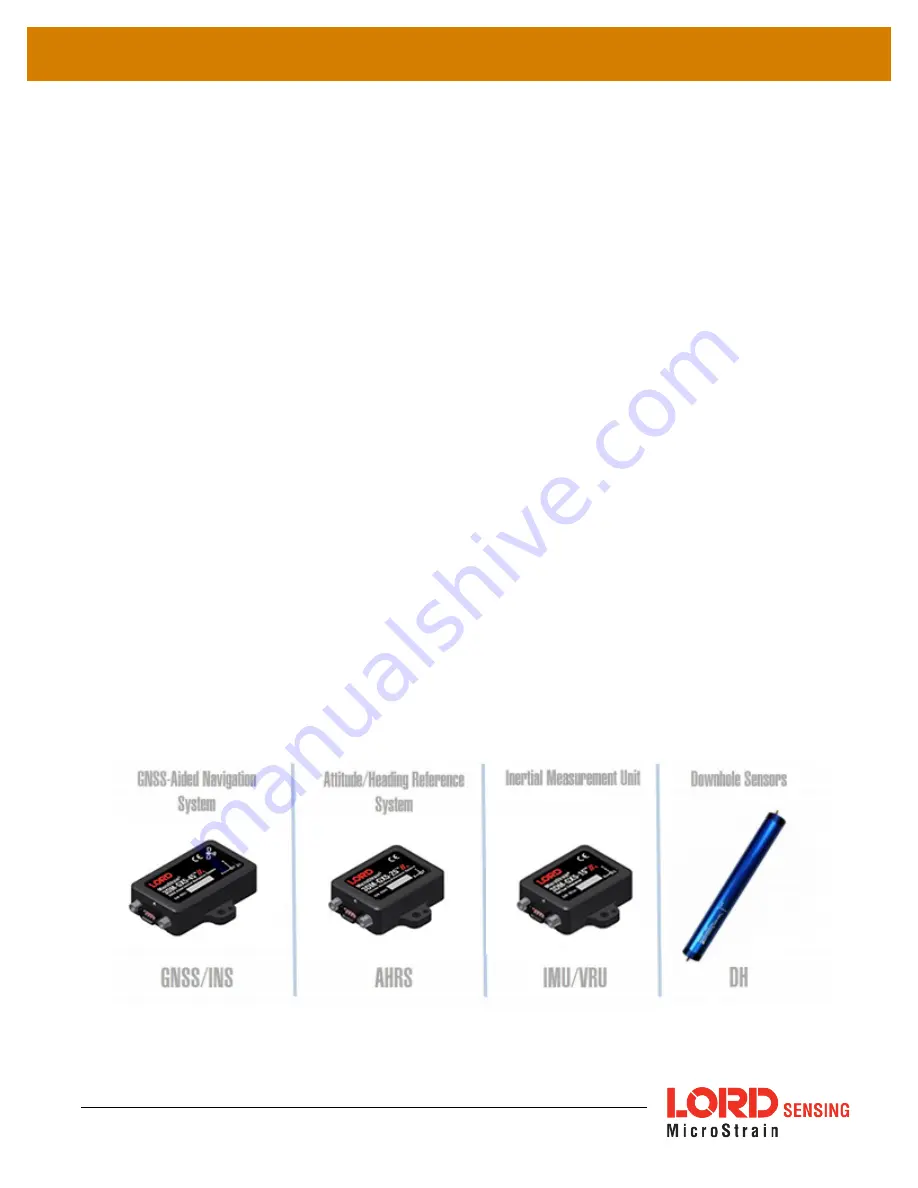
3DM
®
-GX5-10
User Manual
1.
System Family Overview
The LORD Sensing 3DM-GX5 family of industrial-grade inertial sensors provides a wide range of triaxial
inertial measurements and computed attitude and navigation solutions.
In all models, the Inertial Measurement Unit (IMU) includes direct measurement of acceleration and
angular rate, and some also offer atmospheric pressure readings. In models that include a Kalman Filter,
sensor measurements are processed through an Extended Kalman Filter (EKF) to produce highly
accurate computed outputs. The 3DM-GX5 features include extremely stable and low-noise gyros, a new
accelerometer with noise densities as low as 25 µg/√Hz, and a multi-constellation GNSS receiver. The M7
and M4 dual Cortex processors run a new Auto-Adaptive EKF. The Kalman filter enables compensation
for magnetic and linear acceleration anomalies as applicable to the model. It also provides sensor bias
tracking, auto-zero update options (ZUPT), and user adjustable sensor noise factors. All sensors are fully
temperature-compensated and calibrated over the full operating temperature range.
The use of Micro-Electro-Mechanical System (MEMS) technology allows for small, lightweight devices.
Sensors are integrated into customer systems using serial communication protocols such as RS422,
RS232 and USB. The LORD Sensing MIP Monitor software can be used for device configuration, real
time measurement monitoring, and data recording. The LORD Sensing MIP Data Communications
Protocol (DCP) that is used to communicate with LORD Sensing inertial sensors is also available for users
who want to develop customized software solutions. Because of the unified set of commands across the
sensor family, it is easy to migrate code from one inertial sensor to another.
Common applications of LORD Sensing inertial sensor products include vehicle health monitoring,
platform stabilization, down- hole and drilling operations, and inertial navigation systems such as
unmanned air and ground vehicles and personal navigation systems.
5