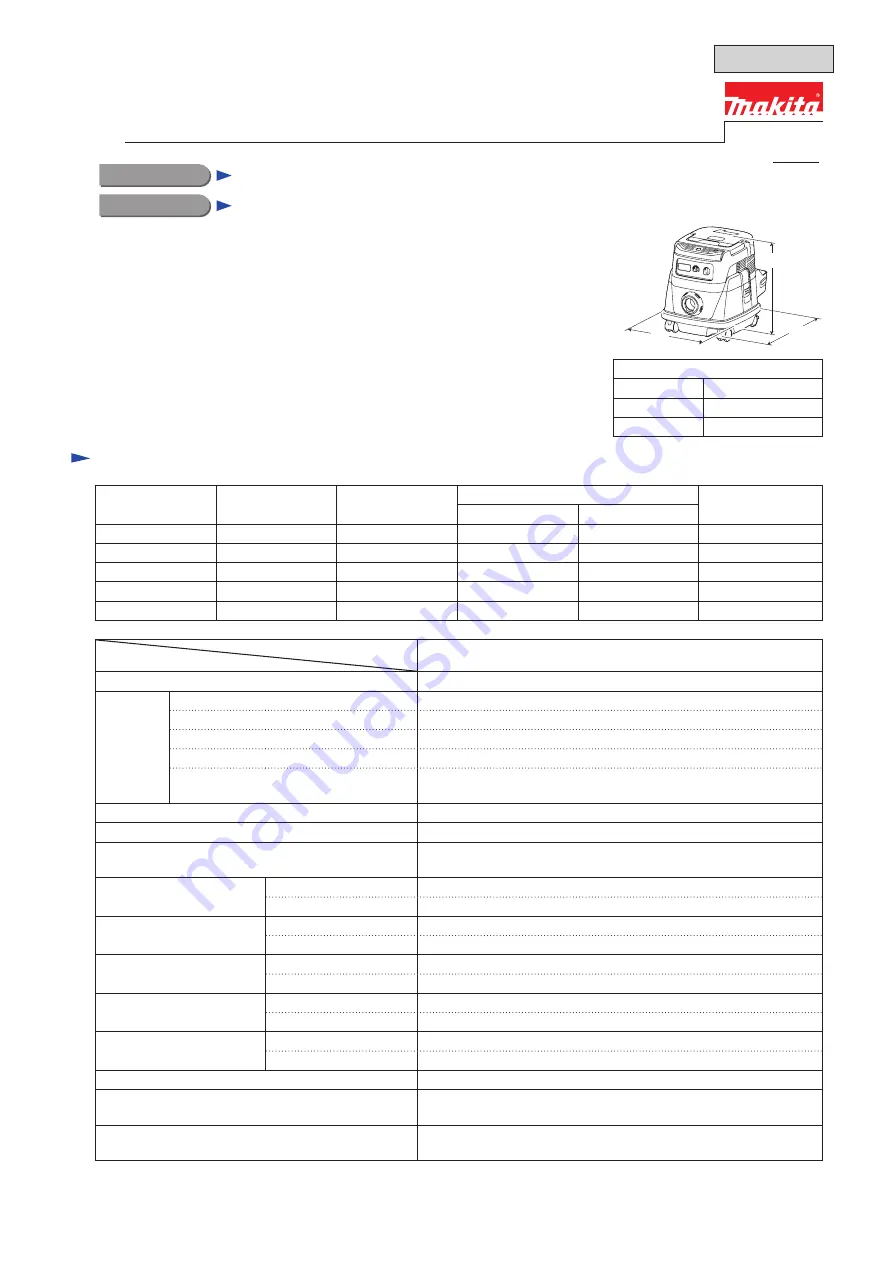
C
ONCEPT AND MAIN APPLICATIONS
Model DVC860L is a corded and cordless vacuum cleaner powered by AC and
two 18V Li-ion batteries in series.
Its main features are as follows:
• Cloth filter type; for both Wet & Dry vacuum cleaning
• Large on-off switch; also equipped with main power switch
• Variable suction power control by dial
• Dual battery fuel gauge
• Removable storage box
• Removable power supply cord
for better maneuverability
Note:
Not compatible with 1.3Ah Li-ion battery BL1815.
S
pecification
Model
Specification
DVC860L
Power unit
AC/DC
Battery
Voltage: V
36 (18x2)
Capacity: Ah
1.5, 2.0, 3.0, 4.0, 5.0
Energy capacity: Wh
27x2, 36x2, 54x2, 72x2, 90x2
Cell
Li-ion
Charging time (approx): min
15, 24, 22, 36, 45 with DC18RD
15x2, 24x2, 22x2, 36x2, 45x2 with DC18RC
Wet/Dry type
Wet & Dry
Variable suction power control
Yes (by dial)
Continuous run time (approx.) on a single full
battery charge: minute
30 - 65 with two batteries BL1850; BL1850B
Suction power: W
on DC power
70 - 25
on AC power
320
Max sealed suction: kPa
on DC power
9
on AC power
24
Max air flow: m
3
/ minute on DC power
2.1
on AC power
3.6
Tank capacity: L
Wet
6
Dry
8
Noise: dB
on DC power
64
on AC power
75
Protection from electric shock
Double insulation
Power supply cord: m (ft)
*
1
North American countries: 6.0 (19.7),
Other countries: 5.0 (16.4)
Weight according to
EPTA-Procedure 01/2003
*
2
: kg (lbs)
8.6 (19.0)
*
3
, 9.2 (20.3)
*
4
Dimensions: mm ( " )
Length (L)
366 (14-3/8)
Width (W)
334 (13-1/8)
Height (H)
368 (14-1/2)
*1
As for the shord cord, connection cord is included.
*2
With Plastic dust bag 650x650
*3
With two batteries BL1815N; BL1820
*4
With two batteries BL1830; BL1840, BL1840B; BL1850, BL1850B
Voltage (V)
Current (A)
Cycle (Hz)
Continuous Rating (W)
Max. Output (W)
Input
Output
110
10
50/60
1,050
---
---
120
9.2
50/60
---
---
---
220
5
50/60
1,050
---
---
230
4.8
50/60
1,050
---
---
240
4.6
50/60
1,050
---
---
OFFICIAL USE
for ASC & Sales Shop
T
ECHNICAL INFORMATION
Model No.
Description
Corded and Cordless Vacuum Cleaner
DVC860L
L
W
H
PRODUCT
P 1/ 2
9
October 2015