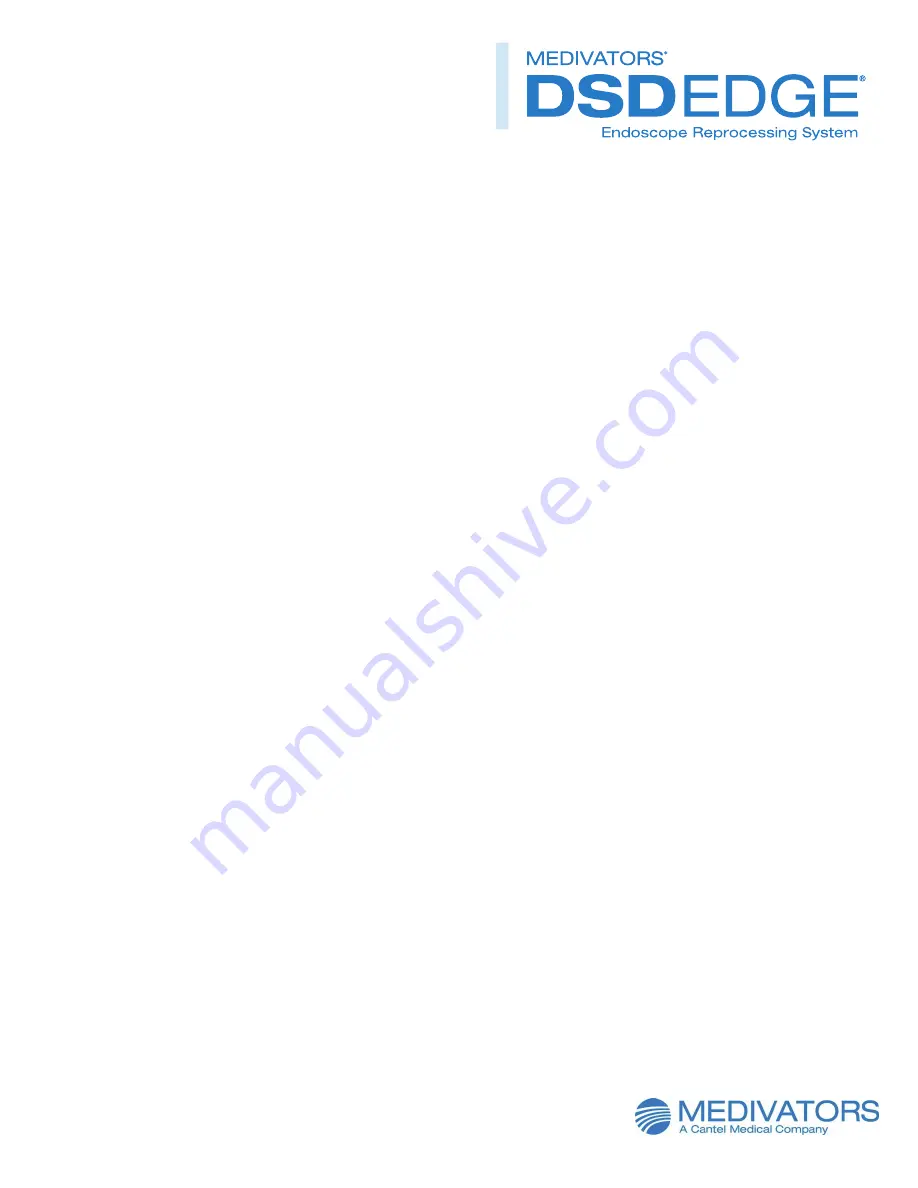
1
ANNUAL PM INSTRUCTIONS
PREVENTATIVE MAINTENANCE KIT
For use with PM Kit 78401-176 120V and 78401-177 230V
Prior to performing the preventative maintenance:
Carefully read through the procedure prior to performing the PM.
Precautions should be taken to prevent spillage of disinfectant when performing the PM.
Personnel should wear the appropriate Personal Protective Equipment (PPE) when performing the preventative
maintenance. Refer to the Material Safety Data Sheet (MSDS) for PPE information.
The machine must be in an idle state prior to the start of the preventative maintenance.
The changing of the 0.2 micron internal water filter, and air filters are not part of the PM procedure. However, if the
filter change times coincide with the PM, they can be performed at this time. Refer to the DSD EDGE operations
manual for instructions on how to change the filters.
Tools Required:
7/16-inch nut driver, open end wrench or socket wrench
9/64-inch, 3/32-inch and 3/16-inch hex keys
Small flat-bladed screwdriver
A set of Phillips screwdrivers
Valve stem wrench for air actuated valves (MEDIVATORS P/N MW03-0002)
John Guest tool (MEDIVATORS P/N 47049-157)
Lint free cloth/rags
Teflon tape
Silicone grease (MEDIVATORS P/N 17599-463)
Torque driver 0-36 in-lb. range
120 Volt Kit 78401-176
PM Kit Part Content
Part number
QTY
Hydraulic Valve Seals
78401-261
1 (Kit of 10 seals)
Solenoid Valve Seal
MV01-0035
4
Peristaltic Tube Set
MT01-0500
4
Check Valves
78401-260
1 (Kit of 8 valves)
Pump Assembly
78400-684
2
Drain Rebuild Kit
78400-658
2
Overflow Rebuild Kit
78400-659
2
Sample Port Seal
41013-001
2
Strainer 43100-254
2
O-rings SSG Reservoir
43100-302
28
Check valve ball for SSG Res
47049-658
4
O-ring Removal Tool
47049-687
1
Instructions 50098-296
1
O-ring MO01-0004
2
Spring for SSG
47049-415
4
Sensor Cover
MC13-0015
2
Alcohol/Detergent Inlet Valve
MV01-0040
2
Summary of Contents for DSD EDGE
Page 25: ...25 ANNUAL PM INSTRUCTIONS PREVENTATIVE MAINTENANCE KIT Figure 30 Figure 31 Figure 32 ...
Page 28: ...28 ANNUAL PM INSTRUCTIONS PREVENTATIVE MAINTENANCE KIT Figure 35 Figure 36 ...
Page 30: ...30 ANNUAL PM INSTRUCTIONS PREVENTATIVE MAINTENANCE KIT Figure 38 Figure 39 ...
Page 35: ...35 ANNUAL PM INSTRUCTIONS PREVENTATIVE MAINTENANCE KIT Figure 43 ...
Page 45: ...45 ANNUAL PM INSTRUCTIONS PREVENTATIVE MAINTENANCE KIT ...