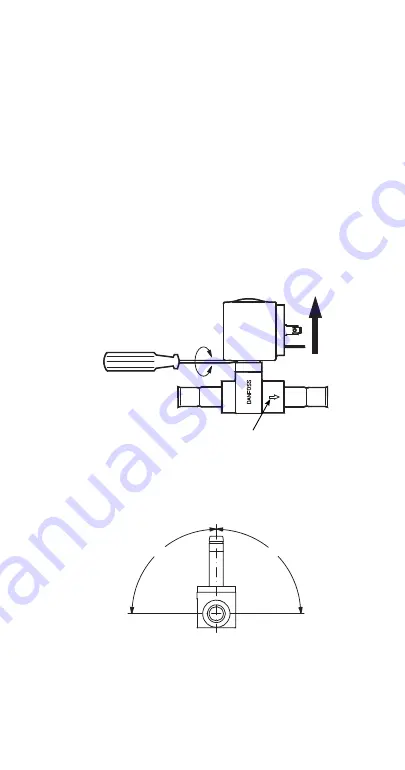
197
Brazing Procedures for Danfoss
Solenoid Valves
•
Danfoss stainless steel solenoid valves require a
slightly different brazing technique than brass-
bodied valves.
Copper clad stainless steel does not require as
much flame contact as copper tubing.
Apply heat to the copper tubing first then the
solenoid socket.
•
15% silver solder is recommended although silver
bearing solder in the 5% to 55% range can be
used.
1. Remove coil and verify direction of flow.
2. Fit valve in place and align stem at the 12:00
position.
3.
Do not disassemble valve.
SV3069
DIRECTION OF
FLOW ARROW
SV3070
90°
90°
Summary of Contents for Q130 series
Page 2: ......
Page 16: ...16 Part Number 8001119 10 19 SM50 MODEL SERIAL NUMBER PLATE ...
Page 36: ...36 Part Number 8001119 10 19 This Page Intentionally Left Blank ...
Page 98: ...98 Part Number 8001119 10 19 This Page Intentionally Left Blank ...
Page 202: ...202 Part Number 8001119 10 19 This Page Intentionally Left Blank ...
Page 234: ...234 Part Number 8001119 10 19 This Page Intentionally Left Blank ...
Page 235: ......