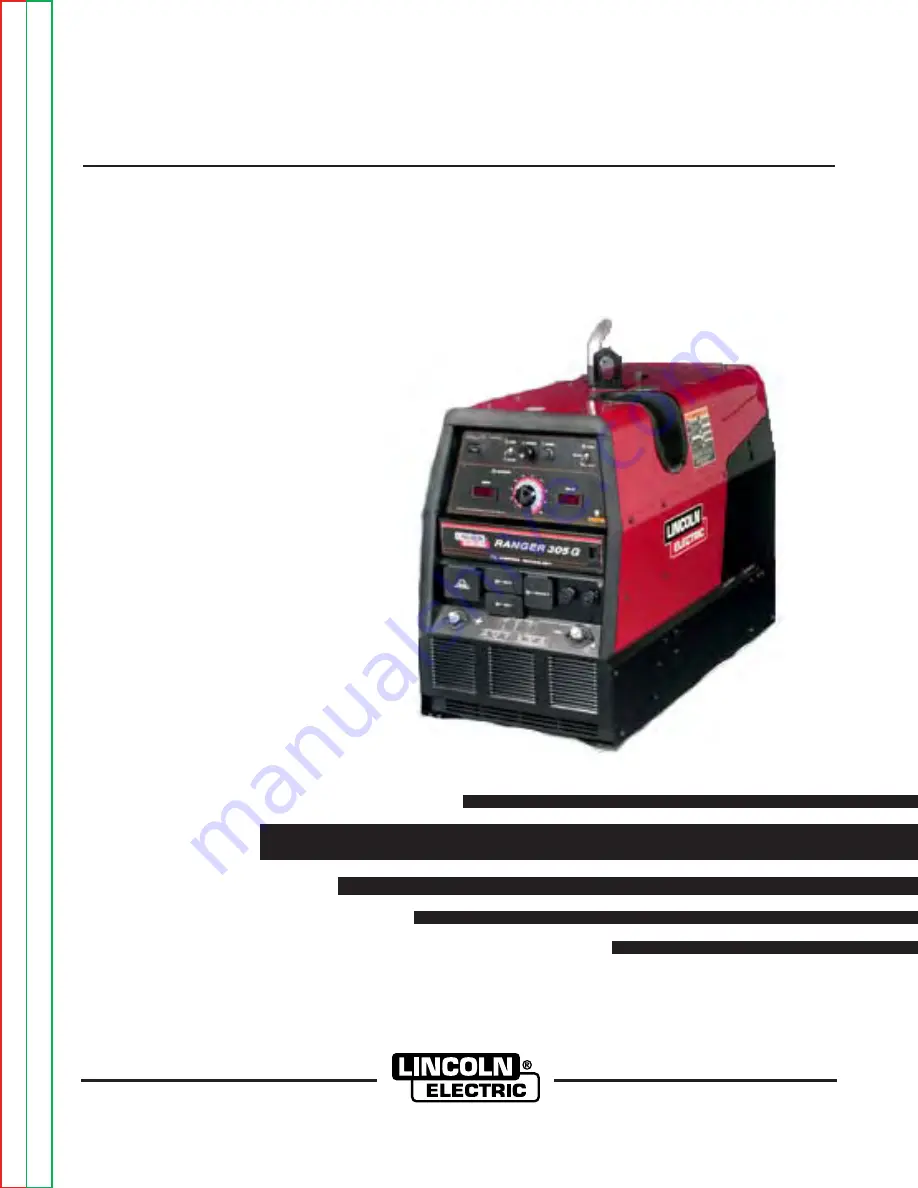
SVM175-A
July, 2007
Safety Depends on You
Lincoln arc welding and cutting
equipment is designed and built
with safety in mind. However,
your overall safety can be in-
creased by proper installation . . .
and thoughtful operation on
your part.
DO NOT INSTALL,
OPERATE OR REPAIR THIS
EQUIPMENT WITHOUT
READING THIS MANUAL AND
THE SAFETY PRECAUTIONS
CONTAINED THROUGHOUT.
And, most importantly, think
before you act and be careful.
SERVICE MANUAL
For use with machines having Code Numbers:
10926, 11121, 11188, 11275
(Domestic)
11027, 11122, 11189, 11314
(UK)
11039, 11123, 11190, 11315
(EUROPE)
Ranger 305D
TM
Retur
n
to
Master
TOC
Retur
n
to
Master
TOC
Retur
n
to
Master
TOC
Retur
n
to
Master
TOC
V
iew
Safety
Info
V
iew
Safety
Info
V
iew
Safety
Info
V
iew
Safety
Info
• Sales and Service through Subsidiaries and Distributors Worldwide •
Cleveland, Ohio 44117-1199 U.S.A. TEL: 1-888-935-3877 FAX: 216.486.1751 WEB SITE: www.lincolnelectric.com
• World's Leader in Welding and Cutting Products •
DD
Copyright© 2007 Lincoln Global Inc.