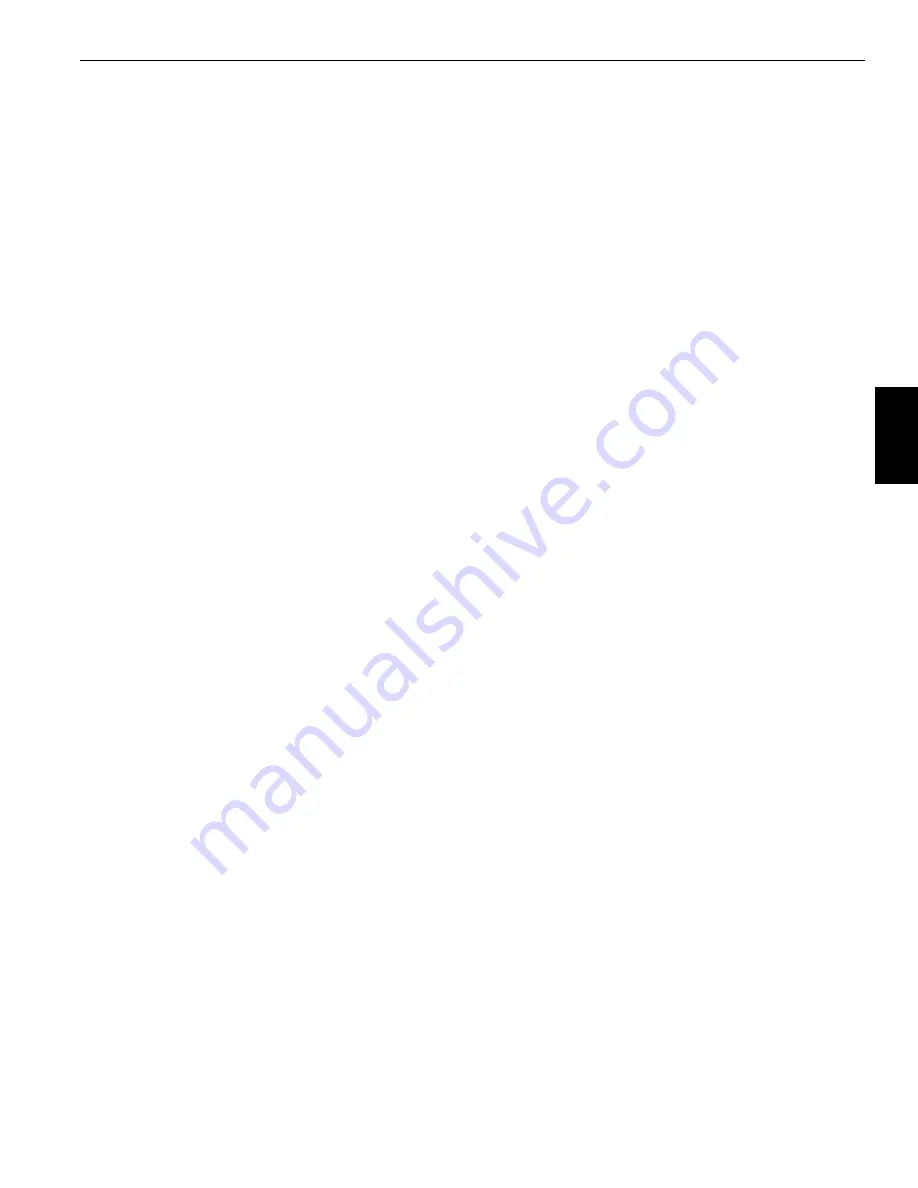
4
10
National Crane
Published 8-01-2017 Control # 287-11
4-27
NBT40 SERVICE MANUAL BOOM
MAINTENANCE
17.
Assemble and install the 5/4/3 retract-2/3/4 extend pin
assembly into anchor plate at the bottom base of the 4th
stage boom (4).
a.
Assemble 3 extend cables (29) on the 5/4/3 retract-
2/3/4 extend pin (78).
b.
Install one washer (132) and one retainer (131) on
each side of the outer cables.
c.
Install one retainer (131) and one washer (132)
inside of each sheave.
d.
Install bushing into single groove sheave and brush
with chassis grease and install on both ends of pin.
e.
Loop 5/4/3 retract cables (77) around single
grooved sheaves and pin assembly.
f.
