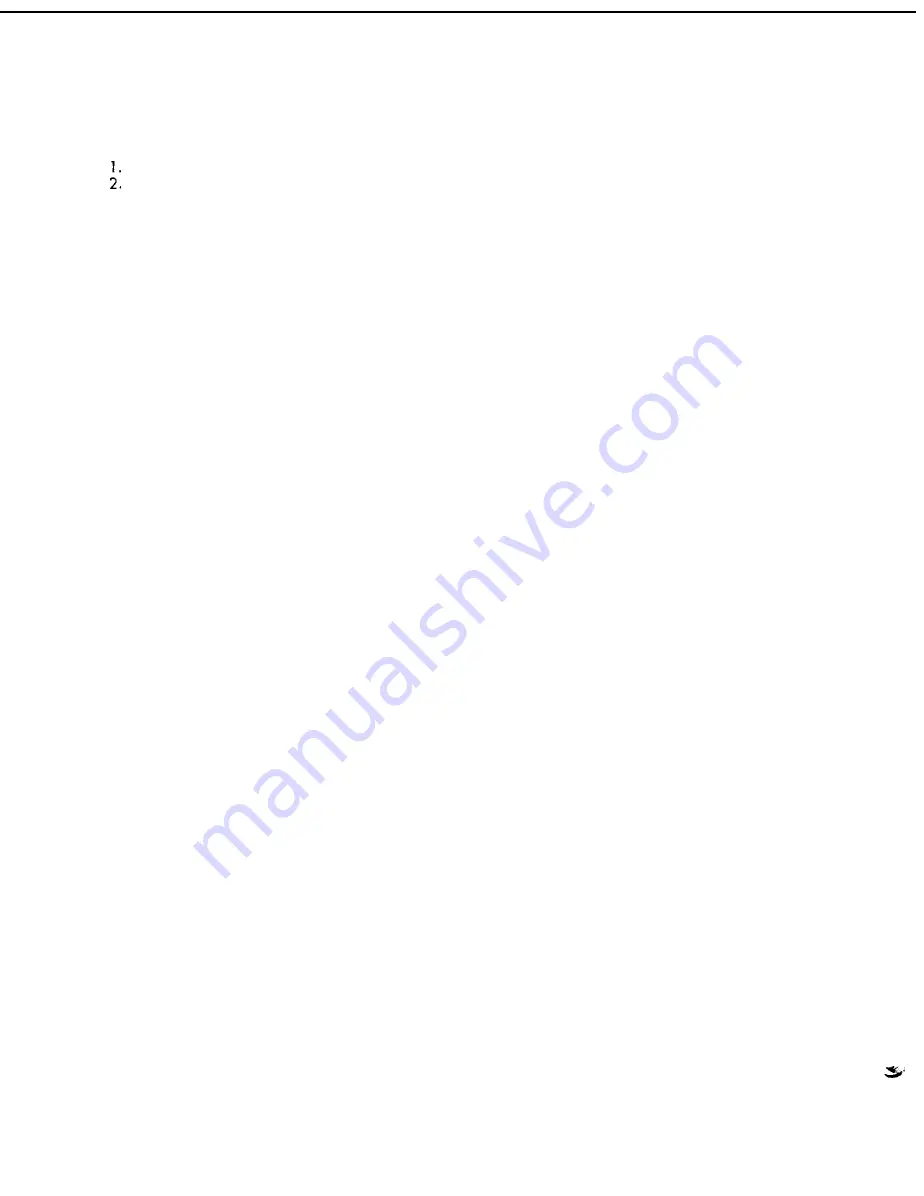
START-UP PROCEDURE
Do not start the SEASONPAK water chiller until the
following steps have been completed.
Check all auxi liary components of the installation.
3.
4.
5.
Open the compressor suction and discharge shut
off valves until back seated. Back seating the
valve closes the gauge ports and, if gauges ore
provided, close valve one turn from full open, to-
ward the closed position. Always replace seal
caps.
Open the manual liquid line shut off valve at the
condenser.
If water regulating valves are provided, connect
their capillary to the manual valves provided on
the condensers and open the manual valves.
Check to see that the water temperature thermo-
stat is installed in the entering water line, that
6
7.
8.
9.
10.
11.
12.
13.
the thermostat well is full of heat conducting
compound and that the bulb is secured with the
retaining fitting.
