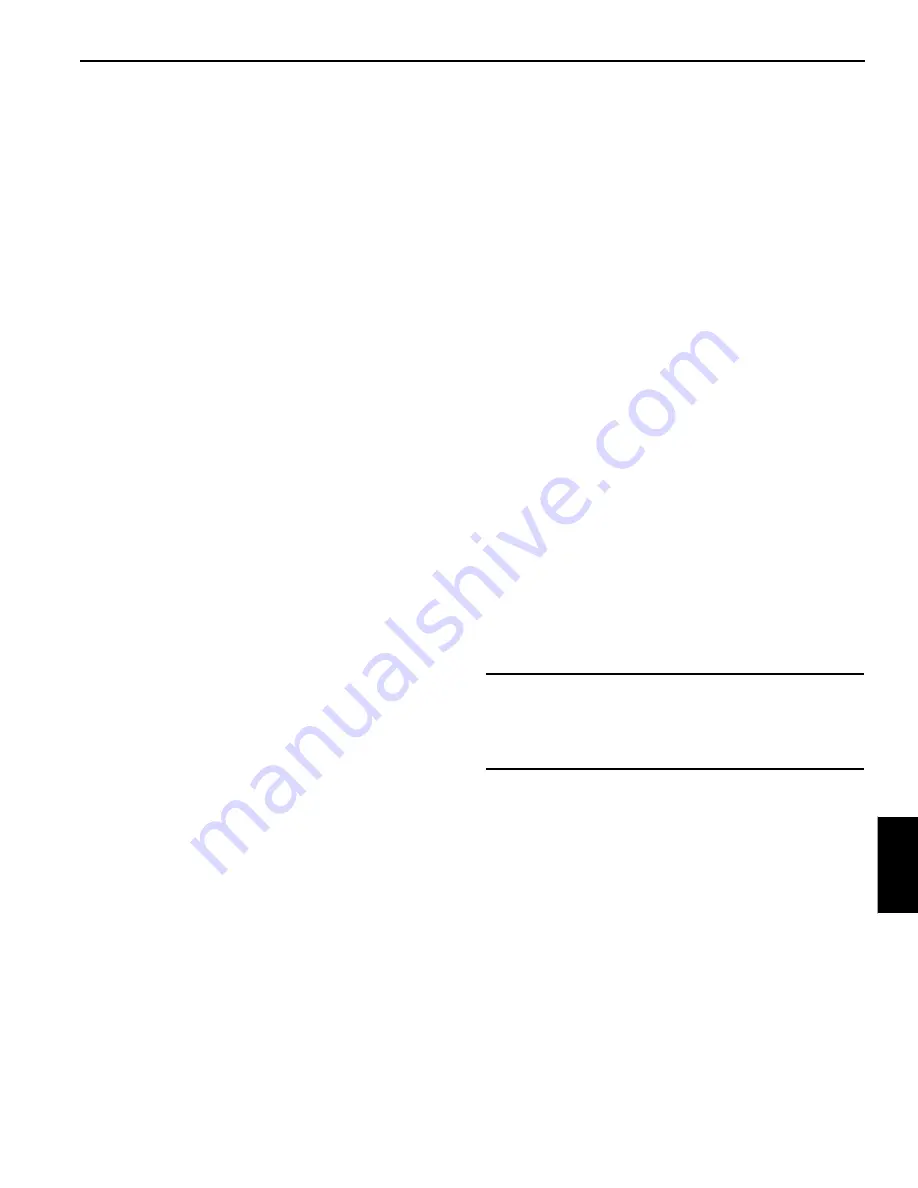
Grove
Published 01-14-2021 Control # 707-01
8-15
TMS9000-2 SERVICE MANUAL
CARRIER
8
Functional Check
A periodic functional check of the power steering system will
generally be adequate to ensure satisfactory service.
1.
Check all fittings for leakage. Accumulation of moist,
black dirt is a good indication of leakage.
2.
Turn the steering wheel through the full range with the
engine running at both idle and full throttle. Do this with
the machine stationary and moving. Note any speed
irregularities and sticky sensation. This may indicate dirt
in the fluid. If the steering wheel continues to rotate
when started and released, a condition known as
motoring exists. This may also indicate dirt in the fluid.
3.
Ensure the system has adequate power. If there is an
indication of hard steering, this can be caused by either
a reduced oil flow to the control valve or a reduced
system relief pressure. Adequate oil pressure can only
be determined by connecting a pressure gauge at the
pump outlet port or at the steering gear inlet port. With
the engine running at a medium speed, turn the steering
wheel to one end of travel and hold at the travel limit just
long enough to get a pressure reading. Never hold the
system relief pressure for more than a few seconds at a
time. The pressure gauge should indicate 13800 kPa
(2000 psi) at the pump outlet.
STEERING PUMP
Description
The steering pump is mounted on and driven by the engine.
The pump is located on the left side of the engine and
provides the hydraulic flow necessary to power the steering
gearbox. The pump is a gear type pump and provides a
priority flow of approximately 38 lpm (10 gpm) at 13,790 kPa
(2000 psi). For additional information on the pump, refer to
Steering Gearbox
Description
The steering gear box is attached to the frame and is located
on the left side beneath the cab. The gearbox provides full-
time hydraulic steering and only enough manual effort to
overcome the torsion bar and turn the rotate valve is
required. With the engine running, there is a constant oil flow
through the steering gear which provides an instant
response and absorbs road shock. There is mechanical
back-up steering so that the vehicle can be steered to the
side of the road in the event of hydraulic pressure loss.
Maintenance
Removal
1.
Tag and disconnect the hydraulic lines from the steering
gearbox. Cap or plug all openings.
2.
Remove the steering shaft from the steering gearbox
input shaft.
3.
Remove the cotter pin and slotted nut securing the drag
link vertical socket to the pitman arm.
4.
Remove the pitman arm as follows.
a.
Using a punch and hammer, bend the retainer tab(s)
out of the pitman arm retainer nut.
b.
Using an allen head socket, remove the retainer nut,
friction washer, and retainer tab washer.
c.
Using a 3-jaw puller, remove the pitman arm from
the gearbox shaft.
NOTE:
The steering gearbox weighs approximately 79 kg
(176 lb).
5.
Support the weight of the gearbox. Remove the six bolts
and hardened washers which secure the gearbox to the
frame and remove the gearbox.
Installation
1.
Prior to installation, wind the relief plungers located at
both ends of the gearbox until they bottom out. Do not
remove or wind out the plungers to a depth of less than 4
mm (0.16 in). Reference Figure 8-9.
2.
Position the gear box on the mounting and secure with
six bolts and hardened washers. Apply Loctite #243 to
the gear box mounting bolts. Torque bolts to 520 Nm
(384 ft-lb).
3.
Turn the input shaft on the gearbox in one direction until
it bottoms out.
4.
Turn the input shaft in the opposite direction while
counting the number of turns until it bottoms out.
5.
Divide the number of turns by two, then turn the input
shaft back that number of turns to center the steering
gearbox output shaft.
1
With the vehicle stationary and engine at idle, place the torque wrench on the steering wheel retaining nut and steer from lock
to lock. A reading of more than 1.7 Nm (15 pounds-inch) means improper phasing. To correct, rotate the intermediate steering
shaft one spline at a time until the torque reads the same throughout the 360 degree rotation.
CAUTION
Equipment Damage Hazard!
Deviation from the following step could result in seal
damage and/or leakage.
Fo
r
Reference
Only