Install plug (64) in end of pin.
g.
Install shaft assembly into retainer at base of 4th
stage boom and install button end of 5/4/3 retract
cables (77) into anchor plate at the bottom base of
the 5th stage boom.
h.
Install cable retaining capscrew (106) into threaded
hole in cable retainer block at back bottom of 5th
stage.
i.
Install grease fittings (95) toward base of boom. or
[if equipped LH tube (194), RH tube (195), fitting
(188) and two grease fitting (73].
j.
Apply multipurpose grease (MPG) to grease fittings.
18.
Install retract cable guides (84) with capscrew (85) into
the base of the 4th stage boom.
NOTE:
Use caution when moving cylinder to avoid
damage to cable guides.
19.
Lower extend cylinder and push into 3rd stage boom
keeping cables taunt to approximately one foot behind
cylinder anchors in the 3rd stage boom. Raise base of
extend cylinder to top of 3rd stage boom.
20.
Install wear pad (81) with capscrews (83)at the base of
the fourth stage boom.
NOTE:
Apply multipurpose grease (MPG) to all wear pads
and contact surfaces.
21.
Route the two 4/3/2 retract cables evenly centered
around the 4/3/2 retract cable keeper (82). Route
threaded ends of 4/3/2 retract cables (53) down through
the opening in the base of the 3rd stage boom and pull
threaded ends of 4/3/2 retract cables toward tip of boom
(3). Install 4/3/2 retract cable keeper (82) into anchor
plates at the base of the fourth stage boom.
22.
Assemble and install the 4/3/2 retract-1/2/3 extend pin
assembly into anchor plate at the bottom base of the 3rd
stage boom (3).
a.
Install one retainer (37) and one washer (36) inside
of each sheave.
b.
Install bushing (35) into double groove sheave (34)
and brush with chassis grease and install on both
ends of pin.
c.
Loop 4/3/2 retract cables (53) around double
grooved sheaves (34) and pin (191) assembly.
d.
Install plug (64) in end of pin (191).
e.
Install shaft assembly into retainer at base of 3rd
stage boom (3).
f.
Install grease fittings (95) toward base of boom or [if
equipped LH tube (192), RH tube (193), fitting (188)
and grease fitting (73].
23.
Apply multipurpose grease (MPG) to grease fittings.
24.
Install retract cable guides (65) with capscrew (74) into
the base of the 3rd stage boom.
NOTE:
Use caution when moving cylinder to avoid
damage to cable guides.
25.
Lower the extend cylinder onto wear pad (83).
3rd and 2nd Section Boom
1.
Install two top wear pad mounting plates (152), wear
pads (172), with capscrew (198), washer (196) onto the
base of the 3rd stage boom (3).
NOTE:
Apply multipurpose grease (MPG) to all wear pads
and contact surfaces.
2.
Install adjustment cam plate (200), capscrews (197) and
flatwashers (196).
3.
Rotate cam (200) until gap is eliminated between wear
pad and boom section keeping sections centered for
proper boom alignment.
4.
Install one bottom wear pad (143), and shims (142) with
capscrew (69) onto the base of the 3rd stage boom.
NOTE:
Apply multipurpose grease (MPG) to all wear pads
and contact surfaces.
5.
Install two side wear pads (42) and shims (41) onto the
base of the 3rd stage boom. Shim according to
calibration instructions in this section.
NOTE:
Apply multipurpose grease (MPG) to all wear pads
and contact surfaces.
6.
Stretch out 3/8 diameter, 1/2/3 sync extend cable (10),
then bring threaded ends back together to form a loop
and find the center of cable length.
a.
Slide this center loop from front to back through the
cable anchor slot at base, top of the 3rd stage boom
(3).
Reference Only
Summary of Contents for National Crane NBT40 Series
Page 1: ...Service Manual National Crane NBT40 Series R e f e r e n c e O n l y ...
Page 2: ...R e f e r e n c e O n l y ...
Page 216: ...SCHEMATICS NBT40 SERVICE MANUAL 10 2 THIS PAGE BLANK R e f e r e n c e O n l y ...
Page 218: ...NBT40 SERVICE MANUAL APL 2 THIS PAGE BLANK R e f e r e n c e O n l y ...
Page 219: ...R e f e r e n c e O n l y ...
Page 220: ...R e f e r e n c e O n l y ...