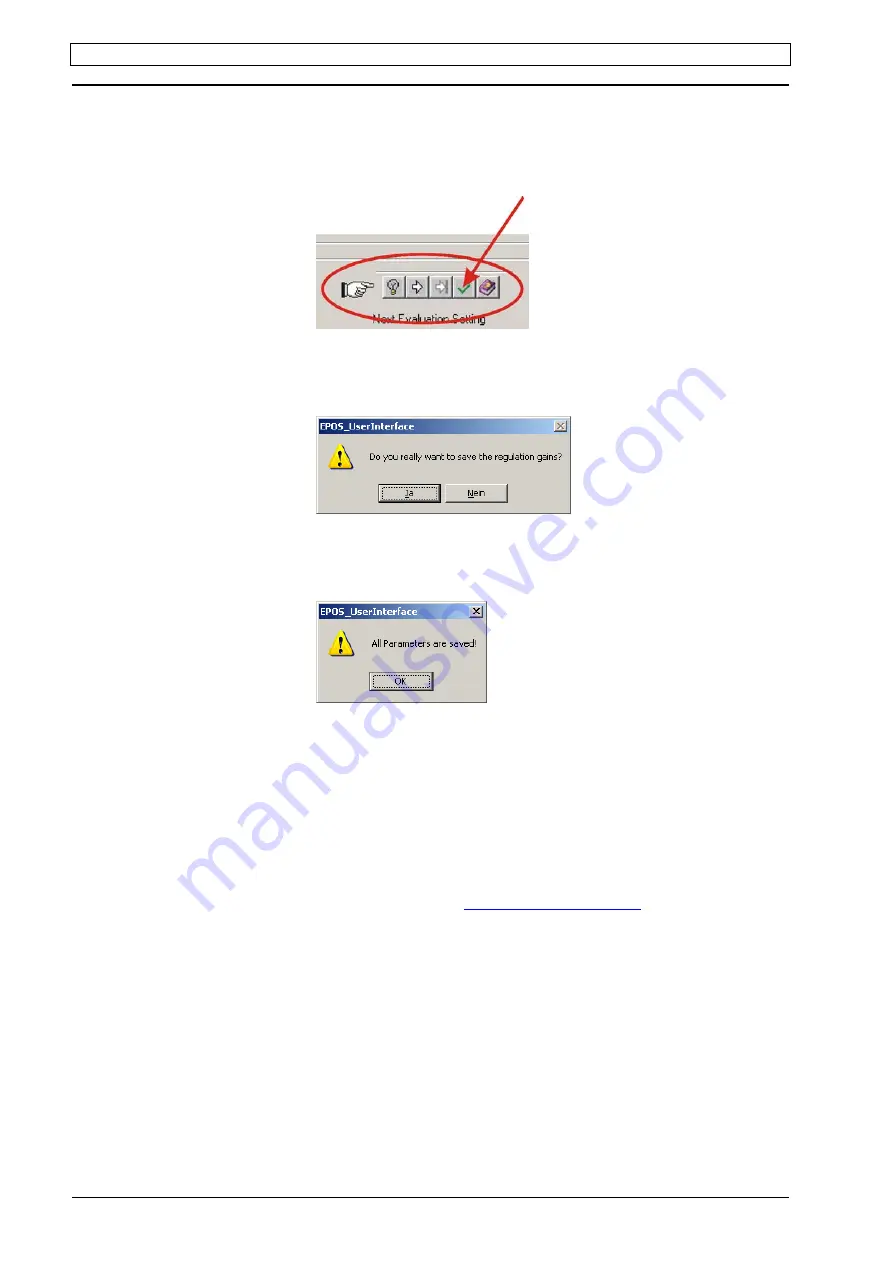
maxon motor
EPOS Positioning Controller
EPOS 24/1 Getting Started
6.4.6
Save all Regulation Gains
All the regulation gains found by the auto-tuning are stored locally (on your
PC) up to now. To take effect permanently you have to store the values on
the EPOS.
a)
Figure 47: Save button
Click on ‘Save button’ to save regulation gains.
b)
Figure 48: Confirm regulation gains saving
Confirm the saving of regulation gains by clicking on ‘Ja’ button.
c)
Figure 49: Confirm saving of all parameters
Confirm saving of all parameters by clicking on ‘OK’ button.
7
Conclusion
Now the EPOS 24/1 is ready for operation in one of the supported
regulation modes!
For further settings and more detailed information’s, use online help by
pressing F1 or refer to the
.
30
maxon motor control
Edition July 2007/ Subject to change