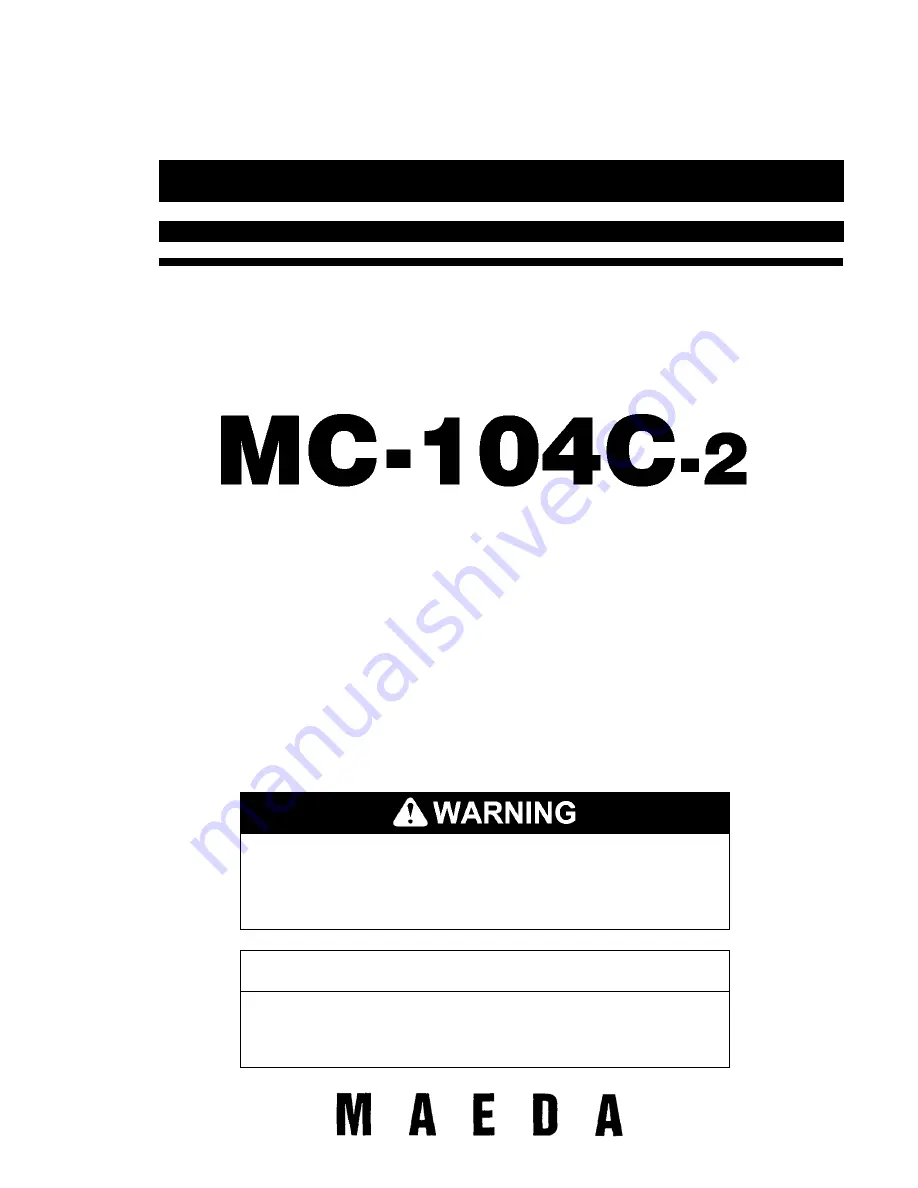
350E-OM0912-03
OPERATION MANUAL
MINI-CRAWLER CRANE
Serial No. M01736
and up
Unsafe use of this machine may cause serious injury or death. Operators
must read this manual before operating this machine. This manual should
be kept near the machine for reference and periodically reviewed by all
personnel who will come into contact with it.
NOTICE
MAEDA has Operation & Maintenance Manuals written in some other
languages. If a foreign language manual is necessary, contact your local
distributor for availability.
Summary of Contents for MC-104C-2
Page 2: ......
Page 6: ...0 4...
Page 48: ...2 30 1 Note for crane performance and outrigger 350 2063300...
Page 52: ...2 34 27 General rules for use Card type 350 2098500...
Page 122: ...3 70...
Page 156: ...4 34...
Page 166: ...5 4 3 TOTAL RATED LOAD CHART 4 WORKING RANGE...
Page 167: ......
Page 169: ......
Page 170: ......
Page 171: ......
Page 172: ......
Page 173: ......
Page 174: ......
Page 175: ......
Page 176: ......
Page 177: ......
Page 178: ......
Page 179: ......
Page 180: ......
Page 181: ......
Page 182: ......
Page 183: ......
Page 184: ......
Page 185: ......
Page 186: ......
Page 187: ......
Page 188: ......
Page 189: ......
Page 190: ......
Page 191: ......
Page 192: ......