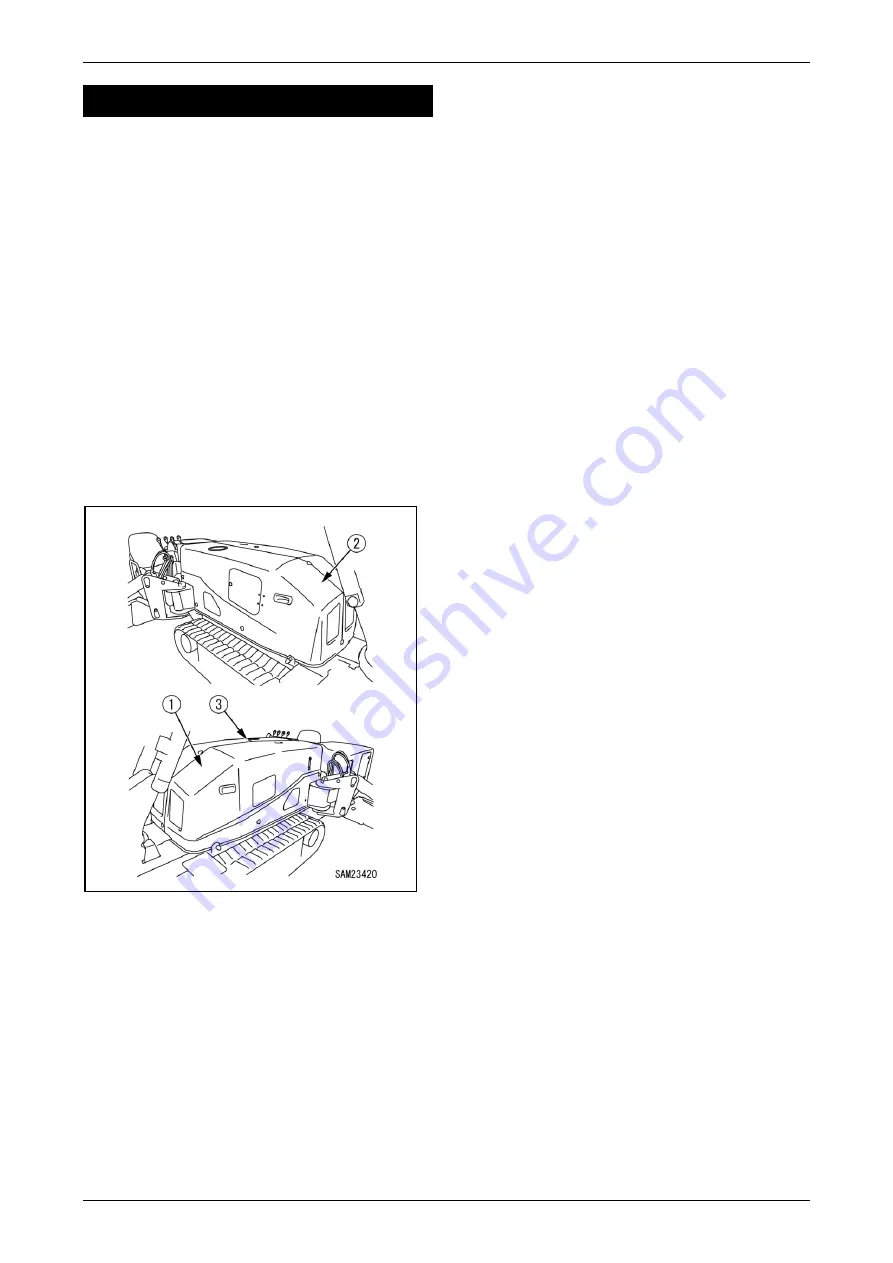
Section 5 – MACHINERY COVER
Mini-Crawler Crane
M A E D A
5-18
3/2019 MC305C-3
MACHINERY COVER
WARNING!
•
Be sure to stop the engine and remove the
starter switch key before removing the
machinery cover.
•
Do not remove the machinery cover
immediately after the operation while the
engine is still hot.
49B
Removing Machinery Cover
Remove the machinery cover with the following
procedure when performing inspection/
maintenance inside the machinery cover.
1. Open all of the outriggers to an angle to allow
removal of the machinery covers.
2. Remove the 10 retaining bolts (3) from the
left-hand machinery cover (1) and right-hand
machinery cover (2).
Fig. 5-23
Four retaining bolts at the top and six at the sides
(three each on the left and right) are used to
tighten with the machinery cover.
3. Pull the left-hand machinery cover (1) to the
side to remove.
4. Pull the right-hand machinery cover (2) to the
side to remove.
50B
Installing Machinery Cover
When you finished inspection/maintenance in the
machinery cover, install the machinery cover
using the following procedure.
1. Reattach the right-hand machinery cover (2)
in its original position.
2. Reattach the left-hand machinery cover (1)
in its original position.
3. Securely tighten the 10 retaining bolts on the
left-hand machinery cover (1) and right-hand
machinery cover (2).
4. Rotate all outriggers back inward to stow.
Summary of Contents for D3001
Page 1: ...103ME OM1903 00 Operation Manual Mini Crawler Crane Serial No D3001 and up...
Page 13: ...3 2019 MC305C 3 1 1 Section 1 INTRODUCTION...
Page 15: ...3 2019 MC305C 3 2 1 Section 2 SAFETY...
Page 24: ...Section 2 SAFETY LABEL LOCATIONS Mini Crawler Crane M A E D A 2 10 3 2019 MC305C 3 Fig 2 2...
Page 41: ...3 2019 MC305C 3 3 1 Section 3 SPECIFICATIONS TERMINOLOGY AND CAPACITY CHARTS...
Page 65: ...3 2019 MC305C 3 4 1 Section 4 OPERATION...
Page 205: ...3 2019 MC305C 3 5 1 Section 5 MAINTENANCE AND INSPECTION...
Page 244: ...Section 5 PERIODIC MAINTENANCE Mini Crawler Crane M A E D A 5 40 3 2019 MC305C 3 Fig 5 61...
Page 294: ......