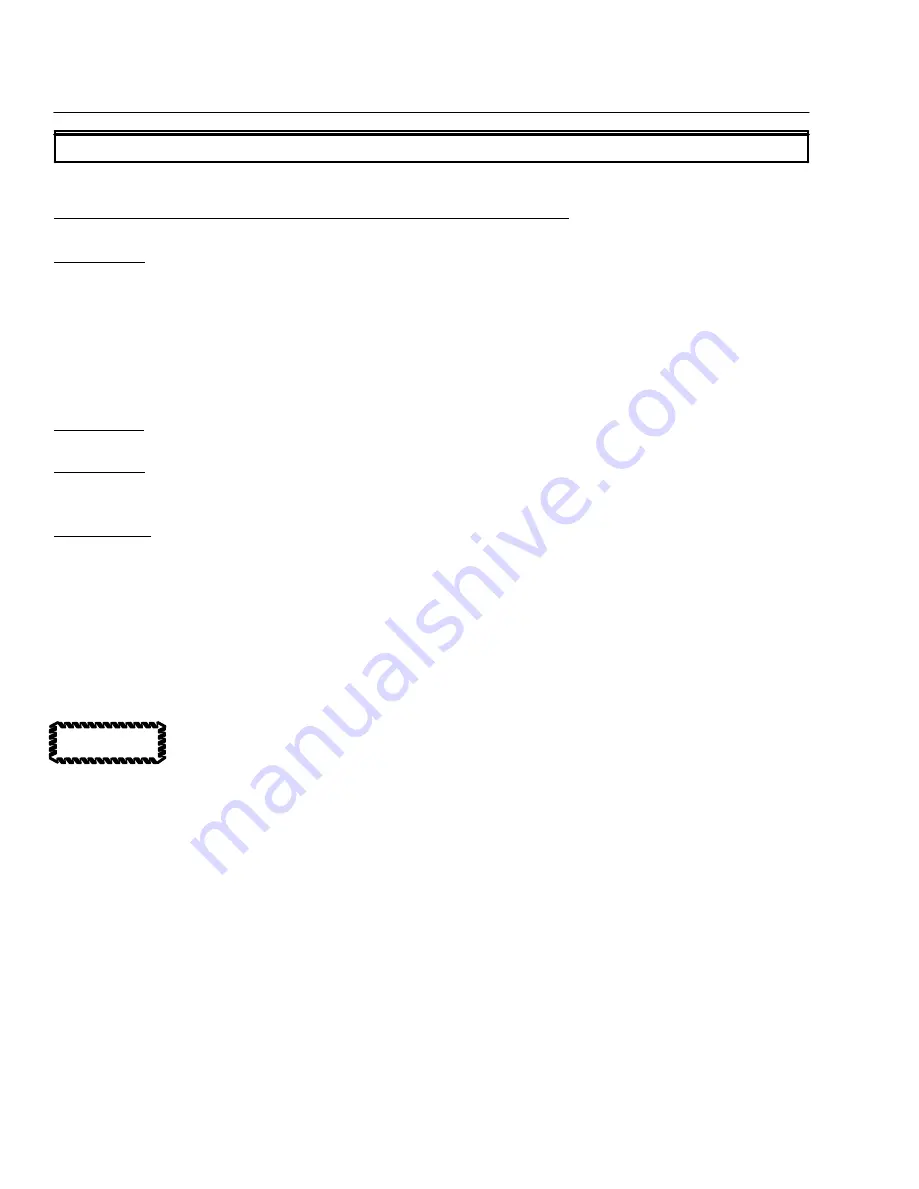
CSP
−
E
−
1
ROTORCRAFT FLIGHT MANUAL
Emergency and
Malfunction Procedures
MD 500E
(Model 369E)
Revision 14
3
−
14
FAA Approved
3
−
8. ENGINE FUEL CONTROL SYSTEM MALFUNCTIONS
FUEL CONTROL OR POWER TURBINE GOVERNOR FAILURE
Indications:
Failure is indicated by an instrument needle fluctuation.
A rise or drop of:
N
1
N
2
/N
R
TOT
Torque
Conditions:
Failure Producing an Overspeed.
Indications:
Engine torque, TOT, N
1
and N
2
/N
R
, suddenly increasing.
Possible right yaw.
Procedures:
Increase collective to load the main rotor, simultaneously rolling the twist-
grip toward the ground idle position until control of N
2
speed is obtained.
Manually control N
2
speed (102−103%) with the pilots twistgrip.
If operating RPM cannot be controlled, close twistgrip to CUTOFF and
make an autorotational landing.
Immediate pilot action is necessary because engine torque, TOT,
N
2
, and rotor rpm may suddenly increase above approved limits.
When shutting down the engine, do not reduce collective pitch until
the rotor rpm has decreased to within the normal operating range.
CAUTION