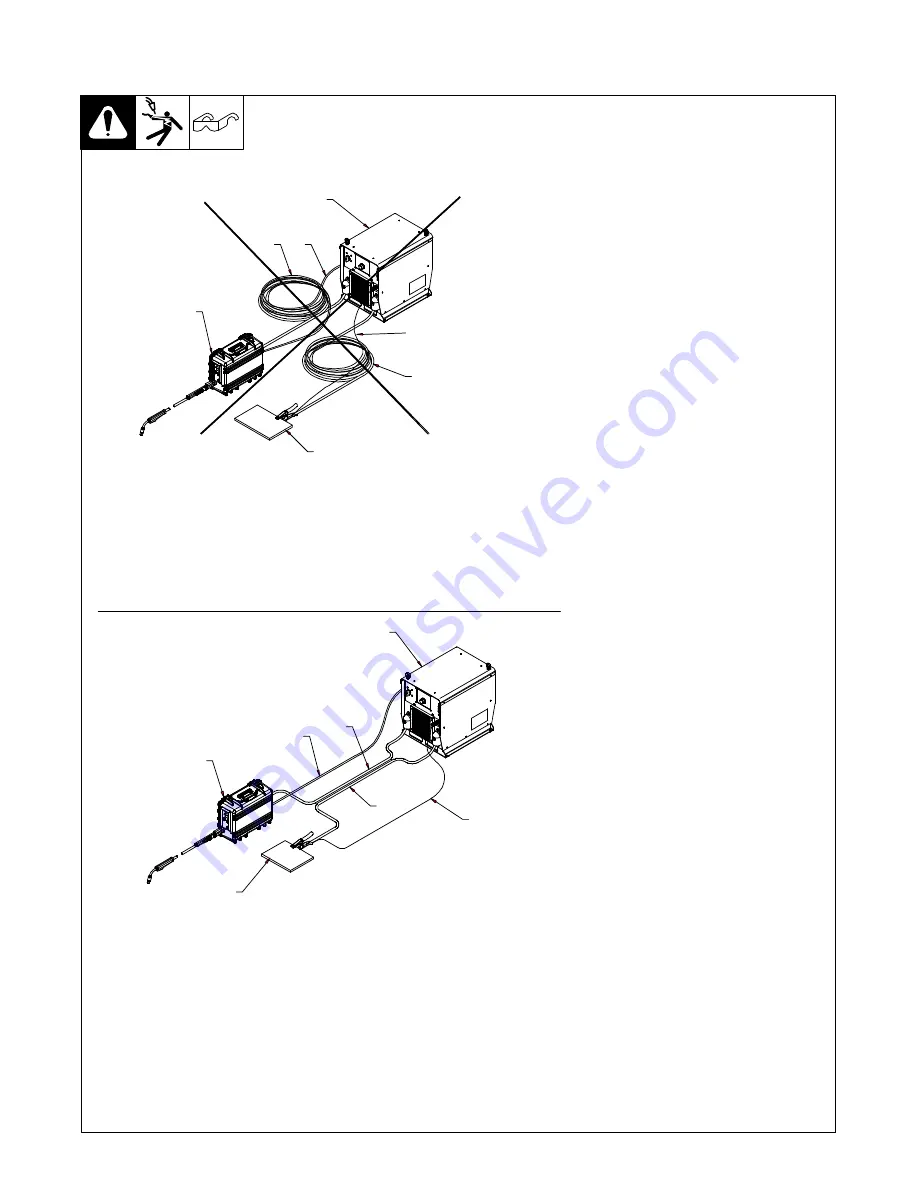
OM-246 466 Page 17
Ref. 243 904-A
1
Welding Power Source
2
Electrode Cable
3
Extension Cable (Optional)
4
Work Cable
5
Volt Sense Lead
6
Wire Feeder
7
Workpiece
The method used to arrange cables has
a significant affect on welding
properties. As an example, RMD
welding process can produce high
welding circuit inductance depending
on cable length and arrangement. This
can result in limited current rise during
droplet transfer into the welding puddle.
The electrode sense lead is contained
in the feeder control cable and is
enabled for all processes. The work
sense lead connects to the welding
power source 4-pin connector located
above the negative output terminal. This
work sense lead automatically compen-
sates for work cable voltage drop when
connected to the welding power source.
Do not coil excess cables.
Use cables
that are the appropriate length for the
application. Whenever using long weld
cables [longer than 50 ft (15 m)] try to
arrange positive and negative weld
cables together to reduce the magnetic
field surrounding the cables. Avoid
coupling the feeder and work sense
leads with the weld cables.
3-10. Arranging Welding Cables To Reduce Welding Circuit Inductance
(Suitcase Feeder)
Bad
Ideal
S
DO NOT coil cables
S
DO NOT share work clamps (no more than 1 machine per clamp)
S
DO NOT tangle cables from different machines
S
DO NOT splice weld cables
S
DO NOT allow volt sense lead braided shield to touch center conductor or workpiece
S
Use shortest cables possible for the job
S
Use proper sized work clamp and weld cables to accommodate peak amperages
S
Separate volt sense lead and feeder control cable from weld cables
S
Place weld cables together if possible
S
Connect work clamp as close to welding arc as possible
1
5
4
2
3
6
7
1
2
3
4
5
6
7
Summary of Contents for OM-246 466B
Page 14: ...OM 246 466 Page 10...
Page 63: ...OM 246 466 Page 59 Notes...
Page 65: ...OM 246 466 Page 61 243 024 B...
Page 74: ...Notes...