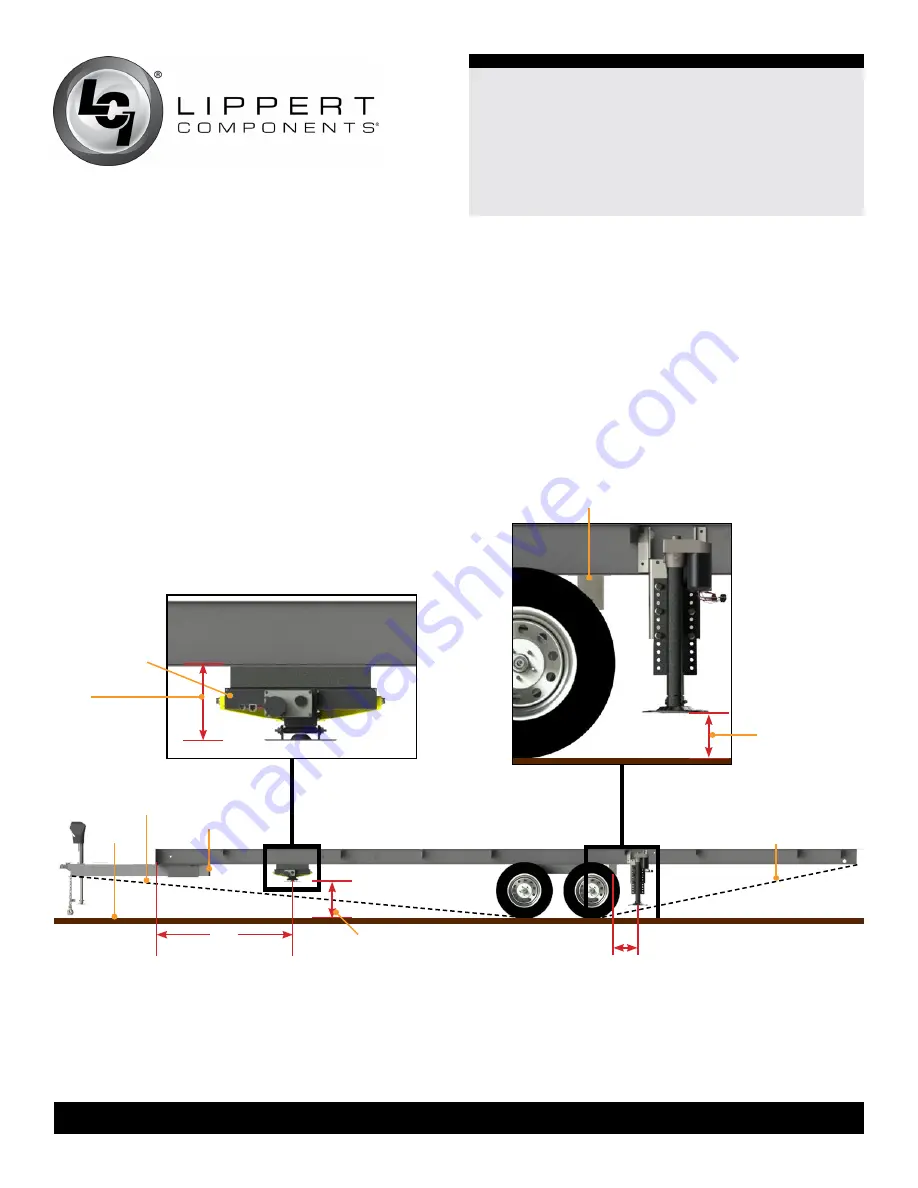
6
574-537-8900
Rev: 03.02.21
Ground Control
®
TT
Leveling OneControl
®
Touch Panel
(3K-5K)
Installation and Owner’s Manual
(For Aftermarket Applications)
CCD-0002700
Measuring Departure and
Approach Angle
Before checking ground clearance make sure the trailer is
level front-to-back.
Departure and approach angles are measured by running
a string line from the meeting point of the tire and ground
up at an angle to the lowest point on the front or rear of the
trailer. These string lines are shown as dotted lines
(Fig.1)
.
Measure from the front of the frame and make a mark at
60”. This will be the maximum allowable distance for the
location of the center of the C-Jack footpad. The final
location should be as close to the draw bar as possible,
staying within the approach angle
(Fig.1)
.
Fig.1
C-jack shown
for reference
only to mark
9
1/2
”
clearance
above the
string line
is required
departure angle
string line
ground
approach angle
string line
draw bar
60”
maximum
distance
12”
maximum
distance
Measure 12” from the center of the rear axle hanger to the
center of the rear 5K short jack footpad. This will be the
maximum allowable distance for the location of the center
of the 5K jack footpad. Make sure the jack footpad is within
the departure angle
(Fig.1)
.
NOTE:
Before checking ground clearance make sure the
trailer is level front-to-back.
10.5” to 15”
ground clearance
7” minimum
ground clearance
axle hanger