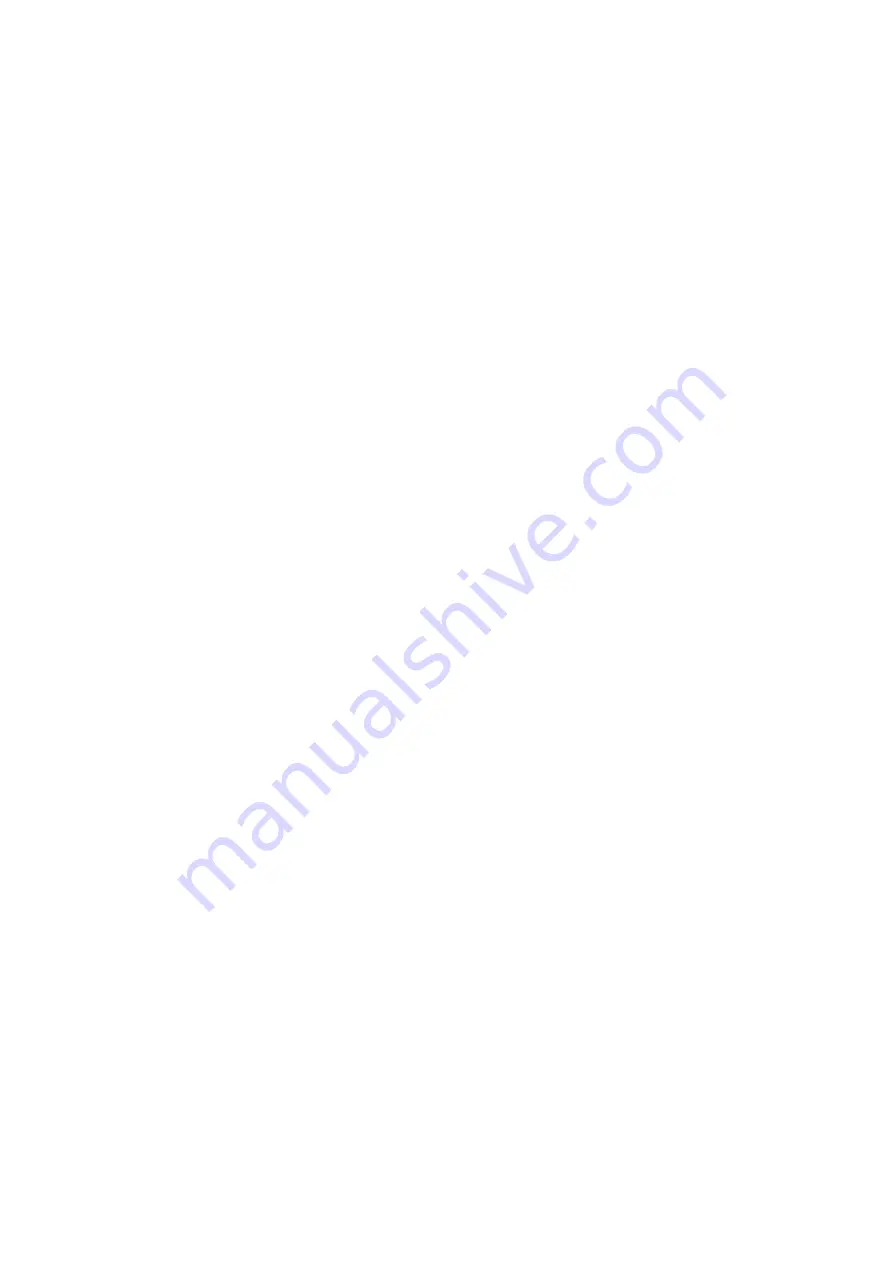
26
12.4.3
PROCEDURE FOR INITIAL LIGHTING
IF THE UNIT IS TO OPERATE ON LPG REFER TO SECTION 13: LPG FUEL BEFORE PROCEEDING
1.
Ensure that the gas inlet appliance isolating valve, provided by the installer, is in the ‘off’ position.
2.
Remove the control cover (located above the water flow and return header). Set the thermostat to a
temperature above that of the system water.
3.
Press the power rocker switch located below the thermostat dials to bring the equipment on.
4.
The burner should try to fire and a spark should be visible by looking at the pilot assembly. As the gas
inlet appliance isolating valve is closed, the controls should go to a flame failure condition.
5.
If the above occurs correctly, open the gas inlet appliance isolating valve and press the flame failure
reset button, positioned above the rocker switch.
6.
After a short delay, the pilot should ignite and the main gas valve should energise lighting the main
burners.
NOTE: During initial warm-up, condensation may drop onto the burners. This will continue until the system
water reaches a temperature above 50°C.
7.
Allow the system to reach temperature to check operation of the control thermostat.
8.
Once the thermostat has been satisfied, check that the main burner and pilot burner flames have
extinguished.
12.4.4
GAS PRESSURE ADJUSTMENT AND COMBUSTION CHECKS
1.
After the burner has operated for approximately 10 minutes, switch off the equipment.
2.
Open the pressure test point on the inlet side of the gas valve, attach a manometer and check the
standing gas-inlet pressure.
3.
Relight the appliance and check the operating gas-inlet pressure
NOTE: The equipment has been designed to conform to the requirements of the Gas Appliance (Safety)
Regulations (1992). For Natural Gas the gas pressure governor control system is configured for a
nominal gas inlet pressure of 20 mbar, with a maximum inlet pressure of 25 mbar. Information relating
to propane firing can be found in Section 13: LPG FUEL.
4.
Switch off the appliance, remove manometer and close pressure test point.
5.
Open the pressure test point on the outlet side of the gas valve and attach a manometer.
6.
Relight the appliance and check the burner pressure.
7.
If required, the burner pressure can be corrected by removing the dust cap with a large slotted
screwdriver and the adjusting screw turned clockwise to increase burner pressure or counter-clockwise
to decrease burner pressure. Details of the correct burner pressure can be found in Table 3.1
NOTE: A second gas control valve is fitted to the MC501CE model, this must also be adjusted in accordance
with the procedure taken for the first valve. Remember to shut all test points after removing the
manometer.
NOTE: If the dust cap is removed, once reinstalled it should be marked with an anti-tamper indicator.
8.
Carry out a spillage test in accordance with BS5440-1.
9.
Carry out a combustion analysis. Record all readings for future reference on a relevant
commissioning sheet.
Summary of Contents for Mini Copper-Fin MCB136CE
Page 36: ...36 ...