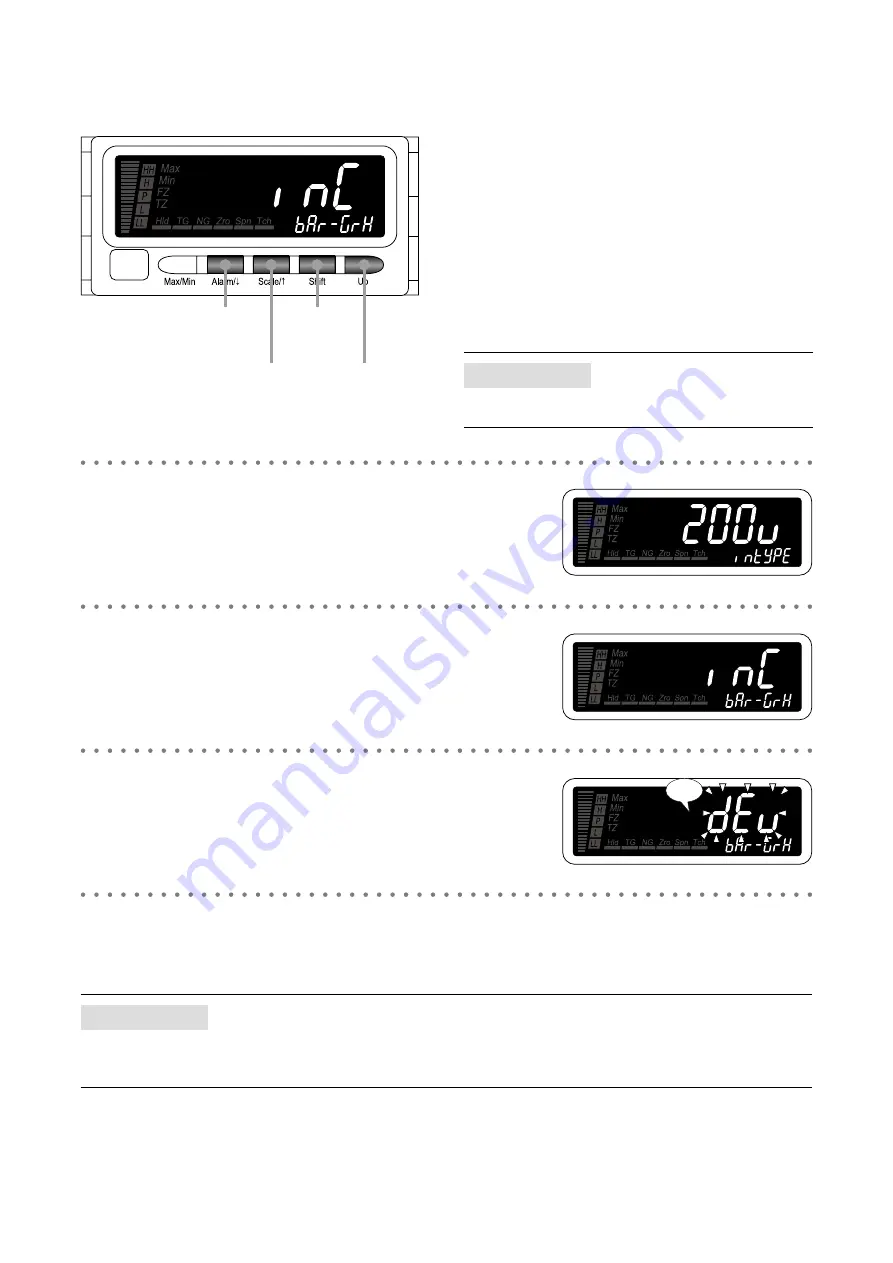
80
47DAC OPERATING MANUAL EM-9518-B Rev.4
7.1 BARGRAPH TYPE
7.1.1 OPERATING PROCEDURE
NOTE
The following figures are display examples. The displays
depend on the specifications and settings.
1
Hold down Scale/
↑
button for 3 seconds or more to move on to
Scaling Setting Mode.
• The input type is indicated.
• The SD indicates ‘INTYPE’.
2
Press Alarm/
↓
or Scale/
↑
button to go to the bargraph type set-
ting.
• The bargraph type is indicated.
• The SD indicates ‘BAR-GRH’.
3
Press Shift and Up buttons to select the bargraph type.
• Select one among ‘INC’, ‘INCR’, ‘DEV’, ‘DEVR’ and ‘OFF’.
4
Press Alarm/
↓
or Scale/
↑
button to apply the new setting.
• And the next parameter setting is indicated.
NOTE
• Press Alarm/
↓
button, and the bargraph lower limit will be indicated (‘BAR-L’ on the SD), or the input type (‘INTYPE’ on
the SD) or the analog output type (‘ANG TYP’ on the SD) will be indicated with the bargraph type set to “no bargraph”.
• Press Scale/
↑
button, and the decimal point position will be indicated (‘D-POINT’ on the SD).
2,4
1,2,
4
3
3
Blinking