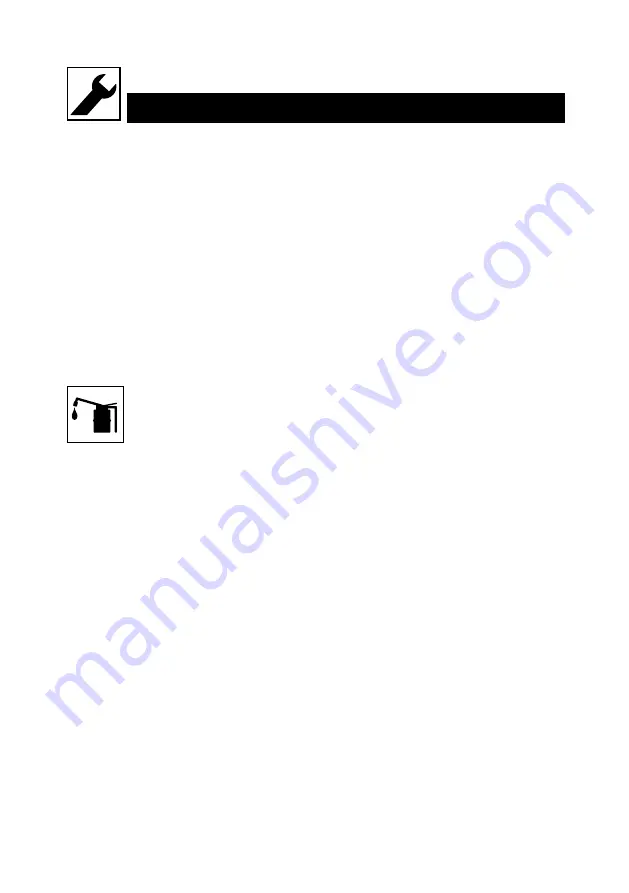
21
6.0 Long live the Rotator
Regular inspection and the replacement of worn or defective parts in good time will
prolong the life of the Rotator. “Prevention is better than repair”, therefore ensure:•
• Check battery every 14 cycles
• Correct usage
• Regular cleaning
• Periodic safety and service inspection (see the back page)
Due to safety reasons, the below points have to be checked every 3 months:
• Loose screws and nuts have to be tightened up.
• Breaches, cracks or deformations are not allowed on the load-bearing parts.
• Wearing parts, such as brakes, wheels and bearings, are to be adjusted or
changed continuously
6.1 Lubrication and hydraulic oil
Under normal operation conditions the Rotator requires no lubrication.
All ball bearings are sealed and lubricated for life, and moving parts
have self-lubricating bearings or are treated with grease.The hydraulic
system is filled with hydraulic oil of viscosity class ISO VG 15.
An additive is added to the oil. The concentrate reduces friction and
wear and protects against corrosion. Pre-mixed hydraulic oil with
additive is available from the dealer. The oil is suitable for use in the temperature
range -10 to +50° C. A thinner oil is recommended for temperatures lower than -10°
C (if necessary, contact your dealer).
6.2 Oil change
Draining the oil:
1. Bring the unloaded forks down to the lowest position.
2. Most of the oil can be drained by loosening the hydraulic hose union and
briefly activating the hydraulic pump with the switch.
3.
The remaining oil can be drained from the oil tank by taking off the twelve clips
on the pump and removing the tank.
Oil filling:
4.
Fill oil through the filling hole on the tank.
5. Oil quantity:
ELFR 920 & ELFSR 890
approx. 1,5 liter
ELFR 1200 & ELFSR 1170
approx. 3 liter
ELFR 1400 & ELFSR 1370
approx. 3 liter
ELFR 1600 & ELFSR 1570
approx. 3 liter
ELFR 1910 & ELFSR 1880
approx. 4 liter
6.
Refit the angular hose nipple and bleed the system (see. 6.3).
Summary of Contents for ROTATOR ELFR
Page 1: ...ROTATOR ELFR ELFSR_ELFRA ELFSRA...
Page 31: ...31...