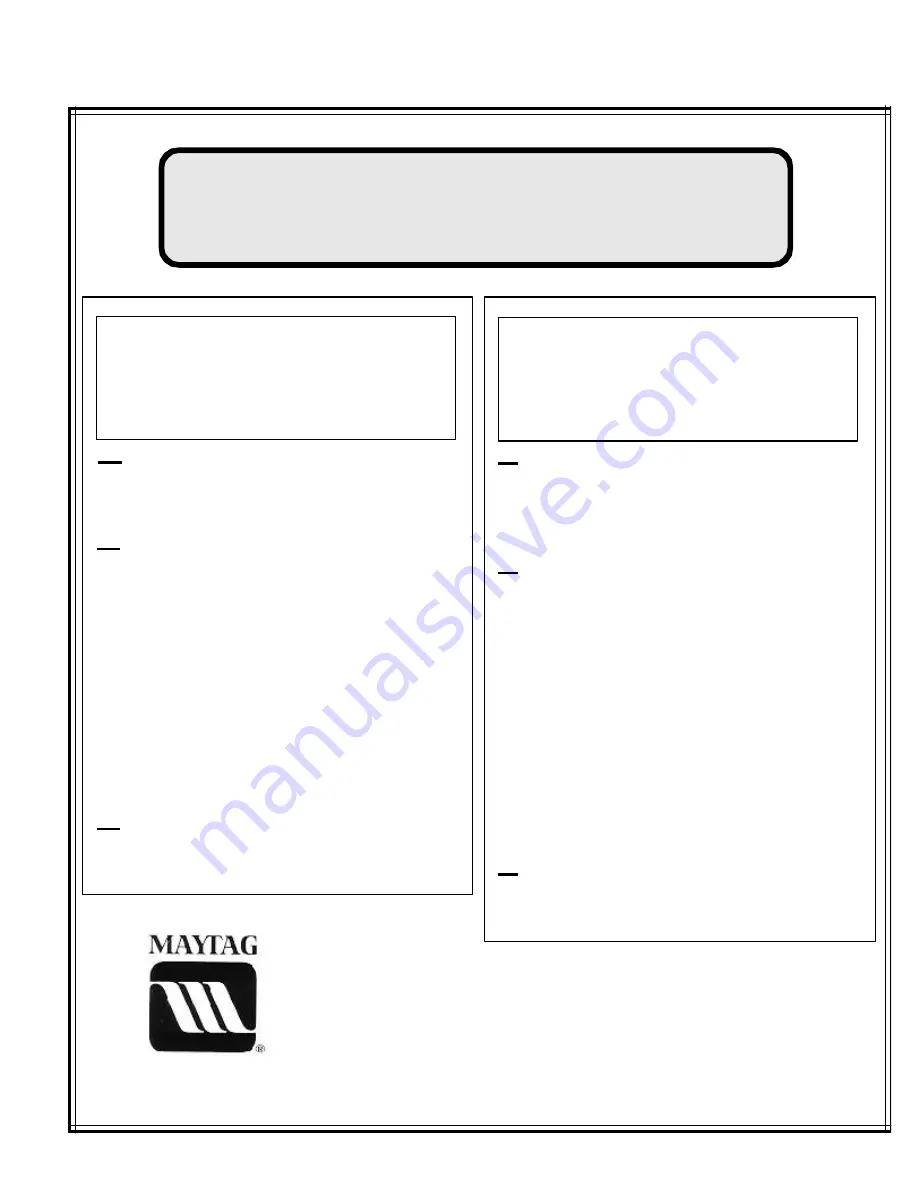
MDG-50
Installation Manual
For replacement parts, contact the distributor from which the dryer
was purchased or contact:
Maytag Co.
403 West Fourth St North
Newton, Iowa 50208
(515) 787-7000
WARNING: For your safety the
information in this manual must be
followed to minimize the risk of fire or
explosion or to prevent property damage,
personal injury or death.
Do not store or use gasoline or other flammable
vapor and liquids in the vicinity of this or any
other appliance.
WHAT DO YOU DO IF YOU SMELL GAS
* Do not try to light any appliance.
* Do not touch any electrical switch; do not use
any phone in your building.
* Clear the room, building or area of all
occupants.
* Immediately call your gas supplier from a
neighbor's phone. Follow the gas supplier's
instructions.
* If you cannot reach your gas supplier, call the
fire department.
Installation and service must be performed by a
qualified installer, service agency or the gas
supplier.
AVERTISSEMENT: Assurez-vous de bien
suivre les instructions données dans cette
notice pour réduire au minimum le risque
d’incendie ou d’explosion ou pour éviter tout
dommage matériel, toute blessure ou la mort.
Ne pas entreposer ni utiliser d’essence ni
d’autres vapeurs ou liquides inflammables dans
le voisinage de cet appareil ou de tout autre
appareil.
QUE FAIRE SI VOUS SENTEZ UNE ODEUR
DE GAZ:
* Ne pas tenter d’allumer d’appareil.
* Ne touchez à aucun interrupteur. Ne pas
vous servir des téléphones se trouvant dans
le bâtiment où vous vous trouvez.
* Évacuez la pièce, le bâtiment ou la zone.
* Appelez immédiatement votre fournisseur de
gaz depuis un voisin. Suivez les instructions
du fournisseur.
* Si vous ne pouvez rejoindre le fournisseur
de gaz, appelez le service des incendies.
L’installation et l’entretien doivent être assurés
par un installateur ou un service d’entretien
qualifié ou par le fournisseur de gaz.
122298SL/cj
Part No. 113067