Check the compressor oil level. Prior to start-up,
the oil level should be in the oil sight-glass.
Fill the water system. The cooler circuits should
be filled with clean non-corrosive water.
Check the main system “on-off” switch to see
that it is in the “off” position. The pump down
switches should be thrown to the “auto” position.
Check resets of all safety controls.
Throw the main power disconnect to “on”.
Start the auxiliary equipment for the installation.
Set the circuit breakers to “on”
Start the system by pushing the system “on-off”
rocker switch to “on”.
OPERATION
During full load operation, check the compressor oil
level. It should be at the center of the oil sight glass
during operation.
Check the refrigerant charge frequently at the mois-
ture/liquid indicator. A steady clear glass of liquid
r e f r i g e r a n t indicates sufficient charge. The sight
glass also indicates the moisture content of the refrig-
erant in the system. The color of the element in the
glass indicates whether the system is wet or dry. Refer
to the color table on face or cap of the indicator. If
the indicator does not show a dry system after several
hours of operation, the filter-drier element must be
c h a r g e d .
CHECKING
All controls are checked a n d adjusted prior to leaving
the factory. However, after the unit has operated sat-
isfactorily for a reasonable length of time, a check of
the operation and safety controls can be made as in-
dicated below.
Oil Pressure Safety Switch - The oil failure pressure
switch is activated by a low pressure differential be-
tween the oil pressure and the crankcase pressure.
Upon start-up, the normally closed pressure actuated
contact of this control opens when the pressure dif-
ferential increases to about 15 psig. If oil pressure
does not reach this differential, the thermal time de-
lay remains energized and opens a bi-metallic safety
contact, de-energizing the complete control circuit.
If pressure reaches the prescribed differential within
120 seconds, the thermal time delay is de-energized
and the control circuit remains closed. If, during the
operation, the oil pressure differential falls below 10
psig, the thermal time delay is again energized ond
and the control will shut down the compressor.
To check the control, jumper the Freezestat ter-
minals L & M and trip the circuit breaker to the “off”
position. Throw control circuit to “on” to pull-in
contactor. The contactor should drop out ond the safe-
ty indicator light should go out after approximately
120 seconds or less. After checking the control, wait
approximately 2 to 3 minutes and then reset control
manually. The compressor con then be started. Re-
peated successive operations of the control will re-
quire a longer period before it can be reset, since the
bi-metal will get hotter and will take more time to
cool.
Check the temperature control thermostat by observ-
ing operation at reduced loads. The thermostat is fac-
tory set for 44F leaving chilled water temperature
w h e n t h e e n t e r i n g t e m p e r a t u r e i s 5 4 F . R e f e r t o
CHECKING CONTROLS section, below.
Check voltage and amperage of the compressor
motor.
Adjust water regulating valve for discharge pres-
sures between 200 and230 psig for the most economic-
al operating pressure.
Close gauge ports on valves when gauge readings
are not required. This will prolong the gauge life.
CONTROLS
High Pressure Control - The high pressure switch
will shut down the compressor and close the liquid
line solenoid valve when the compressor discharge
pressure reaches 270 psig for water cooled units, or
380 psig for air cooled units. To check the control,
slowly throttle the condenser inlet water or shut down
the condenser fan. Observe the cut-out point. During
testing, stand by the System “On-Off” switch to shut
down the unit should the safety device malfunction.
Be sure the gauges used ore accurate.
The water cooled condensers are supplied with a
300 psig relief valve and the discharge pressure dur-
ing the test must be kept below 270 psig. For air
cooled
condenser operation, the relief valve will be
set for 425 psig.
The control can be manually reset at approximately
70 psig below the cut out point.
Low Pressure Control - This pressure switch is con-
nected
to the low side of the system and its purpose
is to shut down the compressorot the end of the pump-
down cycle. It will open at 35 psig and automatically
reset at approximotely 60 psig. The control can be
checked by throwing the individual pumpdown switches
to the manual position ond observing the cut-out point
on the gauge.
Freezestat - The Freezestat is a pressure type con-
trol connected to the low side of the system and is set
to shut down the system when the pressure drops low
enough to be dangerous
OS
far as cooler freeze-up is
concerned. The control is factory set at 52 to 53 psig.
When dropping to this point, the normally open pres-
sure actuated contacts of this control will close ener-
Page 24