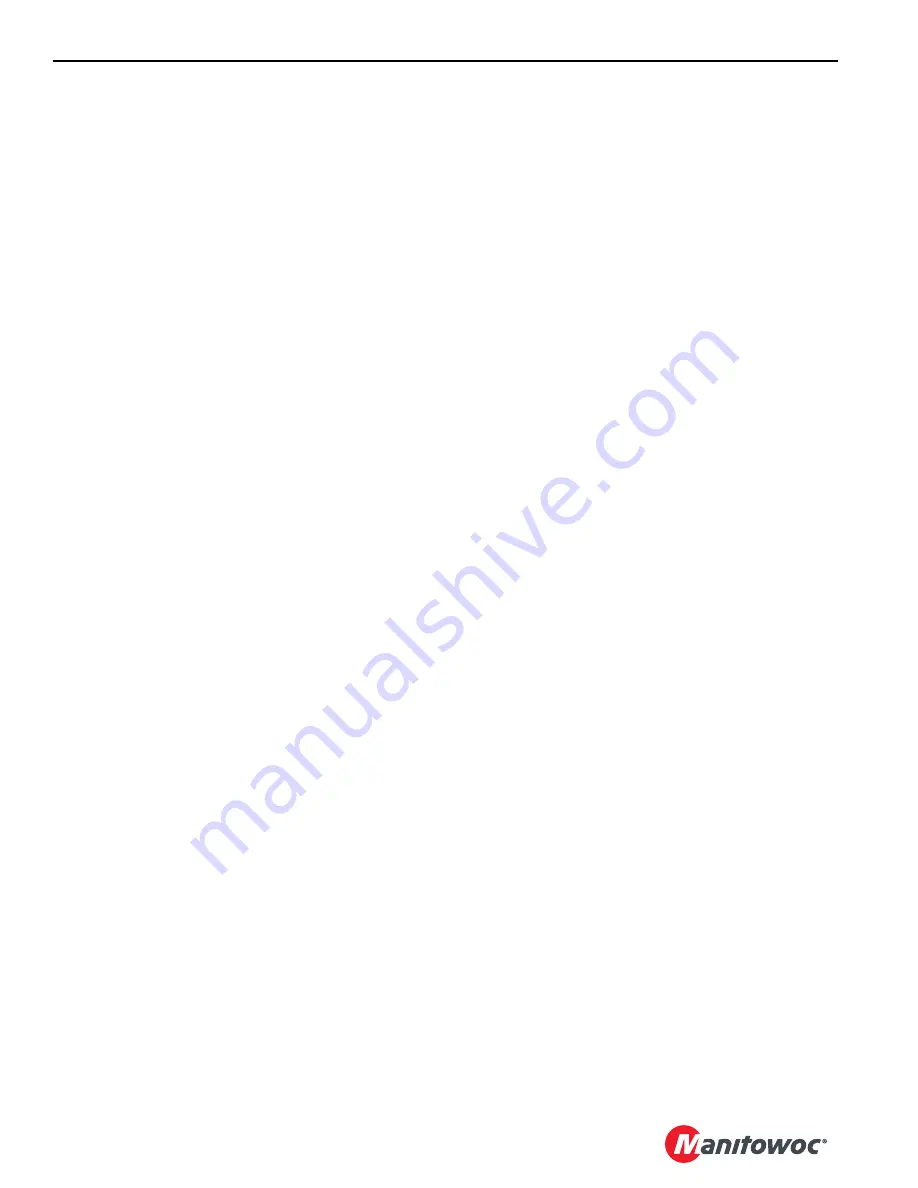
Reference
Only
INTRODUCTION
18000 SERIVCE/MAINTENANCE MANUAL
1-58
Published 12-05-17, Control # 035-23
Mast Hoist Raising to Transport Position
The following drum raising operation is for mast hoist (Drum
5) while lowering from 160° to transport position 0° (mast
raising). Node-4 controller monitors the mast angle sensor in
Setup mode.
When Setup mode is selected, Node-4 controller sends a 24
volt output to drum 5 diverting solenoid valve HS-14 to shift
solenoid valve and apply hydraulic pressure to shift diverting
valve to open lines to drum 5 motor and close lines to main
hoist 2 motor.
