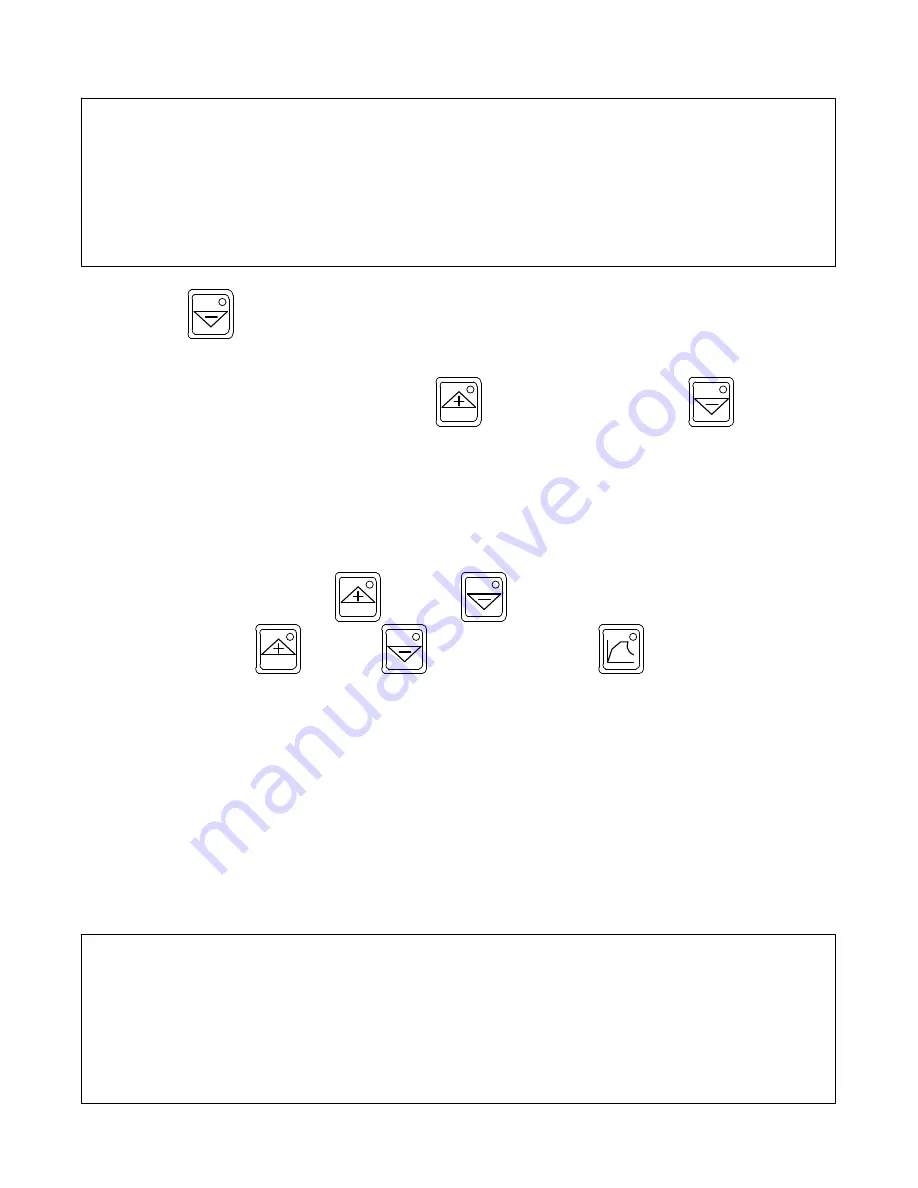
OM-222166 Page 29
Turning off the Decouple Fault allows the system to run with poorly coupled coils. This feature is only available when using liquid cooled cables.
A message will display each time the ProHeat is turned on to remind that the circuit is turned off.
F73: Decoupled/Open Coil
Fault Disabled for
Liquid Cooled Cables Only
Press (−) to Acknowledge
Press the Decrease
button on the front panel to acknowledge the message.
If using a remote On/Off switch, cycling from Off to On 2 times within 3 seconds will also acknowledge the message.
Display Contrast − press and hold the cursor and press the Increase
button to darken, or press the Decrease
button to lighten the
contrast.
.
All parameters in System Setup are considered global, and any changes to the system set-up parameters will apply to all programs.
.
The option to turn backlight on/off was removed at software revision 1.26. Backlight is now always on.
7-4-1.
Factory Defaults
To reset the system back to factory default settings, turn off the power source, and wait until the display goes blank. Turn on the power source. When
the display lights, press and hold the Increase
and Decrease
buttons. A message will display Press Program to reset factory
defaults. Release the Increase
and Decrease
buttons, and press the Program
button.
7-5.
Programming
Programming allows the operator to setup a program for a particular heating process. The selections available are Temperature, Remote, Manual, or
Power vs Time (Time).
7-5-1.
Temperature-Based Control
Temperature-based control operates the system and controls the heating process based on temperature feedback from thermocouple inputs. Ther-
mocouples must be used for this mode of operation or the system will not operate. Within the temperature-based mode there are four different
processes available as follows: Preheat, Bakeout, PWHT (Post-Weld Heat Treat), and Custom Program.
Press the Program button to access the programming mode. Use the cursor button to move the cursor to the desired temperature-based process,
then press the Program button again to select the process.
7-5-1-1. Preheat
The preheat process is a simple method of heating material to a desired temperature and holding that temperature for a specific period of time.
When this process is selected, the following screen will appear on the LCD display:
Mode.......: Preheat
Control TC.:>1
Temperature: 400
Soak Time..: 01:00:00
Preheat Screen