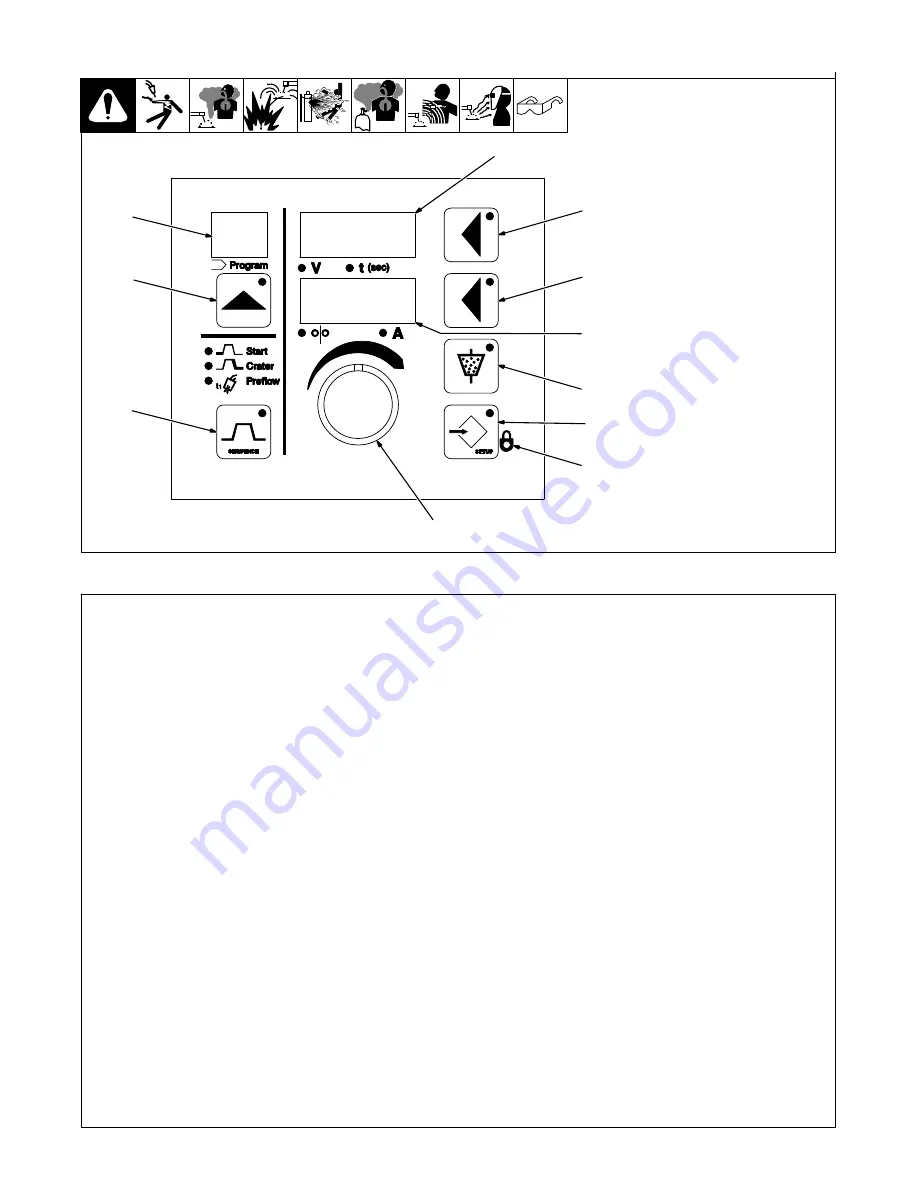
OM-212296 Page 28
6-10. Auxiliary Menus
Ref. 236 564-B
1
Program Display
2
Program Push Button
3
Sequence Push Button
4
Upper Display
5
Upper Display Push Button
6
Lower Display
7
Lower Display Push Button
8
Adjust Control
9
Setup Push Button
10 Flux Push Button
11 Lock LED
1
2
3
4
5
7
6
10
9
8
11
Auxiliary Menus (Continued)
•
Auxiliary Menu
An auxiliary menu is provided when both
the Sequence and Setup buttons are
pressed simultaneously. The Setup and
Sequence button LEDs flash when in the
auxiliary menu. Press the Setup button to
scroll forward, or press the Sequence but-
ton to scroll backwards through the auxilia-
ry menu.