When mast hoist (Drum 5) control handle is moved back for
raising
, an input voltage of 2.6 volts or more is sent to node-
1 controller. Node-3 controller sends a variable zero to 24
volt output that is divided by a resistor and applied to main
hoist pump 2/5 EDC in the raise direction.
Main hoist 2/5 pump EDC tilts the swashplate in the raise
direction to satisfy pressure memory. Node-1 controller
compares drum holding pressure to value in pressure
memory. When system pressure is high enough, node-6
controller sends a 24 volt output to drum brake solenoid
valve HS-11. The drum brake solenoid shifts to block drain
port and opens charge pressure port from pump 2/5 to
release brake.
When brake is released, node-3 controller sends a 24 volt
output voltage to pump EDC to tilt swashplate to stroke
pump in the raise direction. In the raise direction, hydraulic
fluid flow is from port B of pump to port A of motor. Return
fluid is from port B of motor to port A of pump. As mast raises
to transport position, mast hoist drum hauls in wire rope
between mast drum and gantry sheaves.
Before the mast is raised to 114°, mast angle sensor sends
an input voltage to node-1 controller. Node-3 controller
sends a 24 volt output to enable mast raising cylinders
solenoid valve HS-33 in extend direction. The mast raising
cylinders extend sequence is explained in “Mast Hoist
Raising from Transport Position”.
When the mast is raised to 114°, the live mast is resting on
the cylinder arms. The accessory system pressure builds
with the actual pressure between a minimum of 3,000-psi
(207 bar) at the beginning and 4,000 psi (276 bar) after the
mast cylinders start moving down.
From the accessory valve, the fluid pressure enters free-flow
check valve sections on side “B” of load equalizing valve.
From equalizing valve, fluid enters counterbalance valves
and rod end of mast cylinders, retracting cylinder rods.
Fluid flow from piston end of mast raising cylinders is
blocked by free-flow check valve sections on side “A” of
counterbalance valves and flows through valve flow restrain
sections preset for a relief pressure of 3,500 psi (240 bar).
Counterbalance valves operate with a 5:1 pilot ratio of the
relief valve pressure, permitting valve to open when pressure
in piston end of the cylinders is approximately 700 psi (48
bar).
Hydraulic fluid from side “A” sections of both counterbalance
valves combines, and the free-flow check valve section on
side “A” of load equalizing valve blocks the flow. The fluid
then passes through the valve flow restrain section that is
preset at 4,000 psi (276 bar). Load equalizing valve operates
with a 1.5:1 pilot ratio of the relief valve pressure, permitting
valve to open when the hydraulic pressure on side “A” of the
load-equalizing valve is approximately 2,670 psi (185 bar).
Restraining section on side “B” of load equalizing valve
opens, controlling flow of fluid out of the cylinders to ensuring
cylinder operation is balanced.
When the mast cylinders are retracting, node-3 controller
monitors mast hoist drum speed sensor. Node-1 controller
maintains a speed that is proportional to accessory system
hydraulic pressure applied to the mast raising cylinders.
Node-3 controller output voltage to pump EDC is relative to
control handle movement. The system pump varies flow to
keep drum at handle command setting. As control handle is
moved back, an output voltage increases the pump
swashplate angle.
Node-4 controller monitors the mast angle sensor when
mast is moving. When mast is at 0°, node-3 controller sends
a zero output voltage to pump EDC that moves swashplate
to center position. After control handle center switch opens,
node-6 controller also sends a zero output voltage to disable
mast hoist brake solenoid valve HS-11 to apply brake before
mast hoist pump de-strokes.
Node-4 controller sends a zero output voltage to shift spool
of mast raising cylinder solenoid valve HS-34 to center
position.
Summary of Contents for 18000
Page 1: ...R e f e r e n c e O n l y Service Maintenance Manual Manitowoc 18000 ...
Page 2: ...R e f e r e n c e O n l y ...
Page 4: ...R e f e r e n c e O n l y THE ORIGINAL LANGUAGE OF THIS PUBLICATION IS ENGLISH ...
Page 210: ...R e f e r e n c e O n l y NOTES SKETCHES AND PHOTOGRAPHS ...
Page 315: ...R e f e r e n c e O n l y ...
Page 316: ...R e f e r e n c e O n l y ...