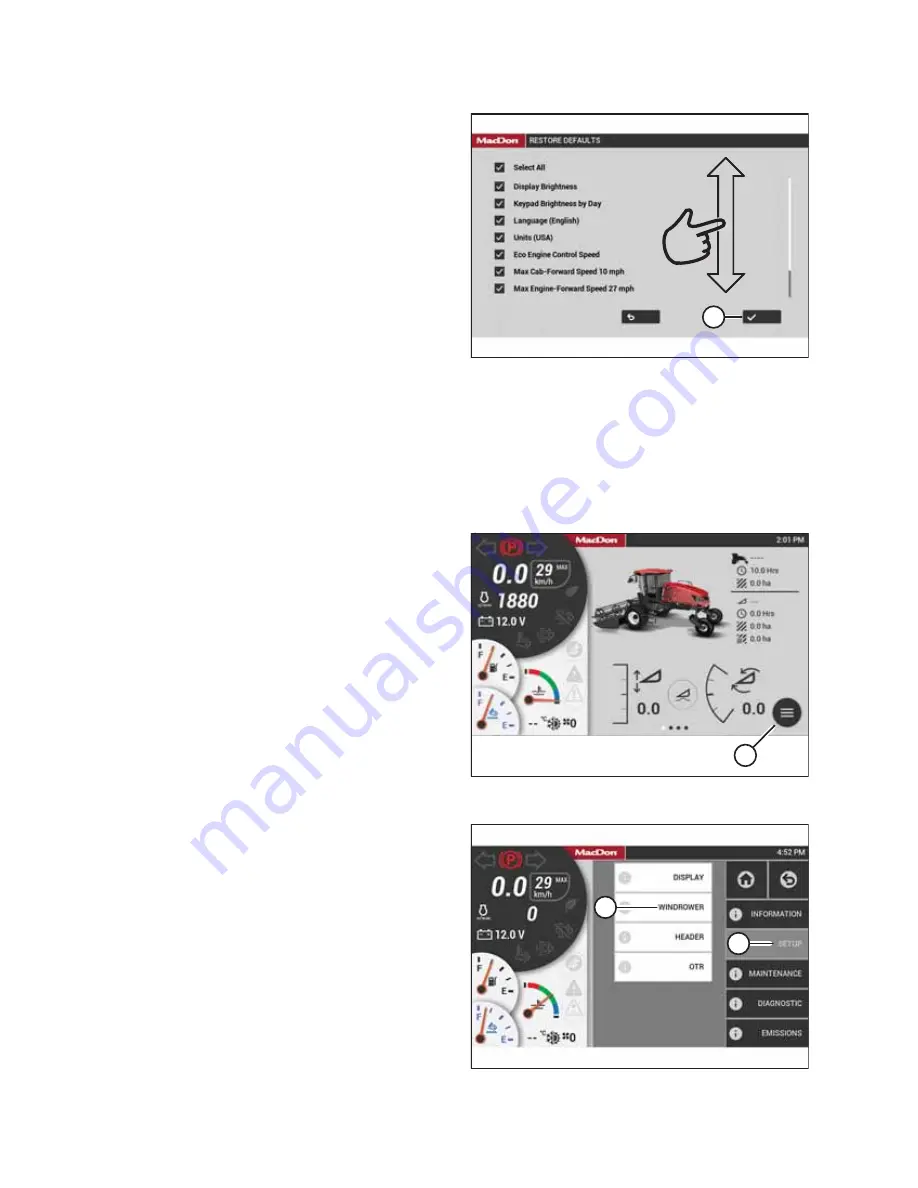
262171
102
Revision A
ϭϬϰϭϵϴϱ
A
Figure 3.118: Restore Defaults Page
4.
Swipe up/down to view the available options. Pressing an
option adds a checkmark that indicates that the option will
be restored.
5.
Once you have selected the options that you wish to
restore, press checkmark (A) to restore.
3.17.12
Activating Control Locks
All header functions are factory-set to the unlocked position, but certain functions can be locked to prevent changes. This
feature can be used to maintain preferred settings when there are multiple Operators.
To activate control locks on header functions, follow these steps:
A
ϭϬϰϭϳϳϯ
Figure 3.119: HarvestTouch
™
Display
1.
Press MENU icon (A) to display the main menu.
ϭϬϰϭϴϵϭ
A
B
Figure 3.120: Setup Menu
2.
Select SETUP (A) and then select WINDROWER (B) from
the menu.