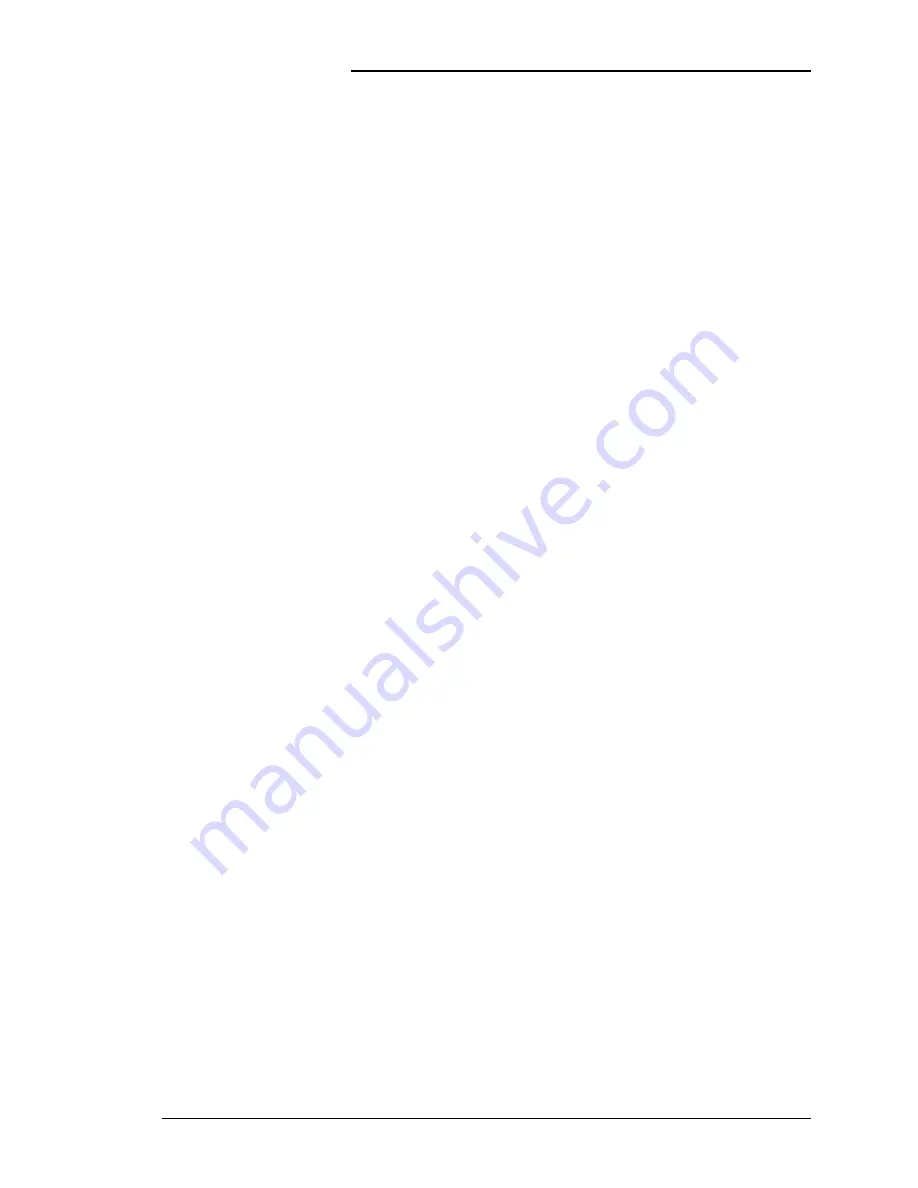
Lucent Technologies Lineage
®
2000 ECS/GPS Battery Plant J85500G-2
Issue 6 May 1999
Engineering, Planning and Ordering 3 - 17
Specify the number of Supplementary Bays required ___
Specifiy the number of Battery Supplemental Bays required ___
Cable and load
breaker sizing
In this section, power cabling for the dc distribution and battery
subsystems is covered, including the following subtopics.
•
maximum and minimum wire gauges
•
wire type
•
crimp lugs
•
circuit breaker selection
To determine actual wire sizes, equipment locations, cable rack
and routing systems at the site must be known. Since the battery
plant shares the cabling system with other building systems,
cabling engineering is not completely defined by this section of
the product manual. In this section, the basics are derived for the
dc power cabling which will be required as part of a complete
cable engineering process. Lucent Technologies offers cabling
engineering services that are separate from battery plant
engineering. Contact your Lucent Technologies Account
Executive for more information on available services.
Use wire type RHW or RHH for dc power wiring. This type of
wire is commonly available in American Wire Gauge (AWG)
Stranded (e.g. KS-5482) and in a finer stranded “welding” type
(e.g. KS-20921). Flexible or Welding Wire is slightly larger than
AWG stranded wire of the same gauge, which may affect the
selection of crimp lugs. For example, different crimp lugs are
required for AWG and Weld wire of the same gauge, for 1/0
gauge and larger. Use flexible power wire (e.g. KS-20921) for
sizes 1/0 and larger in applications requiring tight bends, such as
small battery plants in confined locations.
The terminal lugs that may readily be attached at the dc
distribution subsystem are listed in Tables 3-D and 3-E.