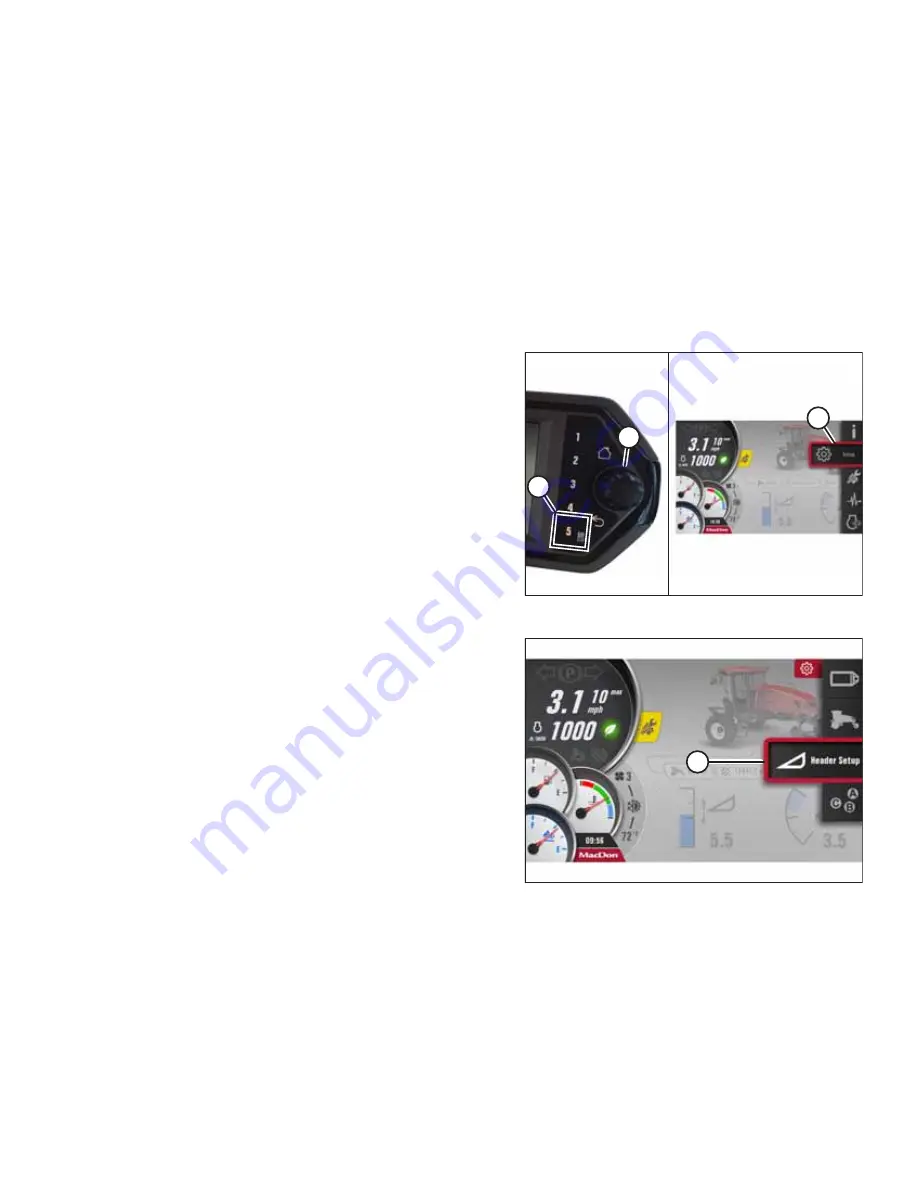
215953
33
Revision A
Chapter 3:
Operation
Safely operating your machine requires familiarizing yourself with its capabilities.
3.1
Activating the Swath Compressor
The swath compressor must be activated in the windrower
’
s control system the first time it is attached to a windrower.
NOTE:
If necessary, refer to the windrower operator
’
s manual to review navigating the Harvest Performance Tracker (HPT) display.
A header must be attached to the windrower.
1.
Turn the ignition key to ON to activate the HPT.
1016140
A
B
C
Figure 3.1: Opening the Main Menu
2.
Press soft key 5 (A) to open the main menu or press SHIFT
and SELECT on the ground speed lever (GSL).
3.
Use the HPT scroll knob (B) or the GSL scroll wheel (not
shown) to place red cursor (C) over the icon you want to
select.
NOTE:
Using the scroll knob will activate titles that explain each
selection.
4.
Press HPT scroll knob (B) or the GSL SELECT button (not
shown) to select the highlighted icon.
NOTE:
Pressing the corresponding soft key will also work.
1021915
A
Figure 3.2: Header Setup Menu
5.
Scroll down and select HEADER SETUP menu (A).