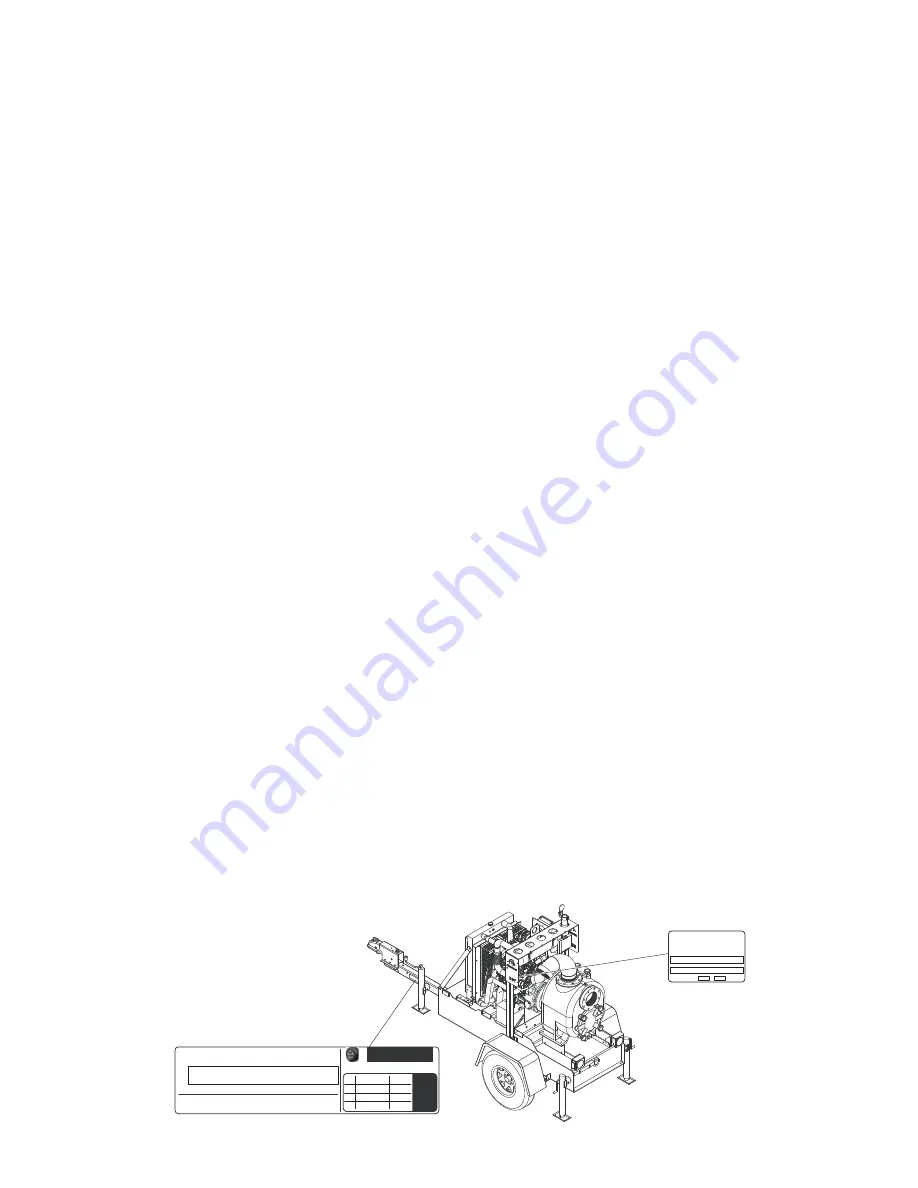
9
•
Connect safety chains in a crossing pattern under the tongue and
ATTACH THE BREAKAWAY
CABLE TO THE REAR BUMPER OF THE TOWING VEHICLE.
Do not attach the cable to the trailer
hitch.
•
Make sure directional and brake lights on the trailer are connected and working properly.
•
Check that all lug nuts holding wheels on are tight and that none are missing.
