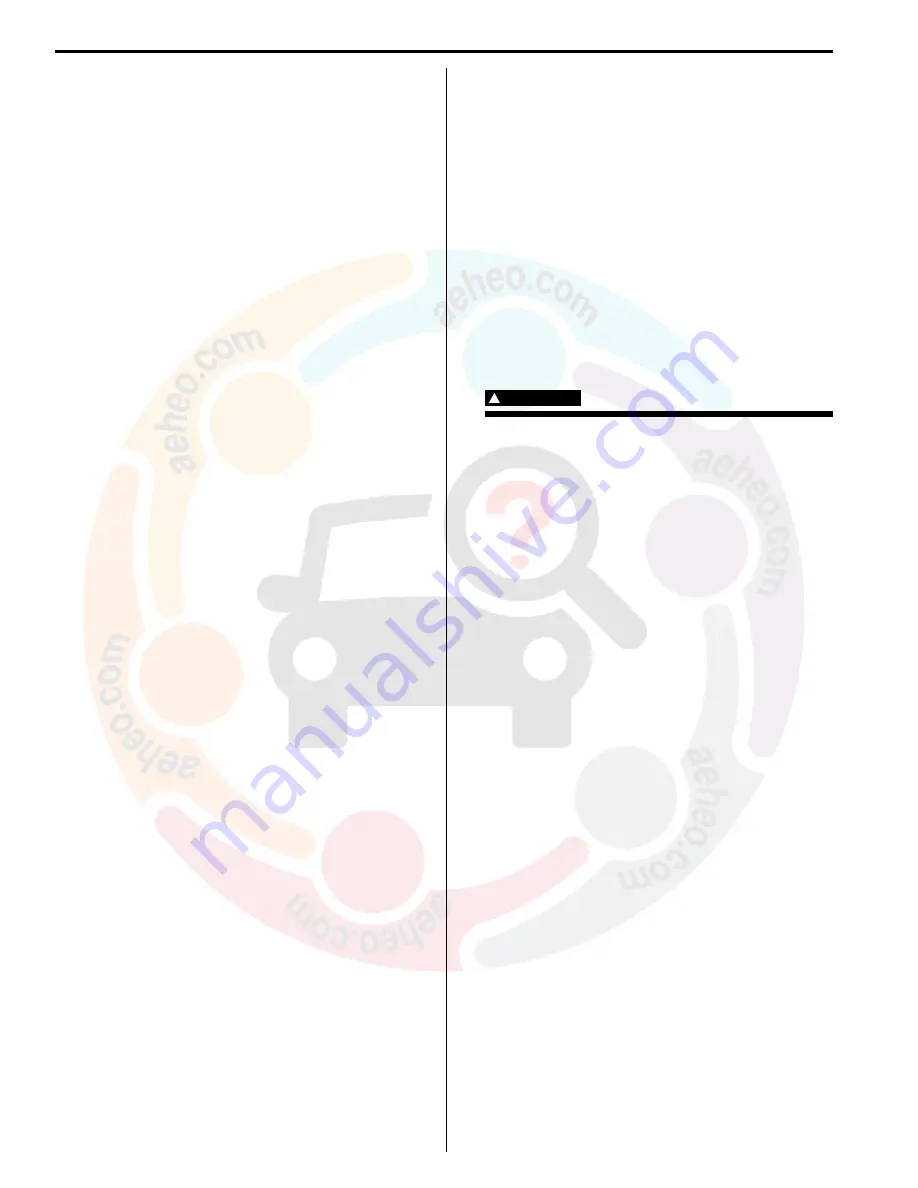
00-3 Precautions:
• Never expose air bag system component parts
directly to hot air (drying or baking the vehicle after
painting) or flames.
• WARNING / CAUTION labels are attached on each
part of air bag system components. Be sure to follow
the instructions.
• After vehicle is completely repaired, perform “Air Bag
Diagnostic System Check”: in Section 8B.
Precautions for LPG Vehicles
AENAR90A0000002
LPG Feature
• LPG is a clean, high octane and eco-friendly fuel. It is
basically a mixture of Butane and Propane and is
obtained from Natural Gas Fractionation and Crude
Oil Refining.
• LPG is a gas at atmospheric pressure, but can be
liquidated when moderate pressure is applied or when
the temperature is sufficiently reduced.
• When LPG leaks, LPG settles down since LPG is
heavier than air.
Condition of Workshop
• There should be no leaks in the fuel system, referring
to “Fuel Leakage Check Procedure”: LPG in Section
1G.
• There should be enough ventilation system.
• Vehicles should not be parked within 3 m of any
sources of ignition.
• LPG fueled vehicles being repaired in workshops,
unless the fuel is required for engine operation,
should have the manual shut off valve closed and the
LPG in the service line exhausted by running the
engine or depressurizing the line in a well ventilated
area.
• Vehicles undergoing repairs involving welding or the
application of heat, to any part within 1 m of the LPG
cylinder, should have the LPG cylinder removed or
shielded from the source of heat.
Servicing and Handling
• Make sure to stop engine when inspecting engine
system.
• Repair operation involving heat should be carried out
with due regard to fire safety.
• Damaged LPG pipes or hoses should not be repaired;
in all cases they should be replaced.
• Welding, brazing and the application of heat should
not be carried out on any part of the LPG cylinder
subsequent to manufacture.
• Make sure to relieve LPG pressure before removing
LPG pipes or hoses. Check for fuel leakage after
installing them.
• The LPG cylinder, piping and all components of the
system should be examined for corrosion,
deterioration and for any modification affecting
compliance, at least once in a year or incase of
malfunction or accident.
• A vehicle, which is about to be scrapped, should have
its LPG cylinder removed prior to disposal.
• The LPG cylinder, which passed more than 15 years
from its production, should not be used.
General Precautions
AENAR90A0000003
The WARNING and CAUTION describe some general
precautions that you should observe when servicing a
vehicle. These general precautions apply to many of the
service procedures, and they will not necessarily be
repeated with each procedure to which they apply.
WARNING
!
• Whenever raising a vehicle for service, be
sure to follow the instructions under
“Vehicle Lifting Points”: in Section 0A.
• When it is necessary to do service work
with the engine running, make sure that
the parking brake is set fully and the
transaxle is in Neutral, Keep hands, hair,
clothing, tools, etc. away from the fan and
belts when the engine is running.
• When it is necessary to run the engine
indoors, make sure that the exhaust gas is
forced outdoors.
• Do not perform service work in areas
where combustible materials can come in
contact with a hot exhaust system. When
working with toxic or flammable materials
(such as gasoline and refrigerant), make
sure that the area you work in is well-
ventilated.
• To avoid getting burned, keep away from
hot metal parts such as the radiator,
exhaust manifold, tail pipe, muffler, etc.
Summary of Contents for Wagon R
Page 2: ......
Page 32: ...0B 5 Maintenance and Lubrication ...
Page 184: ...1J 3 Charging System ...