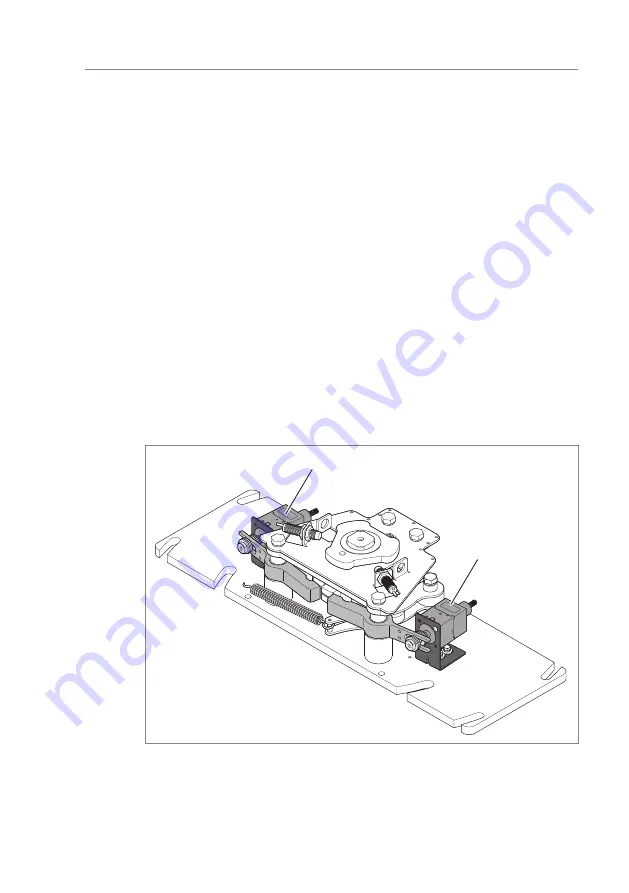
79
MPT-333
Converting the locking unit
14
Converting the locking unit
14.1
Safety during conversion
Qualification of personnel
Cleaning and maintenance
›
Technician
›
Electrical specialist
ä
Personal protective equipment
Wear the following personal protective equipment:
›
Work clothes
›
Protective gloves
›
Safety shoes
›
Protective helmet.
By default, the locking unit is delivered with the configuration "normally open".
Ma
g0088
7
1
2
Fig. 37: Locking unit configuration "Normally open"
1 Magnet RL1
2 Magnet RL2
Summary of Contents for MPT-333
Page 1: ...Operating Instructions Full Height Turnstile MPT 333 Doc ID 5817 0028EN Version 00...
Page 89: ...89 MPT 333...
Page 90: ...90 MPT 333...
Page 91: ...91 MPT 333...