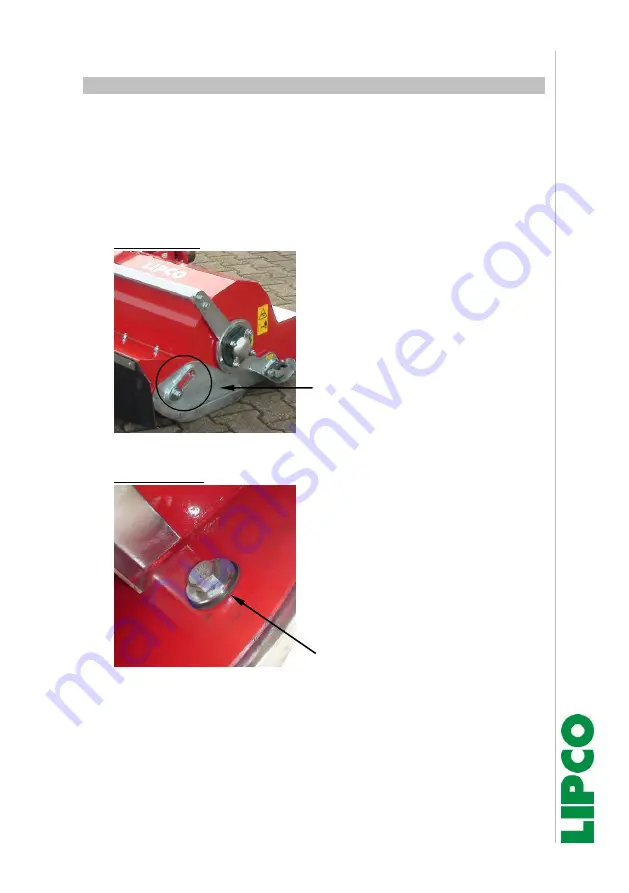
Instructions
Flail mower ME 70/80/90/104/120/140..L
23 - 40
110725-E-03-EN BA ME-70-80-90-104-120-140-L / 05/11/2019
12. Assembly of blade shaft
The assembly of the blade shaft is done in reverse order of re-
moval.
Make sure that both skids are running smoothly in the adequate
guiding’s, thus avoiding sticking.
Skid guiding:
Make sure that both skids are
running smoothly in the ade-
quate guiding’s, thus avoiding
sticking.
Skid guiding
Führung Kufe (2x)
Fig. 15
Rubber plate:
Make sure that inside under the
washer of the skid guiding, the
appropriate rubber disk is rein-
stalled.
This reduces vibration and noise
and counteracts the wear.
Rubber plate
Führung Kufe (2x)
Fig. 16
Check after installation of the blade shaft and all related fittings
the alignment of the two pulleys and the belt tension.
Summary of Contents for ME 104 L Series
Page 40: ...40 40 Design mail bauer ib com...