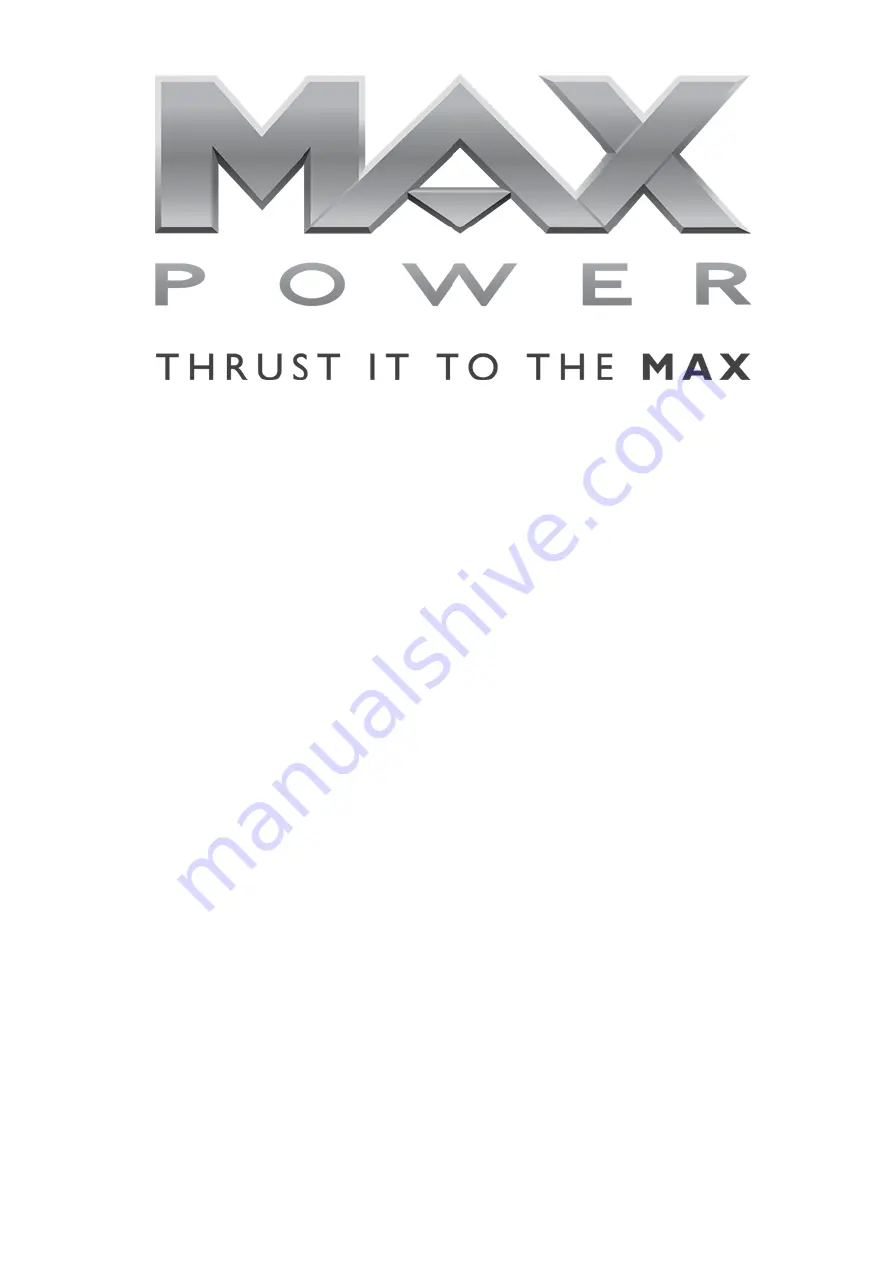
www.max-power.com
CT100 12V
CT125 24V
With electronic thruster control
INSTALLATION OPERATION MAINTENANCE
FROM SERIAL NO. 83338 TO CURRENT
Serial No.: ------------------------------------------------------
Installation date: -------------------------------------------------
THIS MANUAL MUST BE KEPT ONBOARD AT ALL TIMES
Manual CT100 12V & CT 125 24V
Last Update: December 2013
Via Philips 5, 20900 Monza (MI), Italy
Tel. +39 039 200 1973-936 - Fax +39 039 2004299
www.max-power.com E-mail:[email protected]