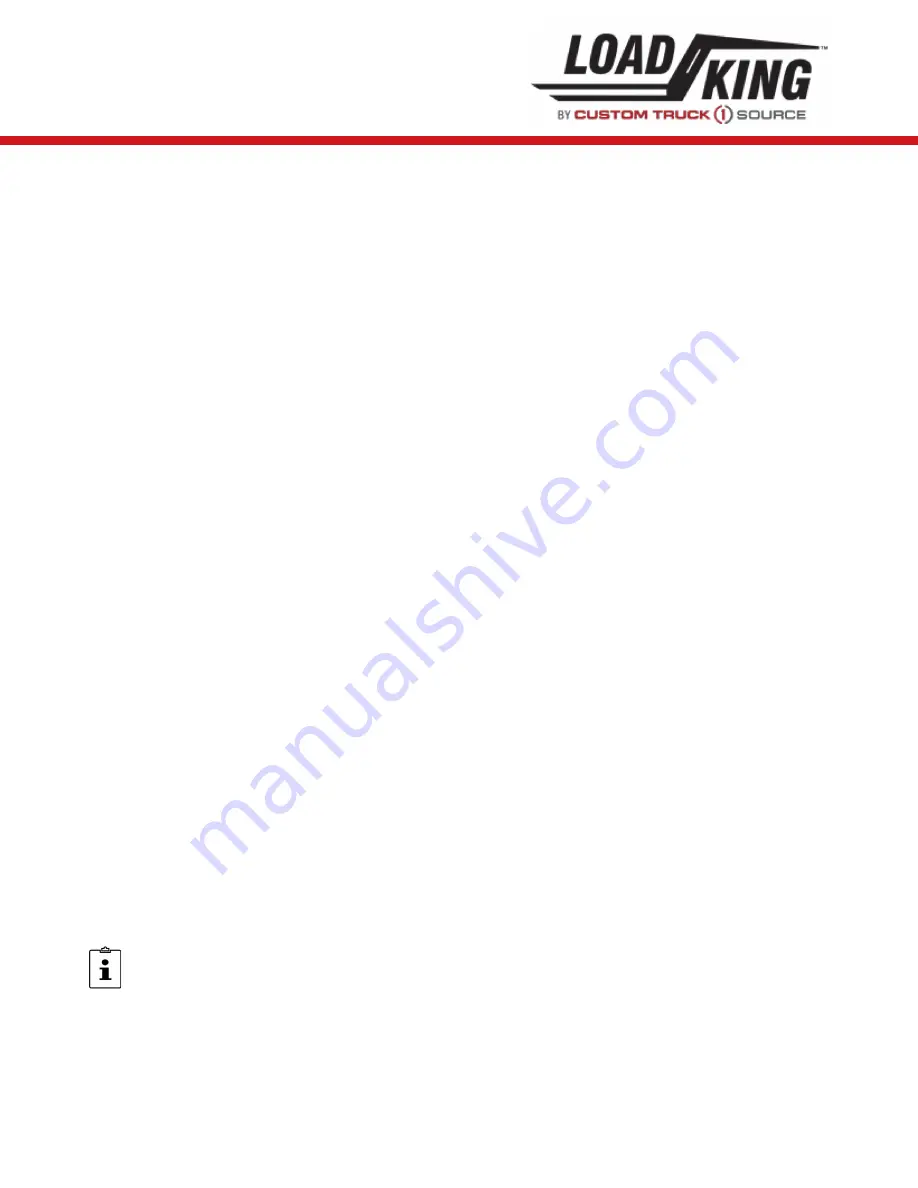
293
Chrome Cylinder Rod Storage
Hard chrome plating is primarily applied to steel cylinder rods for its wear resistant properties, although
it does provide considerable corrosion resistance as well. Once the chrome-plated rod is assembled into
a cylinder and put into service, the hydraulic fluid on the surface of the rod provides all the corrosion
resistance required for the rod during its life cycle. As a cylinder cycles, hydraulic fluid is driven into any
surface cracks that exist in the chrome plate. When these cracks are filled with hydraulic fluid, moisture
or corrosive fluids can not penetrate the cracks. However, some machining and cleaning operations can
negatively impact the future corrosion resistance of chrome-plated shafting. For example, additives
such as chlorine, sulfur, and sodium found in Extreme Pressure (EP) coolants and some washing solutions
are known rust accelerates and can strip chrome plating from the base metal. Cleaning processes, such
as phosphate washing are also known to be detrimental to the corrosion resistance of hard chrome
plated shafting.
