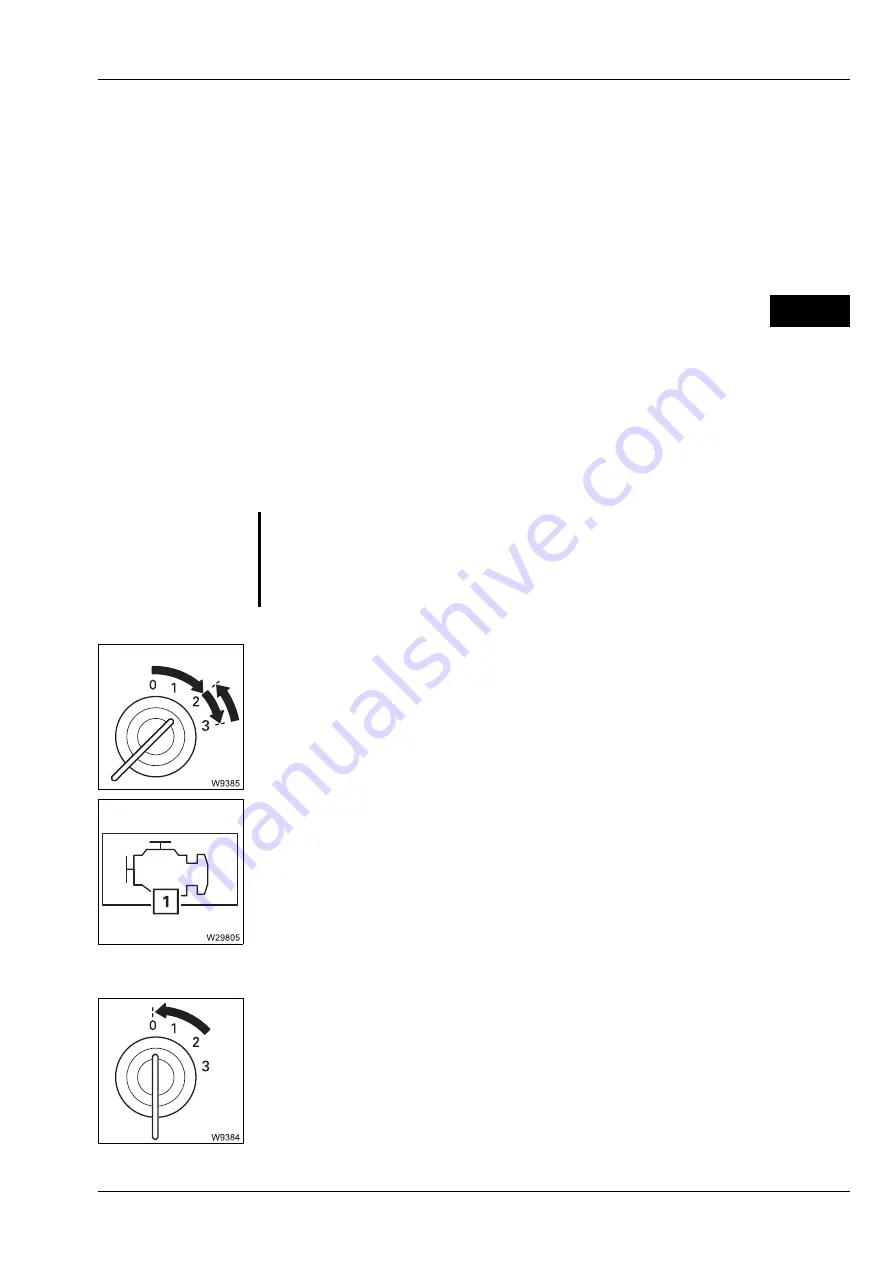
Maintenance work on the carrier
7.3 Engine
0
9
.0
3.
201
8
Maintenance manual
3 302 746 en
7 - 11
GMK5200-1
7.3
Engine
•
In addition, carry out the additional maintenance work as specified in the
Engine manufacturer's documentation
supplied with the vehicle.
•
At the first oil change, fit a drain valve in place of the drain plug;
7.3.1
Checking the oil level
Prerequisites
– The truck crane must be level.
Checking the oil
level
•
Start the engine from the driver's cab;
à
Operating manual
.
•
Start the engine and watch the symbol (
1
).
•
Stop the engine immediately
if the symbol does not disappear after
10 seconds.
If symbol (
1
) is displayed, the oil pressure is too low.
•
Allow the engine to run at idling speed for 2 - 3 minutes.
•
Switch off the engine.
•
Check the oil level after approx. 2 minutes.
s
D
S
Risk of damage to the engine if the oil pressure is too low.
Switch off the engine immediately if the symbol (
1
) is displayed. The engine
can be damaged by running it when the oil pressure is too low.
Summary of Contents for Grove GMK 5200-1
Page 1: ...Maintenance manual 3 302 746 en 09 03 2018 ...
Page 4: ...09 03 2018 3 302 746 en Maintenancemanual GMK5200 1 Blank page ...
Page 6: ...09 03 2018 3 302 746 en Maintenancemanual GMK5200 1 ...
Page 14: ...09 03 2018 3 302 746 en Maintenancemanual GMK5200 1 ...
Page 22: ...09 03 2018 3 302 746 en Maintenancemanual GMK5200 1 ...
Page 27: ...09 03 2018 4 Maintenance manual 3 302 746 en GMK5200 1 4 Run in regulations ...
Page 28: ...09 03 2018 3 302 746 en Maintenancemanual GMK5200 1 ...
Page 32: ...09 03 2018 3 302 746 en Maintenancemanual GMK5200 1 ...
Page 62: ...09 03 2018 3 302 746 en Maintenancemanual GMK5200 1 ...
Page 72: ...09 03 2018 3 302 746 en Maintenancemanual GMK5200 1 ...
Page 313: ...09 03 2018 9 Maintenance manual 3 302 746 en GMK5200 1 9 Longer out of service periods ...
Page 314: ...09 03 2018 3 302 746 en Maintenancemanual GMK5200 1 ...
Page 318: ...09 03 2018 3 302 746 en Maintenancemanual GMK5200 1 ...
Page 322: ...09 03 2018 3 302 746 en Maintenancemanual GMK5200 1 ...
Page 333: ...09 03 2018 Maintenance manual 3 302 746 en GMK5200 1 Appendix ...
Page 334: ...09 03 2018 3 302 746 en Maintenancemanual GMK5200 1 ...
Page 335: ...Appendix ...
Page 336: ......
Page 338: ......
Page 340: ......
Page 342: ......
Page 344: ......
Page 345: ......
Page 346: ......