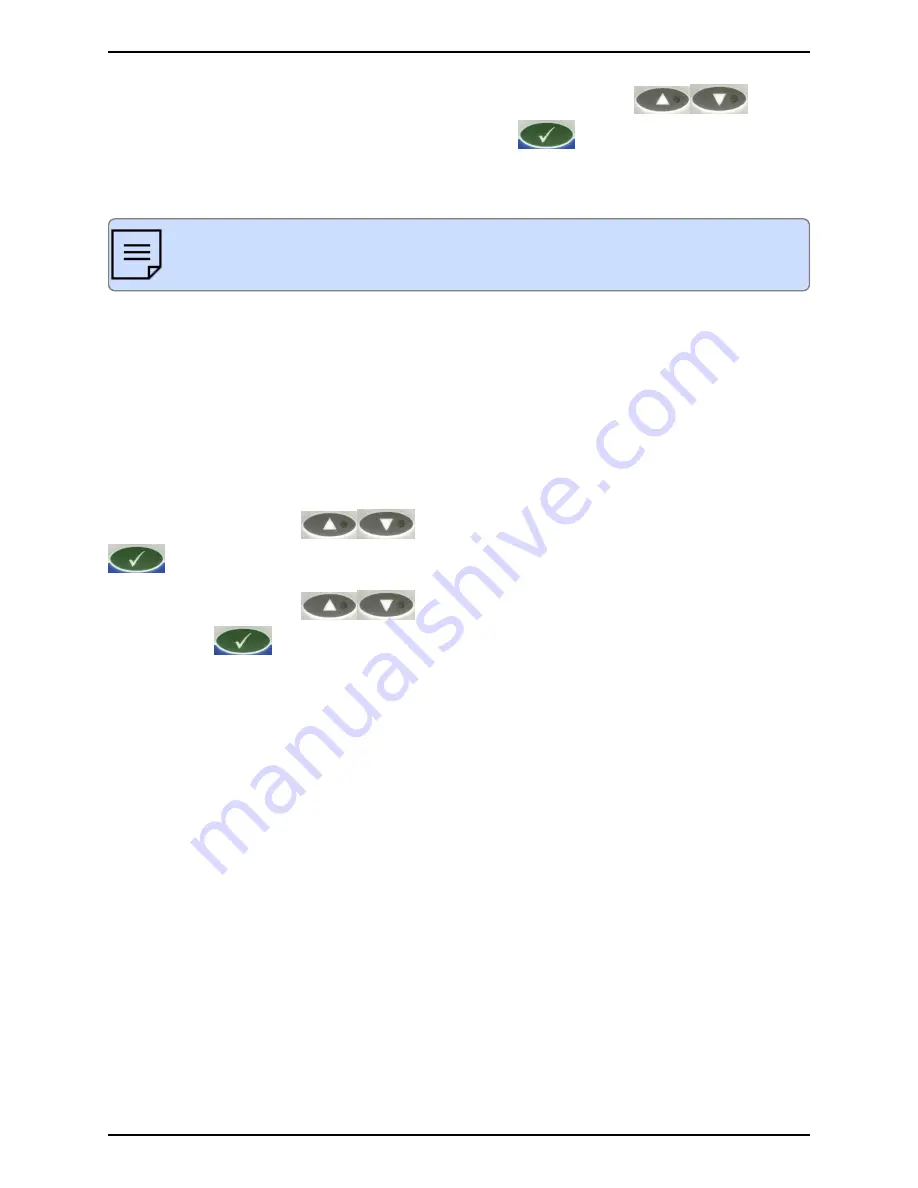
Operating Instructions
58
Copyright © Loma Systems
Original Document
4. Navigate to the Menus > Change menu, then use the Navigation Keys
to
display the Ferrite F product and press the OK / Enter Key
to select it.
5. Perform a Full Learn whilst moving the end of the ferrite wand with the sample in and out of the
search head; taking care not to put your hand in or get any watches/rings near the search head.
On systems fitted with a Product Registration Photo-eye, block the photo-eye to
register that packs are present.
6. Once a successful Learn has been completed, navigate back to the Menus > Service >
Options menu and de-select the Access Ferrite option.
You have now completed the Ferrite Tune process.
4.15 Setting Up the Reject Options
To set up the reject options, proceed as follows:
1. Select Menus > Service > Reject > Set Up to display the Reject Set Up menu options which are
listed and described below.
2. Use the Navigation Keys
to select each option in turn press the OK / Enter Key
to enable the value to be edited.
3. Use the Navigation Keys
to select the required option value and then press the
OK / Enter Key
to confirm the selection.
4. Repeat step 2 and 3 until you have selected and confirmed values for each option.
The Reject Set Up menu options available are as follows:
Mode
The following Mode options are provided for selection:
l
Pulse (only available if a photo-eye is fitted)
If this option is selected, when a contaminated package is detected the reject delay time is
counted down, in order for the package to travel from the photo-eye to the reject device,
where-upon the reject is turned on for a time equal to the reject dwell time. Typically, this mode
of reject would be used for air blast or pusher type rejects for the accurate rejection of small
packages at high speed.
l
Pulse Extension
This option provides the same functionality as the Pulse option, except that the dwell time is
extended if a second contaminated product reaches the reject point before the dwell time
from the first contaminated product has timed out. This could typically be used with an air blast
or retracting band reject device, but not a pusher type device. This reject mode is always
available.
l
Toggle (only available if a photo-eye is fitted)
Summary of Contents for IQ3X
Page 2: ...Version Number Date Reason 1 29 07 2019 Initial Release ...
Page 28: ...Thispage intentionally left blank ...
Page 33: ...33 Operating Instructions Original Document Copyright Loma Systems 3 9 IQ3X Display Menu Map ...
Page 38: ...Thispage intentionally left blank ...