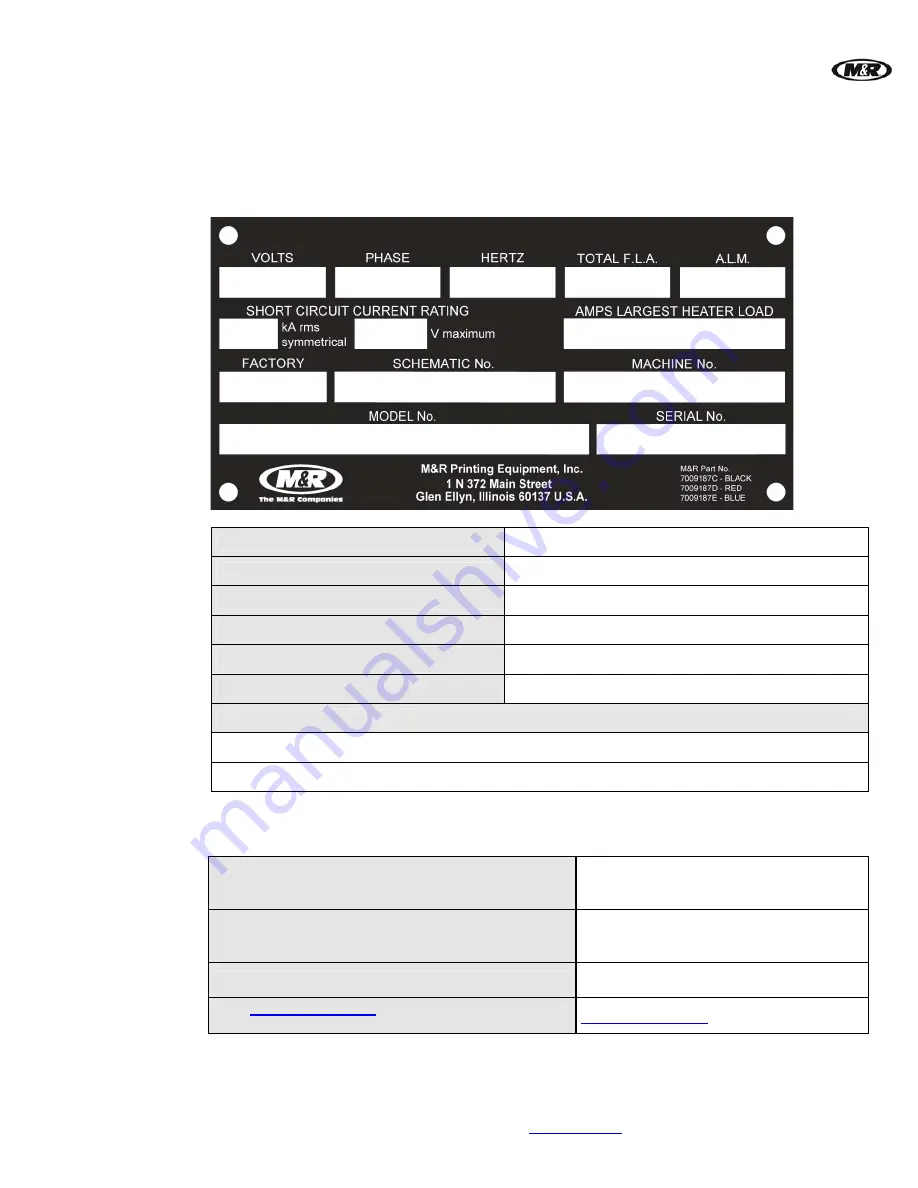
V.033007
Sprint
®
2000
2.1
Service and Parts
Manufacturer’s
Rating Plate
Most products manufactured by the M&R Companies carry a metal manufacturer’s rating plate similar
to the one shown below. Please use it to fill out the product information below, and be prepared to
provide the identification information when calling. This helps us respond to your needs more quickly.
Model No.
Machine No.
Serial No.
Schematic No.
Date Installed
Installed by
Optional Features and Special Information
Contacting M&R
If you need service or have questions about your equipment, call the appropriate number and ask for
Technical Support. If you need parts, ask for the Parts Department.
From the United States & Canada
Monday-Friday between 8:30 AM and 5:00 PM
Central Standard/Daylight Time
800-736-6431
Or
630-858-6101
From all other countries
Monday-Friday between 14:30 and 23:00 Greenwich
Mean Time (GMT)
+847-967-4461
Outside Regular Hours
Call our Global Hotline:
+630-462-4715
Visit
contacts
M&R Companies 1N 372 Main St. Glen Ellyn, IL 60137 USA
9
Tel: +630-858-6101 Fax: +630-858-6134
www.mrprint.com