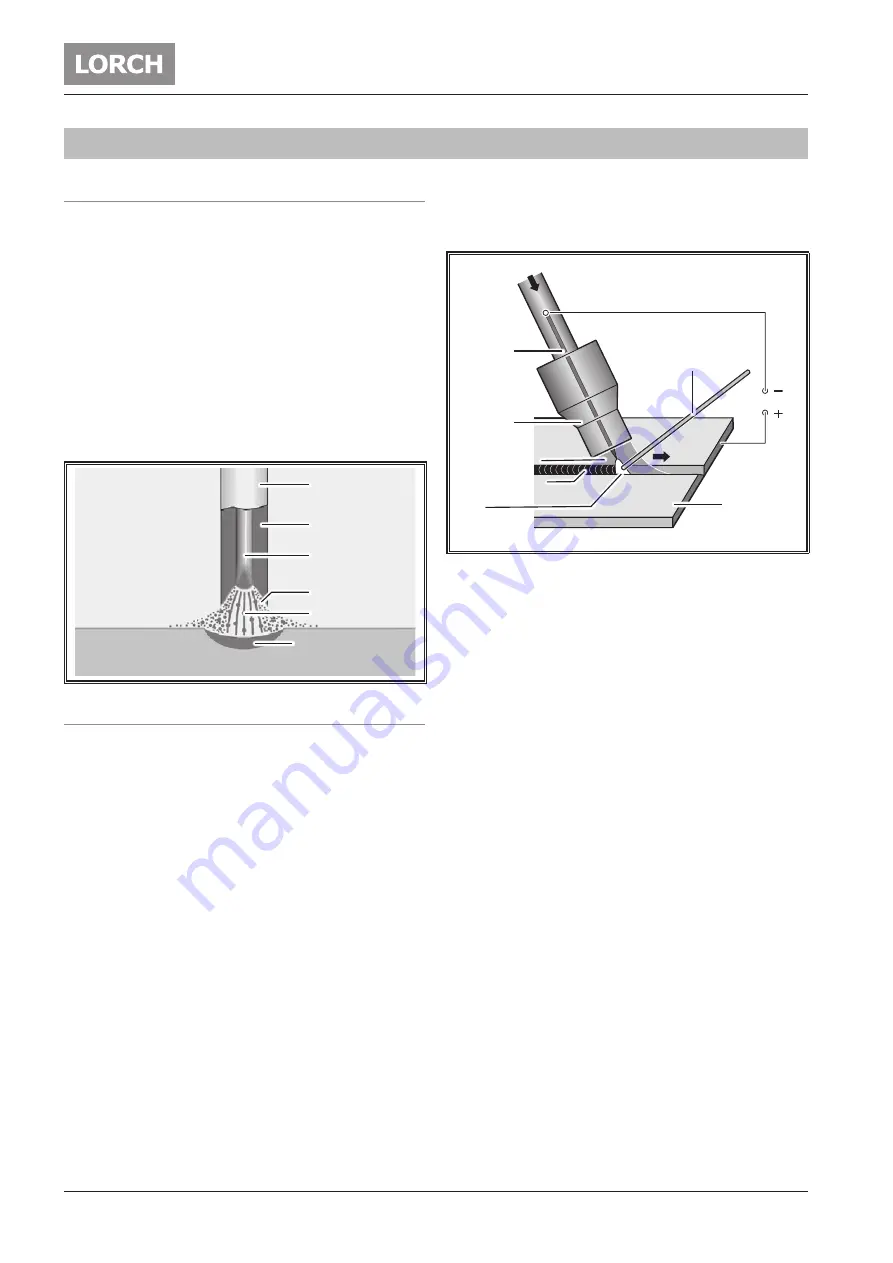
Welding basics
- 20 -
11.18
909.1550.1-08
15
Welding basics
15.1 Stick electrode welding
Coated stick electrodes are used for the widely-used
manual metal arc welding process (stick electrode weld-
ing). The coating of the electrode melts off during the
welding process together with the core wire. The coating
generates the shielding gas. Additionally the burning-
off coating compensates alloy elements, which are de-
stroyed in the molten pool. A slag layer forms on top of
the welding seam, which covers and protects the cooling
welding seam against the air.
The coatings of the electrodes differ according to thick-
ness and type, i.e. chemical composition. This results in
different welding properties and consequently different
applications for the electrodes. Types and nomenclature
are defined in DIN EN 499 (formerly 1913).
Stick electrode
Arc
Coating
Core rod
Gas/slag
Molten zone
Base metal
15.2 TIG welding
The TIG welding process is a universally-applicable
process which creates high quality joints.
The electrode of the TIG process consists of non-melting
tungsten, the shielding gas is an inert gas. In English us-
age we speak of TIG welding ("Tungsten“ = Wolfram).
Inert gas is chemically neutral and does not react with
the weld metal. Inert gases are, e.g. argon, helium and
their mixtures. Usually pure argon (99.9%) is used. The
welding gas must be dry. DIN 32 526 defines the differ
-
ent types of shielding gas.
TIG welding process basics
A non-melting tungsten electrode is clamped with a col-
let into a gas or water-cooled torch. The arc burns be-
tween the tungsten electrode and the workpiece in an
inert shielding gas atmosphere. Thus the tungsten elec-
trode acts as an arc carrier. The arc melts the workpiece
point by point and forms the weld pool. The shielding gas
escapes through the gas nozzle. This gas protects the
tungsten electrode, the arc and the molten pool against
the surrounding air. This prevents undesired oxidation.
Consequently, poor welding results may occur due to
trouble with the shielding gas supply.
In case additional filler material is required, filler wire
is supplied either manually, as in gas flame welding, or
automatically by means of a cold wire feeder. The filler
wire must be equally or more highly alloyed than the
base material. Flange and corner welds can be created
easily without filler wire.
Shielding gas
Tungsten
electrode
Gas nozzle
Shielding gas
Welding seam
Workpiece
Power source
Arc
Filler wire
Basically, both DC and AC may be used for TIG welding.
The current mode and polarity depend on the material to
be welded.
Non or low-alloyed steel, high-alloyed steel and copper,
as well as titanium and tantalum are welded with DC.
The electrode is connected at the minus pole because of
the stronger current loading.
When welding aluminium and magnesium as well as
their alloys, AC must be used in order to tear up the high-
melting and tough oxide skin which forms on the molten
pool or which is present on the base metal. If the oxide
skin is missing, e.g. there has been welding on the same
part for a longer time, the arc can be unstable or break
up from time to time.
Shape of the electrode tip
Tungsten electrodes always have to be ground length-
wise because crosswise grinding marks cause an un-
steady arc.