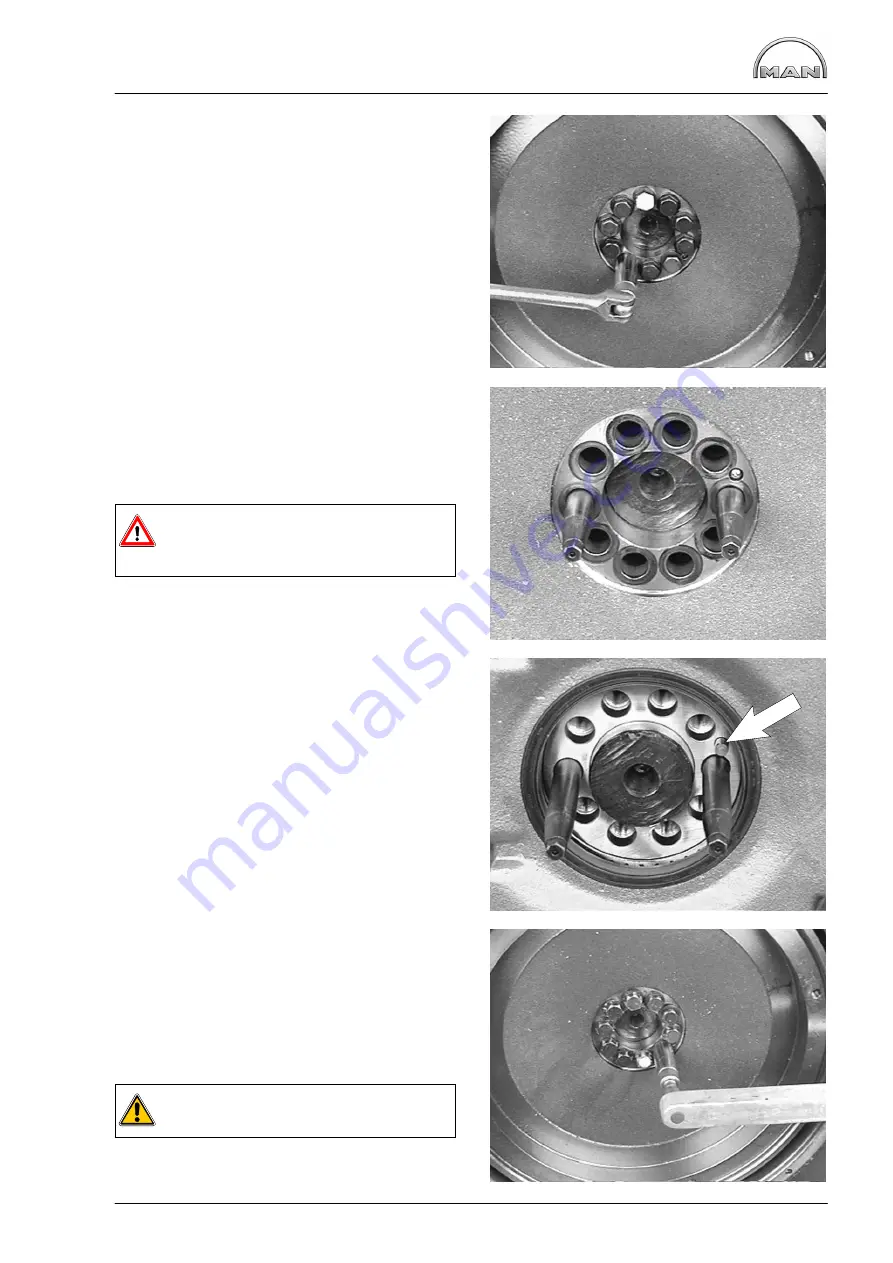
1
2
3
4
Removing and installing flywheel,
Replacing starter gear ring
77
Removing flywheel
Fig. 1
Release the mounting bolts, securing the engine
against rotating if necessary.
Fig. 2
Unscrew two bolts opposite one another and re-
place with two guide mandrels (special tool).
Remove all the bolts.
Pull off the flywheel with suitable lifting gear.
Danger:
The flywheel is heavy!
Use lifting gear.
Fitting the flywheel
Fig. 3
Insert the guide pins.
Coat the sealing face on the inside of the flywheel
with “Antipor 46” sealing compound.
Place guide mandrels on the flywheel; in doing so,
pay attention to the assignment of the centring pin
(arrow) to the hole in the flywheel.
Push the flywheel on as far as it will go.
Fig. 4
Lightly oil the new mounting bolts (stress bolts),
screw them in and tighten in diagonal sequence to
the specified torque.
Pretightening: 100
−
110 Nm
1st angle tightening: 90
_
2nd angle tightening: 90
_
Caution:
Unblock the crank gear!
D
Install rpm sensor
Summary of Contents for D 2840 LE 301
Page 1: ......
Page 2: ......
Page 16: ...Notes 14...
Page 20: ...Engine views 18 Engine views D 2842 LE 301 9 10 11 12 9 8 6 5 4 3 2 1 13 14 15 16 17 18 6 7 8...
Page 150: ...Notes 148...
Page 151: ...149 Service Data...
Page 179: ...177 Special tools...
Page 180: ...Special tools 178 2 3 4 5 6 7 8 1 6 1 6 2 6 3 9 1 9 2 9 3 9...
Page 184: ...Special tools 182 21 22 25 25 2 24 25 1 26 27 1 27 2 27 20 1 19 2 19 1 20 2 19 20 28 23...
Page 186: ...Special tools 184 30 29 32 31 33...
Page 193: ......
Page 194: ......