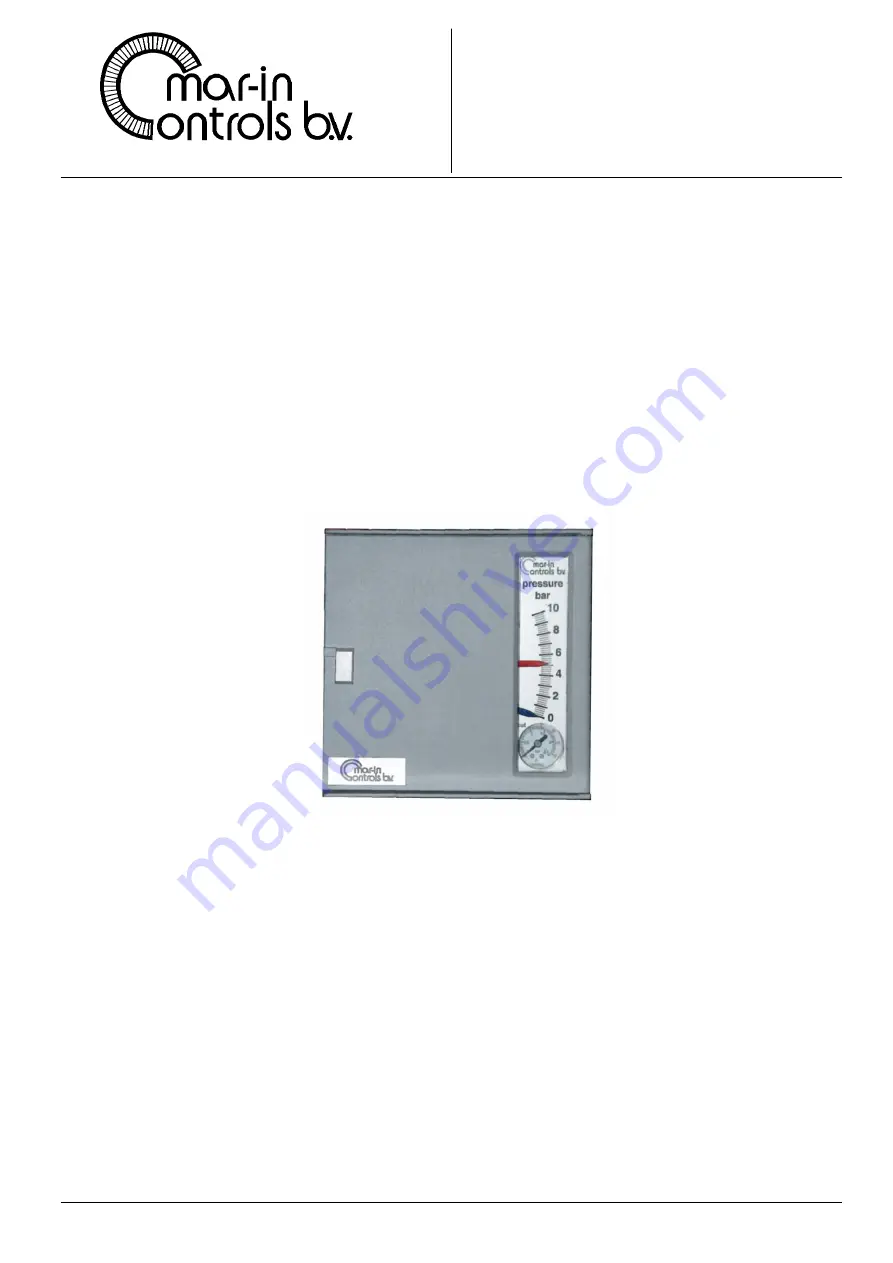
PNEUMATIC CONTROLLER
SERIES
SG6100
Page: 1
MAR-IN CONTROLS B.V. VAN UTRECHTWEG 8 –10 KRIMPEN A/D IJSSEL THE NETHERLANDS
Tel. + 31 (0)180 - 51 71 51 Fax +31 (0)180 - 51 89 14 [email protected] www.mar-in-controls.com
TECHNICAL
MANUAL
CONTROLLER
Pneumatic controller SG 6100