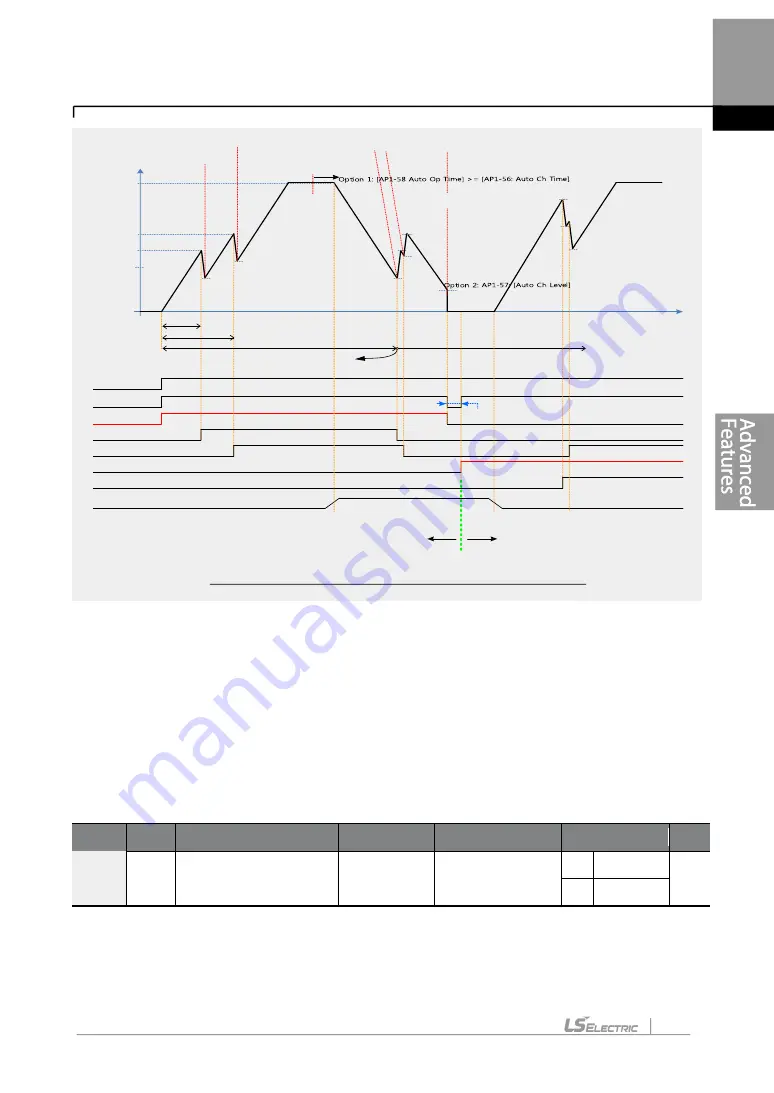
275
Learning Advanced Features
AP1-61
AP1-62
AP1-63
AP1-64
AP1-65
Max Freq
Frequency
AP1-71
AP1-72
Aux Motor 1
Aux Motor 2
Aux Motor 3
Aux Motor 4
Aux Motor 5
Feedback
AP1-71
AP1-72
Perform Main_Exch
Reset the [Auto Op Time]
AP1-62
AP1-63
0%
100%
Fx
Off
On
Stop
Run
Inv State
Main Motor
Main Motor
5min
10min
30min
Operation time
M1(30min) / M2(25min) /
M3(20min)
Pr iority at the moment
M1
M2
M3 /
M4
M5
Pr iority at the moment
M1
M3
M2 /
M4
M5
Pr iority at the moment
M4
M5
M3 /
M2
M1
Supposing its operation in
less than 1minute
AP1-65
AP1-
74
Motor to operate MMC :
M1
, M2, M3
Standby motor : M4, M5
Motor to operate MMC : M3,
M4
, M5
Standby motor : M1, M2
AP1-72
Main Auto Change operation (Op Time Order) when Operable Motor and Standby Motor are set to 3 and 2 each
Option 3: AP1-91: [Interlock DT]
5.44.4 Interlock
When there is motor trouble, the interlock feature is used to stop the affected motor and
replace it with another that is not currently operating (off state). To activate the interlock
feature, connect the cables for abnormal motor signal to the inverter input terminal and
configure the terminals as interlock 1
–5 inputs. Then, the inverter decides the motor’s
availability based on the signal inputs. The order in which the alternative motor is selected is
decided based on the auto change mode selection options set at AP1-55.
Group Code Name
LCD Display Parameter Setting Setting Range Unit
AP1
90
Interlock selection
Interlock
1
0
NO
-
1
YES
After configuring the IN-65
–71 multi-purpose input terminals as Interlock input 1–5, if an
interlock signal is received from an auxiliary motor, the output contacts are turned off for the
motor and the motor is excluded from the MMC operation. This causes the priority level of
the auxiliary motors with lower priority level than the interlocked motor to be increased by 1.
Summary of Contents for LSLV-H100 Series
Page 17: ...Preparing the Installation 4 37 90 kW 3 Phase ...
Page 18: ...Preparing the Installation 5 110 132 kW 3 Phase ...
Page 19: ...Preparing the Installation 6 160 185 kW 3 Phase ...
Page 20: ...Preparing the Installation 7 220 250 kW 3 Phase ...
Page 21: ...Preparing the Installation 8 315 400 kW 3 Phase ...
Page 22: ...Preparing the Installation 9 500 kW 3 Phase ...
Page 35: ...Installing the Inverter 22 ...
Page 50: ...37 Installing the Inverter Input and Output Control Terminal Block Wiring Diagram ...
Page 104: ...91 Learning Basic Features 0 10 V Input Voltage Setting Details V1 Quantizing ...
Page 181: ...168 Learning Advanced Features PID Command Block ...
Page 182: ...169 Learning Advanced Features ...
Page 183: ...170 Learning Advanced Features PID Feedback Block ...
Page 184: ...171 Learning Advanced Features PID Output Block ...
Page 185: ...172 Learning Advanced Features PID Output Mode Block ...
Page 198: ...185 Learning Advanced Features EPID1 Control block ...
Page 199: ...186 Learning Advanced Features EPID2 Control block ...
Page 220: ...207 Learning Advanced Features ...
Page 235: ...222 Learning Advanced Features The Time Chart for the Exception Day ...
Page 506: ...Table of Functions 493 ...
Page 520: ...Table of Functions 507 8 16 4 Cooling Tower MC4 Group ...
Page 549: ...Troubleshooting 536 ...
Page 569: ...Technical Specification 556 11 3 External Dimensions 0 75 30 kW 3 phase 37 90 kW 3 phase ...
Page 570: ...Technical Specification 557 110 185 kW 3 phase ...
Page 601: ...588 ...
Page 602: ...589 ...
Page 603: ...590 ...