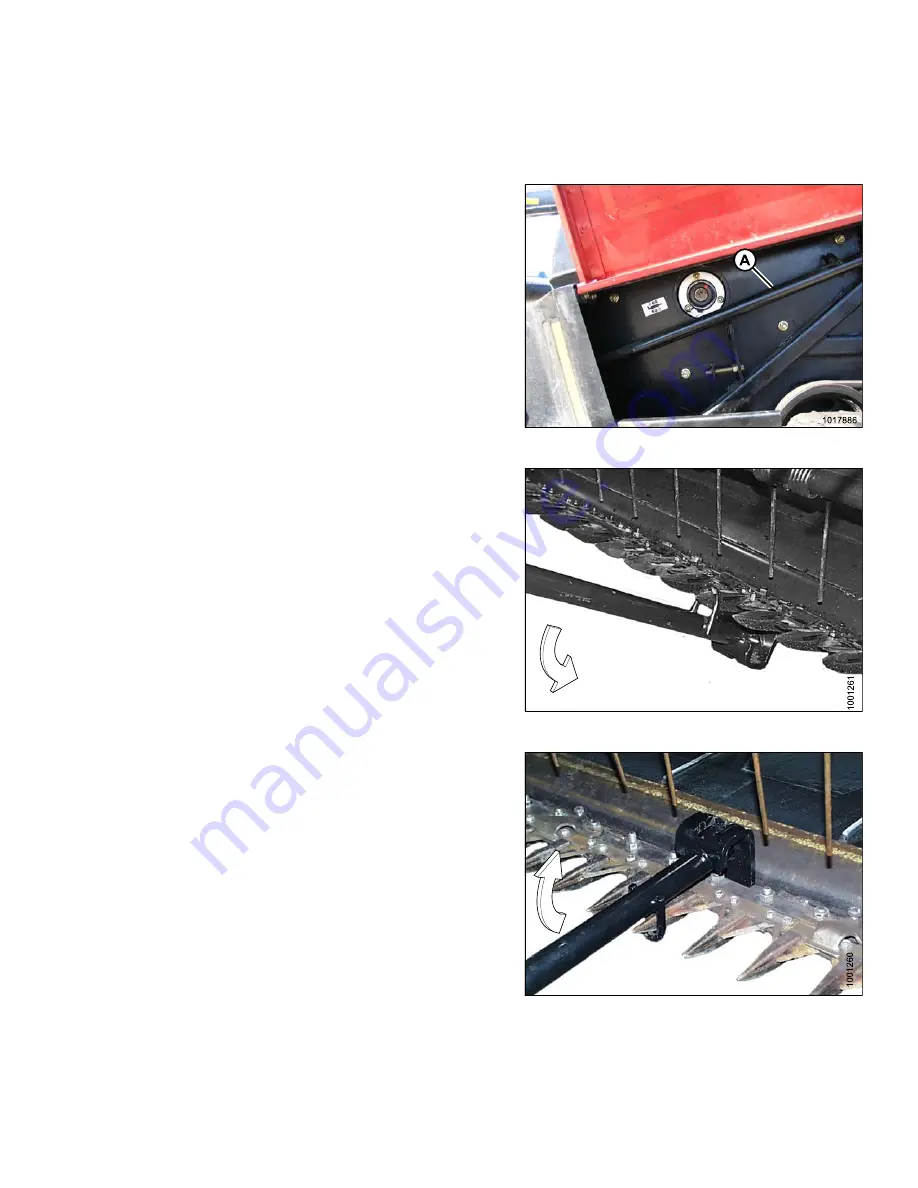
214804
123
Revision A
Aligning Guard
Check daily that guards are aligned to obtain proper shear cut between knife section and guard. Knife sections
should contact shear surface of each guard.
Figure 4.24: Wrench Location
1.
Retrieve tool (A) from left side of header.
Figure 4.25: Guard Tip
–
Downward Adjustment
2.
To adjust guard tips downward, position tool as shown
at right, and push down.
Figure 4.26: Guard Tip
–
Upward Adjustment
3.
To adjust guard tips upward, position tool as shown at
right, and pull up.
NOTE:
If trouble is encountered cutting tangled or
fine-stemmed material, replace guards with stub
guards. If material is tough to cut, install stub guards
with top guard and adjuster plate. A stub guard
conversion kit for the header is available from your
Dealer.
Summary of Contents for A40-D
Page 2: ...MacDon A40D Self Propelled Windrower Auger Header Published November 2018...
Page 3: ...EC Declaration of Conformity Figure 1 EC Declaration of Conformity Page 1 214804 i Revision A...
Page 4: ...Figure 2 EC Declaration of Conformity Page 2 214804 ii Revision A...
Page 14: ......
Page 32: ......
Page 38: ......
Page 127: ...214804 113 Revision A MAINTENANCE AND SERVICING...
Page 206: ......
Page 210: ......
Page 212: ......