•
Maximum recommended speed for highway towing is 45 mph (72 km/h). Recommended off-road
towing speed is not to exceed 10 mph (16 km/h) or less, depending on terrain.
The trailer is equipped with hydraulic surge brakes or electric surge brakes. Check the operation of the
brakes by braking the vehicle at a slow speed before entering traffic. Both the trailer and the vehicle should
brake smoothly. If the trailer seems to be pushing, check the level in the surge brake fluid reservoir.
When towing, maintain extra space between vehicles and avoid soft shoulders, curbs and sudden lane
changes. If you have not pulled a trailer before, practice turning, stopping, and backing up in an area away
from heavy traffic.
A film of grease on the coupler will extend coupler life and eliminate squeaking. Wipe the coupler clean
and apply fresh grease each time the trailer is towed.
REPORTING TRAILER SAFETY DEFECTS
If you believe your trailer has a defect which could cause a crash or could cause injury or death, you should immediately
inform the National Highway Traffic Safety Administration (NHTSA) in addition to notifying Magnum Power Products
LLC.
If NHTSA receives similar complaints, it may open an investigation; and if it finds that a safety defect exists in a group
of vehicles, it may order a recall and remedy campaign. However, NHTSA cannot become involved in individual
problems between you, your dealer, or Magnum Power Products LLC.
To contact NHTSA, you may either call the Auto Safety Hotline toll-free at 1-888-327-4236 (TTY:1-800-424-9153),
go to http://www.safercar.gov; or write to:
Administrator
NHTSA
1200 New Jersey Avenue S.E.
Washington, DC 20590
You can also obtain other information about motor vehicle safety from http://www.safercar.gov.
UNIT SERIAL NUMBER LOCATIONS
Refer to the locations illustrated to find the unit ID tag and VIN tag on your unit. Important information, such as the
unit serial number, model number, and Vehicle Identification Number (VIN) for your trailer are found on these tags.
Record the information from these tags so it is available if the tags are lost or damaged. When ordering parts or
requesting technical service information, you may be asked to provide this information.
MAGNUM POWER PRODUCTS LLC
Manufactured by
A wholly owned subsidiary of
Generac Power Systems, Inc.
215 Power Drive • Berlin, WI 54923
1-800-926-9768
MODEL
kg
lbs
SERIAL NUMBER
MADE IN USA
Unit ID Tag
VIN Tag
TIRE AND LOADING INFORMATION
RENSEIGNEMENTS SUR LES
PNEUS ET LE CHARGEMENT
SEE OWNER’S
MANUAL FOR
ADDITIONAL
INFORMATION
VOIR LE
MANUEL DE
L’USAGER
POUR
PLUS DE
RENSEIGNEMENTS
MANUFACTURED BY/FABRIQUE PAR: Magnum Power Products LLC
DATE: 00/0000
GVWR/PNBV:
000KG
(0000LBS)
COLD
INF.
PRESS./
PRESS.
DE
V.I.N./N.I.V.:
00000000000000000
TYPE:
TRAILER
MODEL:
XXX000
GAWR / PNBE
TIRE / PNEU
RIM / JANTE
GONF A FROID - KPA(PSI/LPC) SGL / DUAL
EACH
AXLE
THIS VEHICLE CONFORMS TO ALL APPLICABLE STANDARDS PRESCRIBED UNDER THE U.S. FEDERAL MOTOR VEHICLE SAFETY STANDARDS(FMVSS) AND CANADIAN
MOTOR VEHICLE SAFETY REGULATIONS IN EFFECT ON THE DATE OF MANUFACTURE.
CE VEHICULE EST CONFORME A TOUTES LES NORMES QUI LUI SONT APPLICABLES EN VERTU DU REGLEMENT SUR LA SECURITE DES VEHICULES AUTOMOBILES DU CANADA EN VIGUEUR A LA DATE SA
FABRICATION.
The weight of cargo should never exceed 0000KG (0000LBS)
Le poids du chargement ne doit jamais depasser 0000KG (0000LBS)