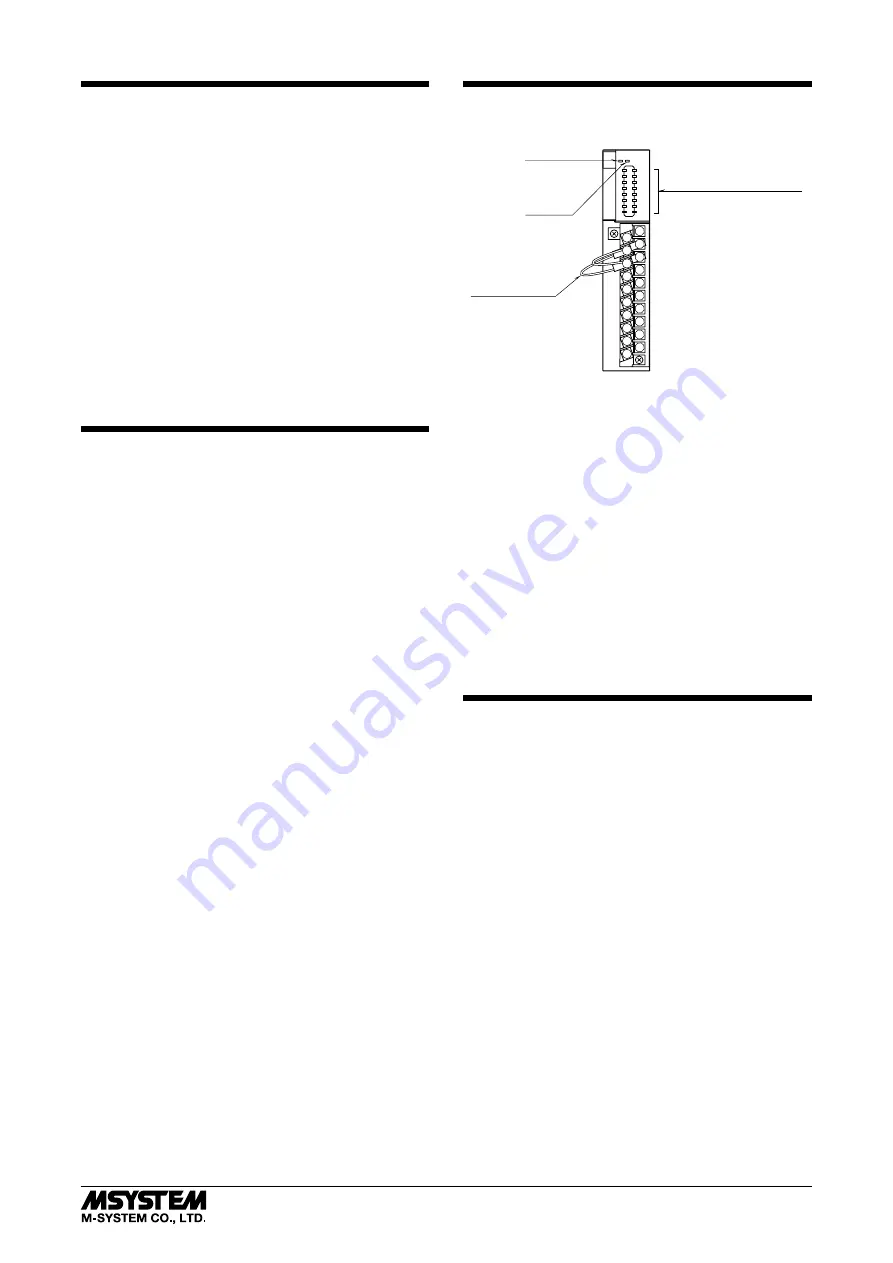
R3-TC2
5-2-55, Minamitsumori, Nishinari-ku, Osaka 557-0063 JAPAN
Phone: +81(6)6659-8201 Fax: +81(6)6659-8510 E-mail: [email protected]
EM-8468 Rev.3 P. 2 / 37
BEFORE USE ....
Thank you for choosing M-System. Before use, please check
contents of the package you received as outlined below.
If you have any problems or questions with the product,
please contact M-System’s Sales Office or representatives.
■
PACKAGE INCLUDES:
Temperature control module
(control CJC sensor, 2 pcs.) .................................(1)
■
MODEL NO.
Confirm Model No. marking on the product to be exactly
what you ordered.
■
INSTRUCTION MANUAL
This manual describes necessary points of caution when
you use this product, including installation, connection and
basic maintenance procedures.
POINTS OF CAUTION
■
HOT INSERTION/REMOVAL OF MODULES
• Removing or replacing modules does not affect other mod-
ules on the same backplane. It is possible to replace them
without removing the power supply. However, replacing
multiple modules at once may greatly change line voltage
levels. We recommend that you replace them one by one.
■
ENVIRONMENT
• Indoor use.
• When heavy dust or metal particles are present in the
air, install the unit inside proper housing with sufficient
ventilation.
• Do not install the unit where it is subjected to continuous
vibration. Do not subject the unit to physical impact.
• Environmental temperature must be within -10 to +55°C
(14 to 131°F) with relative humidity within 30 to 90% RH
in order to ensure adequate life span and operation.
■
WIRING
• Do not install cables close to noise sources (relay drive
cable, high frequency line, etc.).
• Do not bind these cables together with those in which
noises are present. Do not install them in the same duct.
■
UNUSED INPUT CHANNELS
• Unused channels can be specified and set so on the PC
Configurator Software (model: R3CON) without needing
to short at the field terminals.
■
AND ....
• The unit is designed to function as soon as power is sup-
plied, however, a warm up for 10 minutes is required for
satisfying complete performance described in the data
sheet.
COMPONENT IDENTIFICATION
■
FRONT VIEW
1
14
16
18
19
20
5
7
9
10
CJC SENSOR(2)
13
15
17
4
6
8
11
Loop Status Indicator
RUN1
AUTO1
ERR1
ALM1
RUN2
AUTO2
ERR2
ALM2
3
2
13
12
ERR LED
RUN LED
■
STATUS INDICATOR LED
RUN indicator
: Bi-color (red/green) LED;
Red when the internal bus operates normally.
ERR indicator
: Bi-color (red/green) LED;
Red at device error;
Green in normal operating conditions.
Loop status indicators
: Red LED
RUN1
:
Turns on while loop 1 is in operation.
AUTO1
:
Turns on during auto mode, turns off during
manual mode with loop 1
ERR1
:
Turns on at error with loop 1
ALM1
:
Turns on at alarm with loop 1
RUN2
:
Turns on while loop 2 is in operation.
AUTO2
:
Turns on during auto mode, turns off during
manual mode with loop 2
ERR2
:
Turns on at error with loop 2
ALM2
:
Turns on at alarm with loop 2
INSTALLATION
Use the Installation Base (model: R3-BSx).