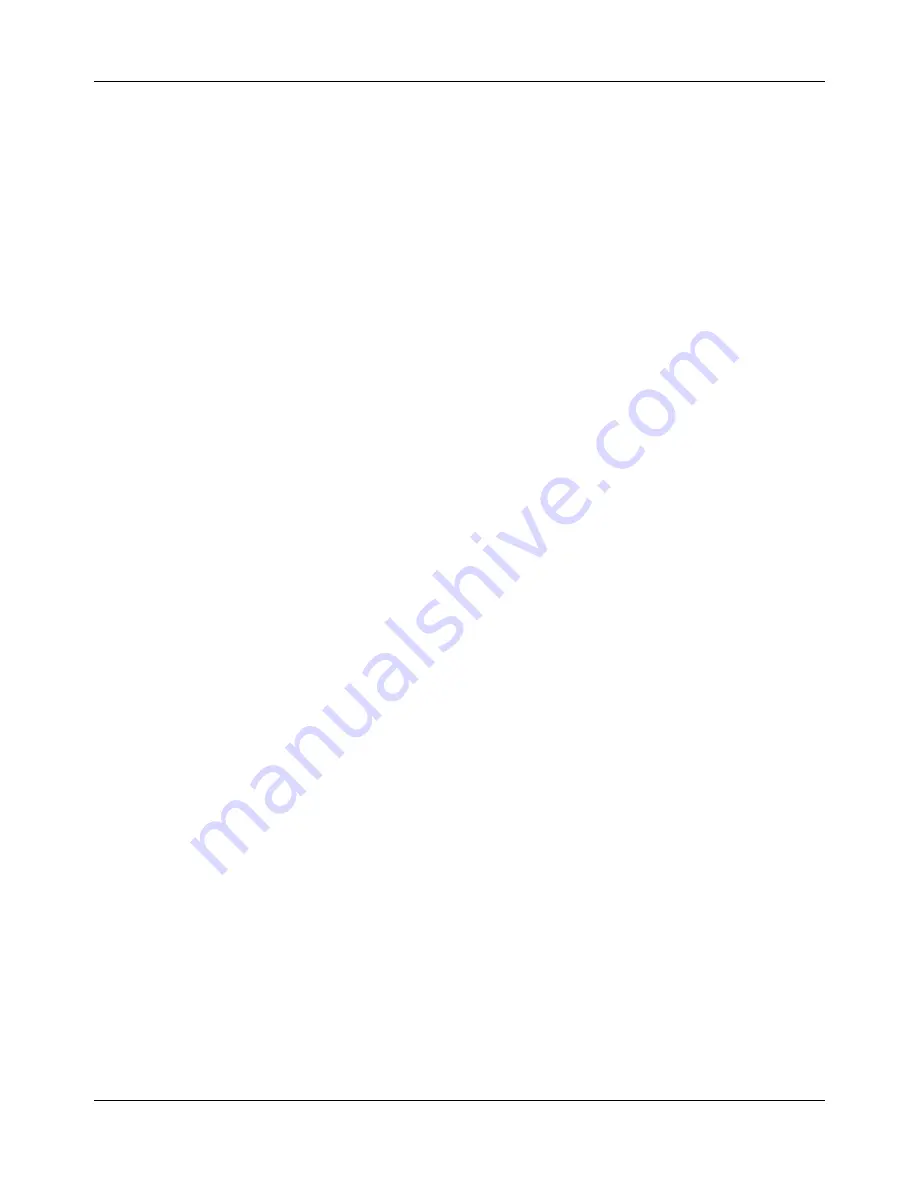
Design Guidelines
Transport System Design
8
MagneMotion
Rockwell Automation Publication MMI-UM002E-EN-P - March 2016
Transport System Design
Overview
This section describes some of the basic considerations for designing a track system for a
MagneMover LITE transport system. The track system includes the guideway, the guideway
supports, the MM LITE railless motors, the vehicles with magnet arrays, and the mechanism
for mounting the motors to the guideway (refer to
for
layout guidelines).
One advantage of the MagneMover LITE transport system is that it is possible to have vehi-
cles move at different rates of speed in the same direction, or in opposite directions without a
collision. The control software ensures that the minimum distance between vehicles (pucks)
when not moving is 3 mm [0.1 in] (refer to
Design Guidelines
Use standard engineering practices to reduce torque, vibration, and other stresses on the
guideway and other parts of the system. Factors specific to MagneMover LITE transport sys-
tems to consider include:
•
Vehicles (pucks) are not held in place if power is removed.
•
There is no magnetic attractive force between the magnet array and the MagneMover
LITE motors.
•
The Vehicle Gap (distance between magnet array and motor, see
maintained throughout the system.
•
The Downstream Gap (distance between motors, see
possible to ensure there is enough thrust to move the vehicle over the gap.
•
Process stations should not be located where the center of the magnet array would be
within the Downstream Gap between motors as settling time and repeatability may be
negatively affected.
•
Ensure the track system configuration accounts for power and communication connec-
tions and all cables.
•
Ensure the transport system configuration accounts for points for grounding the track
to the facility’s earth ground and for grounding of all motors.
•
When choosing vehicle and guideway materials, consider the stresses applied to the
vehicle and guideway during use.
•
When choosing vehicle and guideway materials, consider those that provide low fric-
tion and low wear.
•
When choosing vehicle and guideway materials, consider static electricity dissipation
between the vehicles and the guideway.
•
The vehicle must remain centered over the motors throughout the system.