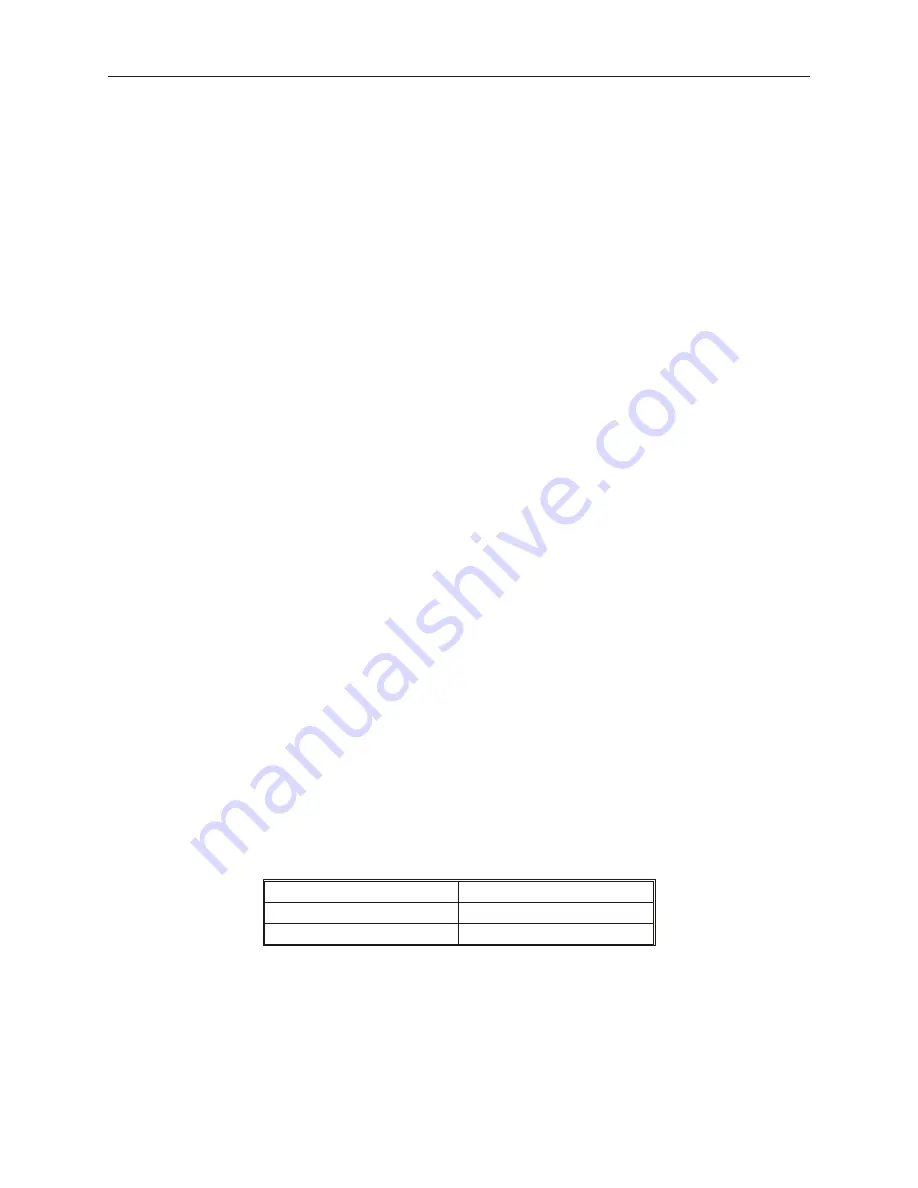
6.
Enter in the
IP Address for the PLC
in the Server IP Address: boxes. Note: Whatever the
network addresses are, the numbers (octets) in the first three boxes must match for the Local
IP and the Server IP.
7.
Enter
255.255.255.0
for the Subnetwork Mask.
8.
If there is a router that will be between the OIT and the PLC, enter the
router IP address
in
the Default Route IP address section.
4
To configure the Slave OIT if there is an Ethernet connected Slave OIT Unit:
1.
Click
Edit-System parameters
and select the
PLC
tab.
2.
Select PLC Type as
Modbus RTU TCP/IP.
3.
Select PLC I/F port as
Ethernet.
4.
For the Multiple OIT box, select
Enable.
5.
Select
Slave
from the Multiple OIT box.
6.
Select
Ethernet
for the Connect I/F.
7.
Select a
unique station number
in the OIT station no. box for each slave OIT, and click
OK
.
Shar ing Data Be tween the Mas ter OIT, Slave OIT and PLC
Mas ter OIT to a PLC
The master OIT will be programmed just as if it were the only OIT connected to the PLC.
Slave OIT to a Mas ter OIT
Any local word registers (LW) or local bits (LB) located in the master OIT can be accessed (read) and written to
(write) by the slave OITs. Do this by using the "Ms_LW" and "Ms_LB" memory registers. For example, if the
master OIT is storing data in LW10, the slave OIT can access that data by using a device type:
Ms_LW
and device
address:
10
. Multiple OIT is set to
Master
. Connect I/F is set to
Ethernet
.
Slave OIT to the PLC
The slave OITs may access data in the PLC in two ways:
1.
It may write to the local words/bits in the master OIT (via Ms_LW and Ms_LB registers), and
those values may be transferred to the PLC by setting up a data transfer object in the master
OIT program. Note: If the master and the slave OITs are accessing the same areas of memory
in the PLC, this method is more efficient because the time required to get information from
the PLC is reduced.
2.
It may read/write directly to the PLC addresses (as though it were the only OIT connected to
the PLC). Note: This method may result in inconsistent Master/Slave communications.
Maple Systems recommends using method #1.
Man ag ing Com mu ni ca tion Fail ures
When communicating with multiple devices over a network, it is possible that one or more of the devices may fail
without affecting other devices on the network. When this happens, plant personnel may need to be notified of the
failure, while still maintaining communications with the rest of the network.
Communications failures to any node can be managed by the OIT. A series of local bits monitor and control
communications failures on both the main and auxiliary communications ports.
Bits
PLC Node
LB9100-9227
Main port nodes 0-127
LB9228-9355
Aux port nodes 0-127
When a communications failure is detected on a particular PLC node address, the corresponding local bit will be
turned off, and communication to that node address is suspended. To restart communications to that node, the bit
must be turned back on.
1010-1001a, Rev 02
Us ing EZware-500
75
Summary of Contents for Silver HMI504T
Page 1: ...1010 1001A Rev 02...
Page 32: ...1010 1001a Rev 02 28 Silver Series Installation Operation Manual...
Page 128: ...1010 1001a Rev 01 124 Silver Series Installation Operation Manual...
Page 156: ...1010 1001a Rev 02 152 Silver Series Installation Operation Manual...
Page 166: ...1010 1001a Rev 02 162 Silver Series Installation Operation Manual...
Page 216: ...1010 1001a Rev 01 212 Silver Series Installation Operation Manual...
Page 251: ...1010 1001a Rev 02 Macros 247 Set Bit Objects Attributes Dialog Project Example of Add 2...
Page 264: ...End Macro_Command 1010 1001a Rev 02 260 Silver Series Installation Operation Manual...
Page 268: ...1010 1001a Rev 01 264 Silver Series Installation Operation Manual...