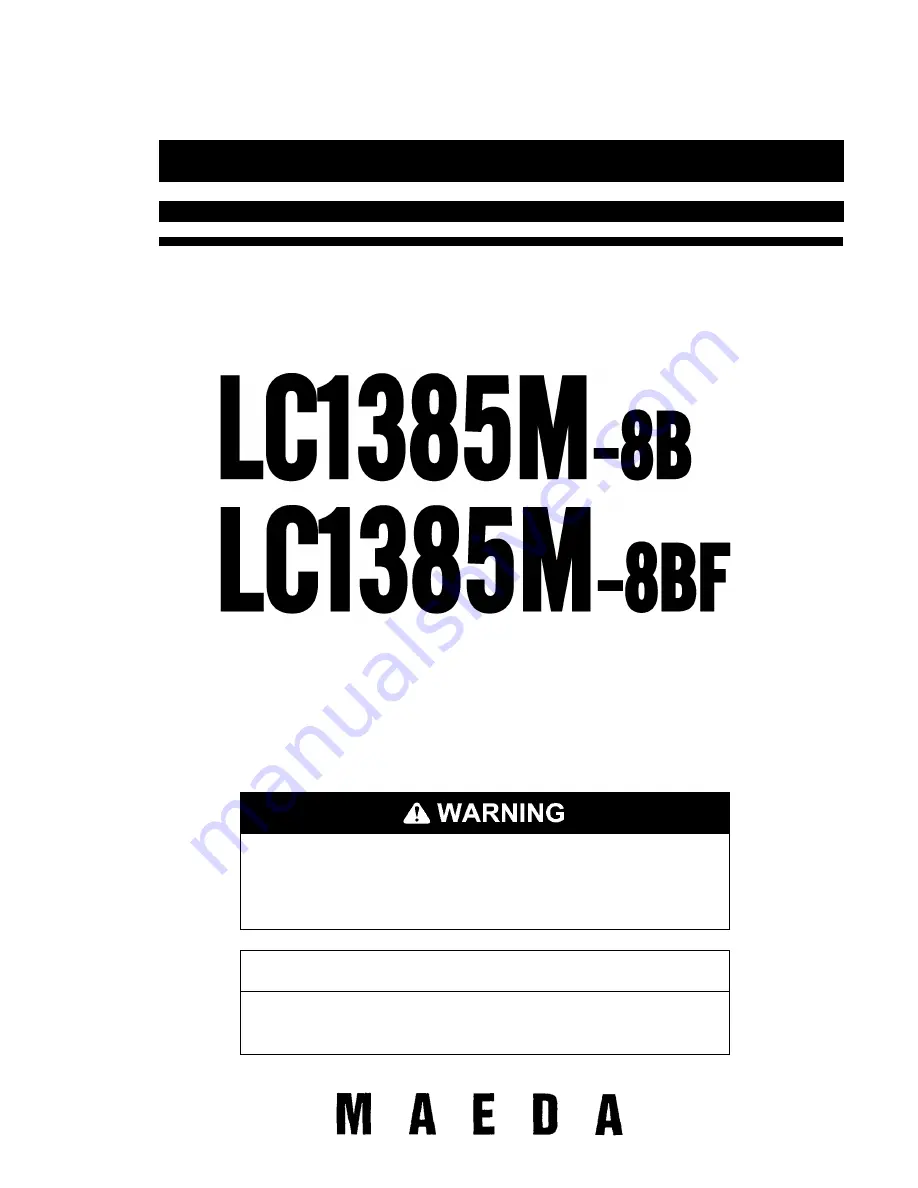
584E-OM0912-02
OPERATION MANUAL
CRAWLER CRANE
Serial No. 8009 and up
Unsafe use of this machine may cause serious injury or death. Operators
must read this manual before operating this machine. This manual should
be kept near the machine for reference and periodically reviewed by all
personnel who will come into contact with it.
NOTICE
MAEDA has Operation Manual written in some other languages. If a foreign
language manual is necessary, contact your local distributor for availability.
Summary of Contents for LC1385M-8B
Page 2: ......
Page 20: ...1 12...
Page 55: ...2 35 SAFETY LABEL LOCATIONS ON CHASSIS...
Page 64: ...2 44...
Page 260: ...3 196...
Page 296: ...4 36...
Page 332: ...4 72...
Page 336: ...5 4 2 SPECIFICATION DIMENSIONAL DRAWING...
Page 340: ...5 8 4 WORKING RADIUS AND LIFTING HEIGHT...
Page 347: ...6 7 3 WORKING RANGE CHART...
Page 383: ......