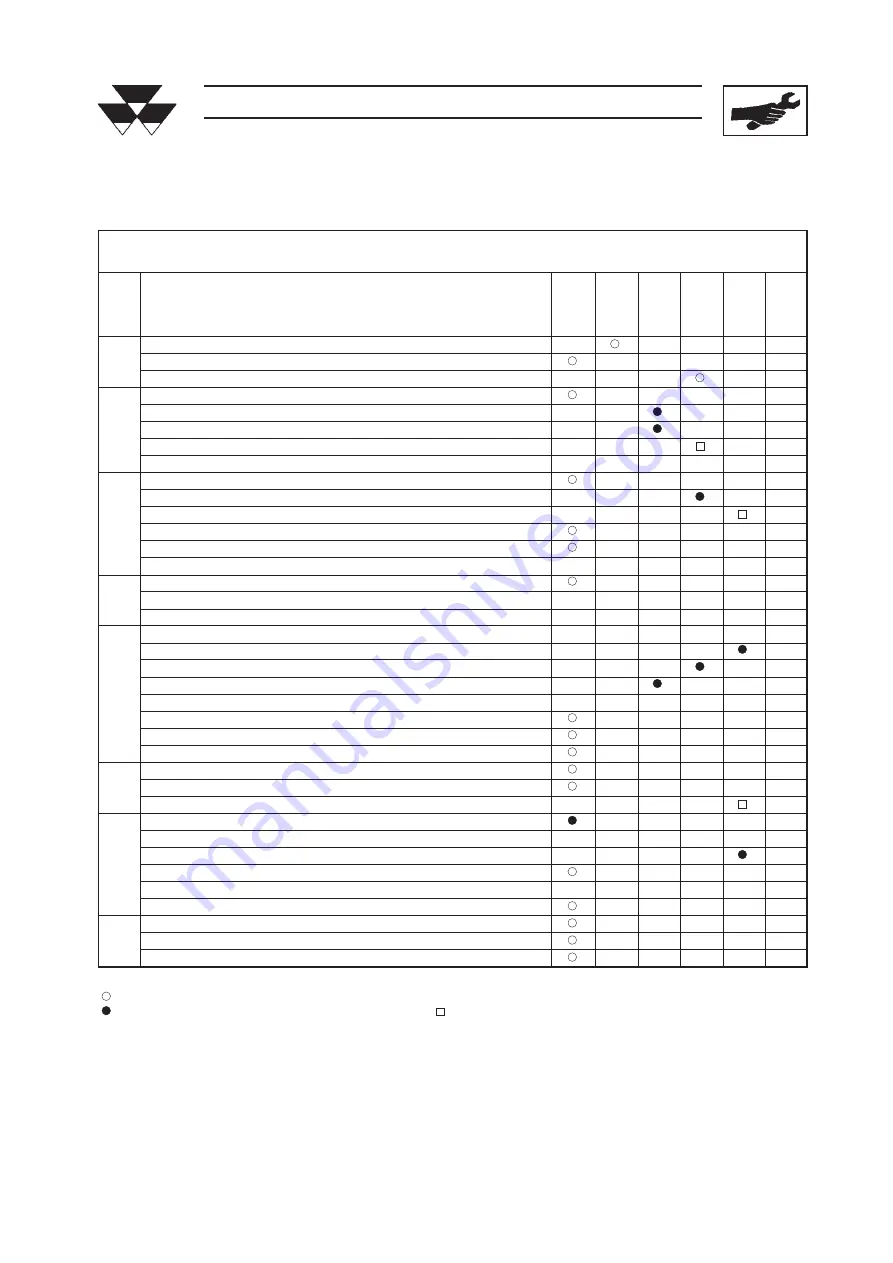
1 - 29
INTRODUCTION
Pre-delivery inspection and maintenance
4-3 Routine maintenance guide
Servicing
points
(Fig.11-1)
1000
hours
500
hours
250
hours
100
hours
Daily or
as
required
ENGINE
FUEL SYSTEM
TRANSMISSION - BRAKES
HYDRAULIC SYSTEM
AND STEERING CIRCUIT
(1) Operation to be carried out at least once a year.
(2) Initially after the first 500 hours service and then every 1000 hours.
(3) ATTENTION: Change the filter on the delivery side of the steering circuit after the first 50 hours service to safeguard the circuit itself.
Following this, replace the filtre on the delivery every 250 hours. Clean (or replace) the filtre on the intake side of the hydraulic pumps
after the first 250 hours service. After this, clean the filter after every 250 hours service and change it every 500 hours.
ATTENTION: use your own discretion and experience when deciding the actual intervals for variable interval service and maintenance
operations. Always remember however, that it is better to perform them too often than not often enough.
REFERENCE MARKS FOR THE OPERATIONS
Inspection, filling, lubrication or adjustment.
q Cleaning or washing
Replacement.
Operations that must be carried out by the Dealer
Perform general lubrication
A B C D
Lubricate three-point hitch
E
Front wheel hub for axle with 2 driving wheels
-
Check engine oil level
3
Change engine oil
12
Change engine oil filter
14
Check valve clearance
-
Clean fuel filter bowls
18
Change fuel filter cartridges
18
Check injector settings
-
Dry air filter: clean drain valve
15
Dry air filter: clean or change cartridge
15
Drain sludge from fuel tank
q
-
Check coolant level in radiator
2
Clean radiator fins
q
2
Wash out cooling circuit
q
-
Check oil levels in gearbox (steering and hydraulic systems), front axle differential and front final drives
q
4 - 5 - 6
Change oil in gearbox
(2)
(steering and hydraulic system), front axle differential and rear final drives
8-9-10-11
Clean oil filter on the intake
(3)
q
16
Change oil filter on the delivery side
(3)
of the steering circuit
17
Clean the transmission and hydraulic system oil cooler
q
-
Check and adjust free travel of brake pedals
-
Check and adjust free travel of clutch pedal and PTO clutch
-
Check oil level in brake circuit
6
Check level of electrolyte in battery
20
Check fan belt tension
21
Check efficiency of alternator and starter motor
-
Check level of screen wash liquid
-
Check and clean cab air filter
q
19
Change cab air filter element
19
Check charge of air conditioning system
-
Clean condenser of air conditioning system
q
-
Check tension of compressor belt
-
Check tyre pressure
-
Check wheel nut tightness
-
Check tightness of nuts and bolts in general
-
CAB AND AIR
CONDITIONING
ELECTRIC
SYSTEM
OTHERS
LUBRICA-
TION
COOLING
SYSTEM
EVERY
PERFORM THE FOLLOWING OPERATIONS
AS
indicated
DESCRIPTION