.
To exit auxiliary menu at any time,
press Sequence and Setup simulta-
neously, or press the inch up or inch
down button.
1
Code
Upon leaving the auxiliary menu, the user is
asked if a password code, indicated by
“CODE” in the top display, should be acti-
vated. By default, the code is off, indicated
by “OFF” in the lower display. The user may
enter a numerical password between 0 and
999 by turning the Adjust control. When the
user re-enters the auxiliary menu, the pass-
word code must be selected to gain access
to the auxiliary menu. A failed attempt re-
turns the user to the weld screen and a
counter will increment. The counter in the
program display shows the number of in-
correct attempts. The user has five at-
tempts to enter the correct password code
before being locked out of the auxiliary
menu, indicate by “LOCK”, in the lower dis-
play. After five failed attempts, the power
may be cycled to continue welding, but the
user will remained locked out of the auxilia-
ry menu. Pressing the Program, Sequence,
upper display, and Setup buttons simulta-
neously resets the counter to zero (0),as
shown in the weld screen. When the count-
er is reset,“CODE” is shown in the upper
display, and “RESET” in the lower display.
Pressing the Program, Sequence, upper
display, and Setup buttons simultaneously
again, will reset the unit to the factory de-
faults (see Section on Reset To Factory
Settings), indicated by “WIPE” in the upper
display. Resetting the unit will also turn off
the password code feature.
2
Power Source Selection
The upper display shows “PSS”. The lower
display shows “ON” or “OFF”. Use Adjust
control to select “ON” or “OFF”.
3
Voltage Range Lock
Voltage range lock is active when “LOCK”
is shown in the lower display and the Volts
LED is lit. The voltage range lock is off by
default, and is confirmed by “OFF” being
shown in the upper display. To set a voltage
variance between 0 to 10 volts from preset
voltage, press the upper display button and
rotate the Adjust control to the desired volt-
age. The voltage range lock is program de-
pendent, a different voltage variance may
be locked in for each program and indepen-
dent from the wire feed speed and amper-
age lock.
.
If locks are active, only those programs
with locks are accessible and the lock
LED will be on. To quickly enable or dis-
able the locks for all programs, press
the upper and lower display push but-
tons at the same time.
4
Amperage Range Lock
The amperage range lock is indicated by
“LOCK” in the upper display and a lit Amps
LED. The amperage range lock is set to off,
indicated by “OFF” in the lower display or
0.0 to 250 amperes. The amperage range
lock is program dependant and indepen-
dent for wire feed speed or voltage lock.
.
If locks are active, only those programs
with locks are accessible and the lock
LED will be on. To quickly enable or dis-
able the locks for all programs, press
the upper and lower display push but-
tons at the same time.
5
Wire Feed Speed Range Lock
The wire feed speed range lock is indicated
by “LOCK” in the upper display and a lit
Wire Speed LED. The wire feed speed
range lock is off by default, and “OFF” is
shown in the lower display. To set a wire
feed speed variance between 0 to 250 ipm
(0 to 6.3 mpm) from the preset wire feed
speed, press the lower display button and
turn the Adjust control until the desired wire
feed speed variance is set. The wire feed
speed range lock is program dependent, a
different wire feed speed variance may be
set for each program and independent of
from voltage and amperage locks.
.
If locks are active, only those programs
with locks are accessible and the lock
LED will be on. To quickly enable or dis-
able the locks for all programs, press
the upper and lower display push but-
tons at the same time.