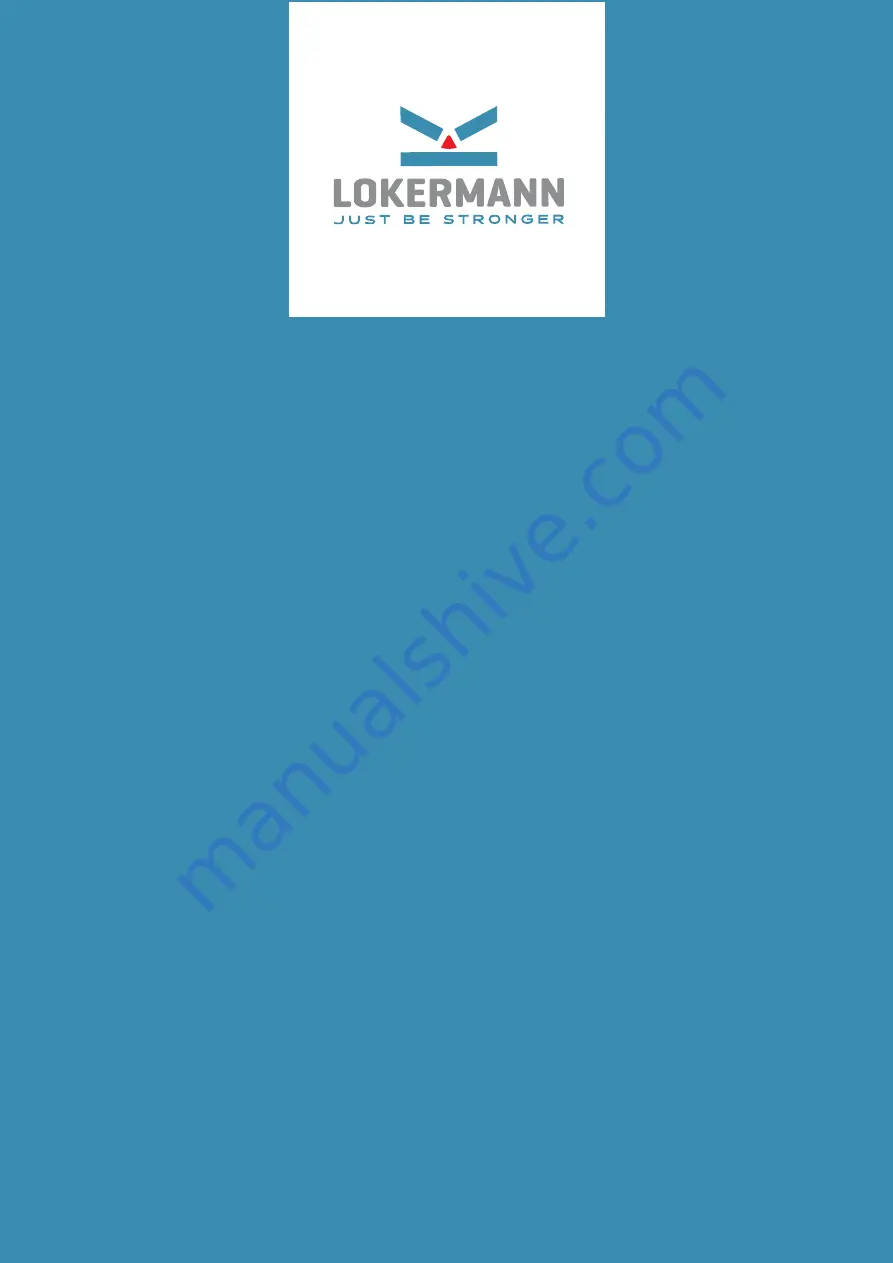
USER MANUAL
INVERTER Based Welding Machines
GRAND MIG
200 MULTI
PFC SYN MV
IMPORTANT
: Read this OPERATOR MANUAL together
with PRESCRIPTION AND COMPLIANCE MANUAL before
to use this equipment. In case of loss one of two parts
contact immediately your dealer.
Allow the operator to consult this manual.