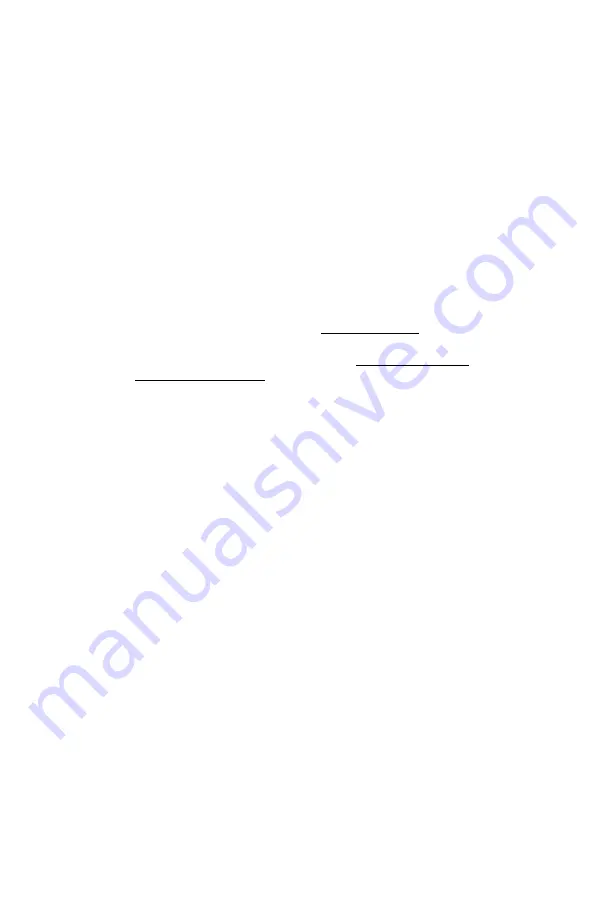
7
IX. CLEANING PROCEDURE
(Please notify the factory if cleaning for oxygen service is required)
A.
TUBE AND FLOAT CLEANING
1.
Remove the float stops. Take care to avoid chipping the inside edges of
the tube.
2.
Flush the inside of the tube with solvent (without wax or inhibitors, i.e.
glycols). Isopropyl alcohol 90% is recommended. All parts should be
ultrasonically cleaned if possible.
3.
Clean the inside of the tube with a pipe cleaner, flush with solvent (see
step A. 2.), and then blow dry.
4.
Clean the float with a lint free cloth. Floats should always be handled
using clean tweezers with soft holding surfaces.
5.
Clean and replace the inlet float stop. Be sure that it is firm in the tube.
6.
Replace the float with tweezers.
7.
Replace the outlet float stop.
8.
Invert the tube as described under INSTALLATION #3.
9.
If the float sticks in the tube then repeat the cleaning procedure.
10.
Reassemble the Tube Cube in reverse to DISASSEMBLY &
REASSEMBLY step C. Note: position the scale behind the lens of the
Tube Cube.
B.
METAL PARTS CLEANING
Ultrasonic immersion cleaning with Solvon PB is preferred; however, any
industrial solvent which does not attack the metal or influence the process
performance is acceptable.
C.
O-RINGS AND SEALS CLEANING
1.
Wash thoroughly with detergent and rinse with water.
2.
Lubricate and reapply to metal parts. Halocarbon grease is
recommended.
X. VALVE REMOVAL AND INSTALLTION
1.
Turn the valve handle clockwise so that the valve stem engages the orifice
(about 3 turns from full open).
2.
Remove the valve cartridge from the flowmeter by using a 9/16” open
end
wrench. The valve cartridge will screw completely out of the flowmeter body.
3.
Take the replacement valve cartridge and screw it into the valve cartridge
cavity and then tighten with the 9/16” wrench.
Note: Be certain that the orifice and the orifice o-ring have been removed prior to
replacing the valve cartridge with another size.