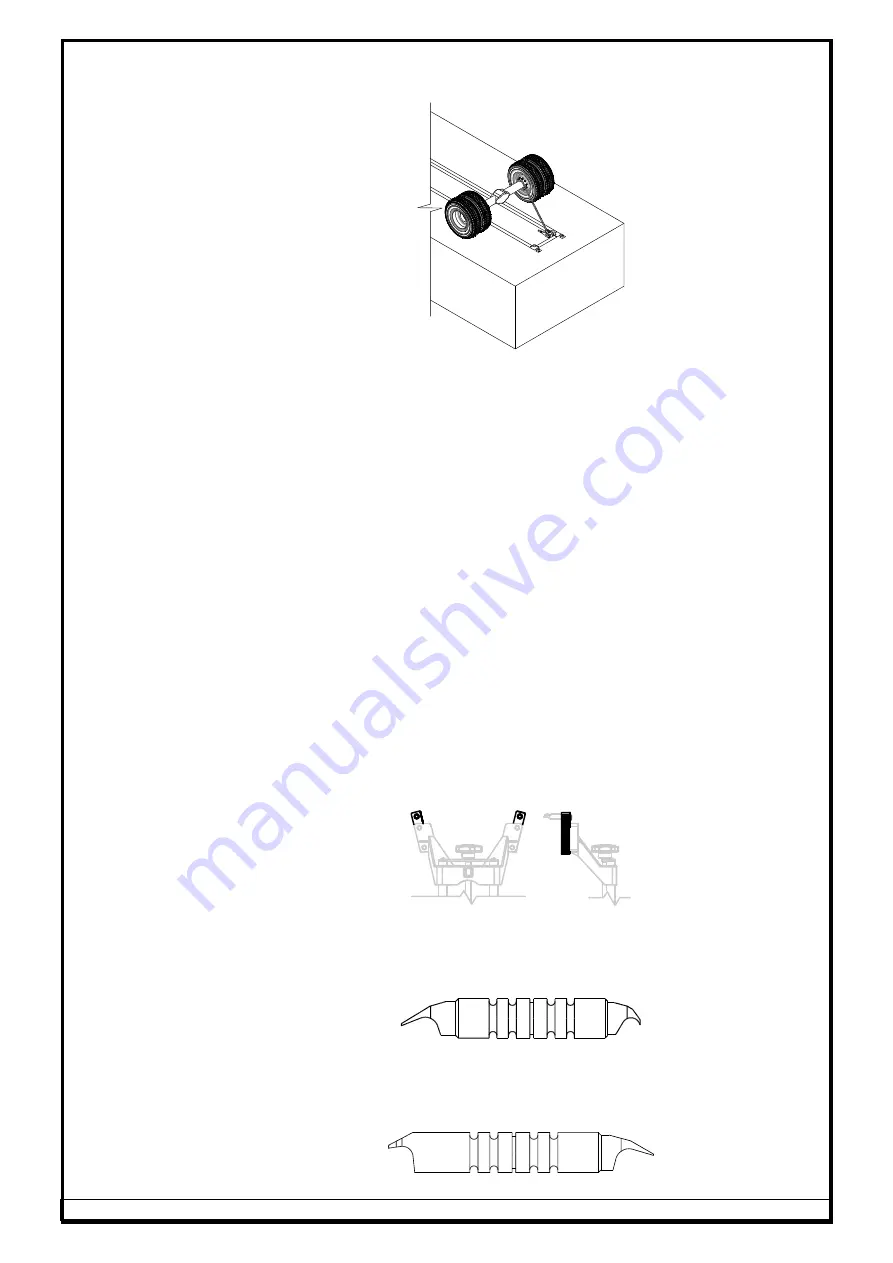
Ref.: MEL-WA(3D HCV) - OM Ver.1.7
36
6.9.13. RATCHET WITH CHAIN BLOCK
This accessory is provided for adjusting the Thrust angle in HCV vehicles with
single rear axle.
Fig. 46
6.9.14. PLASTIC TOOL BOX & ORGANIZER
A box is provided to store the Rim locking pins and adapters safely without
damaging it when not in use.
6.9.15. DATA MANAGER SOFTWARE
Data manager is a smart customized software package available with
alignment program for monitoring the condition of various vehicles aligned by
the equipment and the performance of Wheel alignment centre on the whole.
Reminder letters are automatically generated for existing customer base
periodically, which helps in increasing the revenue for the garage.
6.10.
OPTIONAL ACCESSORIES
(Refer scope of supply)
6.10.1. WHEEL BRACKET (HCV)
– 15” to 28”
The Wheel bracket is a versatile design to accommodate Wheel rims ranging
from 15" to 28" of diameter.
6.10.2. WHEEL BRACKET EXTENSION ADAPTER
This Adapter is very useful for clamping wheel rims of 24
” to 30” dia., while
using along with Wheel
bracket (whose clamping range is 12”-24” dia). This
adapter can cover wheel rims upto 34” dia also, if used along with Wheel
bracket
with 28” clamping range. This adapter eliminates requirement of a
separate Wheel bracket for HCV wheels.
Fig. 47
6.10.3. RIM LOCKING PIN
– Double sided (for Steel cast rims)
This Rim locking pin of 90mm Lg. is developed for clamping different kind of
HCV Steel cast rim profiles, compatible with 24" Wheel bracket.
Fig. 48
6.10.4. RIM LOCKING PIN
– Double sided (for Low contour steel rims)
This Rim locking pin of 90mm Lg. is developed for clamping different kind of
HCV Low contour steel rim profiles, compatible with 24" Wheel bracket.
Fig. 49