If the rod is not periodically cycled and is subject to a corrosive environment, moisture and oxygen can
work its way down through the chrome layer and begin to corrode the base metal. Brand new equipment
may be stored outside for a considerable period of time at the equipment dealership before it is sold.
During these times, a protective barrier must be applied to the exposed cylinder rod. This protective
barrier will preserve the integrity of the chrome plating by preventing the elements of corrosion from
getting to the metal substrate.
Cylinders should be stored in the retracted position, if at all possible. The steps outline below cover the
procedures to be followed for Protecting New Equipment from corrosion if it must be stored in the
extended position:
1. Position the equipment as it will be stored and identify all the exposed portions of the chrome
plated cylinder rods.
2. Clean any dirt and dust from the exposed portions of the cylinder rods using a dry cloth or a cloth
which has been dampened with an appropriate solvent. Do not use caustics or acids.
3. Apply a thin coating of 1“Ferro-Kote 5856-BF” to the exposed surfaces of the chrome plated
cylinder rods. The Ferro-Kote may be thinned using a 40% Kerosene or No. 1 fuel oil mixture.
4. Inspect the cylinder rod surfaces and reapply at three to six month intervals.
5. If the equipment is to be moved and then stored again for an extended period of time or if the
cylinder is cycled, steps 1 through 4 should be repeated for all cylinder rods that were exposed.
For the protection of Older Equipment that is to be stored, the procedure outlined above can be used,
but greater attention to cleaning the exposed portions of each cylinder rod is required. Solvent applied
with plastic or copper wool can be used, but abrasives such as sandpaper should never be used to clean
the exposed surfaces of the cylinder rod. If surface damage to the chrome plate is discovered, the
frequency of corrosion barrier applications should be increased.
1
Ferro-Kote 5856-BF is a product of Quaker Chemical Company, Conshohocken, PA 19428
NOTE:
Caution must be used when cleaning equipment in service with high pressure washes.
Soaps or chemicals containing chlorines or other corrosive elements should be avoided. Cylinders
should be cleaned in a retracted position as not to expose rods to the chemicals. Cylinders should
be cycled immediately following the wash. If rods are to be stored in the extended position, refer to
steps 1-4 above.
Summary of Contents for 80-160
Page 1: ...OPERATORS MANUAL LOAD KING 80 160 REV B DECEMBER 2020...
Page 2: ...Page Intentionally Blank...
Page 18: ...Page Intentionally Blank...
Page 26: ...26 80 160 Safety 80 160 Safety Sign Locations Right Hand Side View Left Hand Side View...
Page 27: ...27 Rear View Front View...
Page 28: ...28 80 160 Safety Upper Cab...
Page 70: ...70 80 160 Safety Access Egress Rear...
Page 98: ...98 80 160 Assembly...
Page 118: ...118 80 160 Description Of Machine and Controls Lifting controls screen Cab controls screen...
Page 124: ...124 80 160 Description Of Machine and Controls 1 1 PTO Engage Switch...
Page 137: ...137 REPAIRS ADJUSTMENTS REMARKS ITEM REQUIREMENT DATE...
Page 155: ...155 OBSERVE CAUTION NOTES ON OUTRIGGER MOVEMENT WHENEVER SETTING UP OR STOWING OUTRIGGERS...
Page 206: ...Page Intentionally Blank...
Page 209: ...209 8 Install the pin 5 in the guide sheave kickstand 5 9 Remove the lower left hand pin 7 7...
Page 257: ...257 Master Lubrication Chart 13 14 5 4 3 2 2 8 12 9 7 6 15 10 11 BOOM BLOCK TOP VIEW...
Page 300: ...Page Intentionally Blank...
Page 326: ...Page Intentionally Blank...
Page 331: ...331 Repairs Adjustments Remarks Log ITEM REQUIREMENT DATE...
Page 333: ...333...
Page 354: ...Page Intentionally Blank...
Page 362: ...362 80 160 Appendix...
Page 366: ...80 160 Notes...
Page 369: ...80 160 Operator Manual...